Precision Panel Saw requirements: work, work should ensure that fixed profile positioning in line to eat cutting direction to avoid abnormal cut, do not exert side pressure or curve cutting, feed abrasive grinding
wheels to a smooth, avoid contact with the workpiece edge impact resistance, resulting in blade breakage, or workpiece flying out of an accident. Work, we found that abnormal sound and vibration, cutting surface roughness, or odor, you must immediately terminate the job, timely inspection, troubleshooting to avoid accidents. Cutting and stop cutting at the beginning, do not feed too fast to avoid broken teeth and damaged. If the cutting aluminum or other metal, to General purpose
blade use special cooling and lubrication fluid, to prevent overheating of the blade, resulting in tooth paste, and other damage, affecting the cutting quality. Flutes and suction equipment to ensure smooth flow of slag device to prevent slag accumulation into blocks, affecting production and safety. Dry cutting, do not long continuous cutting, so as not to affect the life of the blade and the cutting effect; wet sheet cutting, water jet cutting should be added, to guard against leakage.
Precision Panel Saw Blade Maintenance:Saw If not concrete saw blades used immediately, it should be flat or use the hole to hang up, the blade can not be stacked horizontally with other items or foot, and pay attention to moisture and corrosion. When the blade is no longer sharp cutting surface roughness must be promptly re-grinding. Grinding can not change the original angle, and destruction balancing. Blade diameter correction, positioning hole machining, etc., must be carried out by the factory. If the processing is bad, will affect the product effect, and may be dangerous, reaming in principle can not exceed the original diameter 20mm, so as not to affect the balance of stress.
diamond core drills, not only in geological exploration has an important position, but also because it has got speed, stone loss, does not destroy the surrounding environment and other unique advantages and is widely used in marble, granite, reinforced concrete walls of the drill hole
PCD grinding wheel
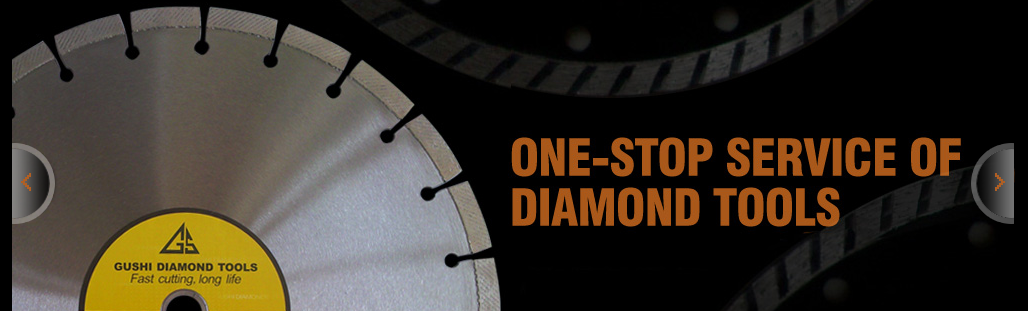
2013年9月29日星期日
varieties of diamond cutting tool material classification
Diamond tool material is divided into single-crystal diamond (there are two kinds of natural and man-made, natural single crystal diamond expensive part is single crystal synthetic diamond substitute), synthetic polycrystalline diamond (PCD) and synthetic polycrystalline diamond and carbide composite blade (PCD / CC) and CVD diamond.
Single crystal diamondSingle crystal diamond cutting tool must be used for large particles (mass greater than 0.1g, the best path length not less than 3mm), mainly used in surface roughness, geometry, high precision and dimensional accuracy requirements
Single crystal diamondSingle crystal diamond cutting tool must be used for large particles (mass greater than 0.1g, the best path length not less than 3mm), mainly used in surface roughness, geometry, high precision and dimensional accuracy requirements
cutting discs of precision and ultra precision machining applications fields. Natural diamond single crystal diamond is the most wear-resistant material. Fine texture of its own, after fine grinding, cutting edge edge edge radius as small as 0.008 ~ 0.005μm. But more brittle natural single crystal diamond, the crystal anisotropy, different surfaces or in the same plane of the crystal in different directions were different hardness, during grinding and use must choose the right direction. The use of harsh conditions, coupled with natural single crystal diamond resources are limited, the price is very expensive, so they use a production PCD, PCD / CC and CVD diamond tools. Some natural single crystal diamond is mainly used for ultra-precision machining non-ferrous metals or gold jewelry production.Synthetic single crystal diamond the size, shape and performance are in good agreement, present due to high pressure technology matures, a certain size concrete saws can be prepared by synthetic single crystal diamond, especially in the processing of high wear-resistant laminated wood, it performance than PCD diamond cutting edge will not cause premature passivated.Synthetic polycrystalline diamond (PCD) and synthetic polycrystalline diamond and carbide composite blade (PCD / CC)PCD is at high temperature (about 1800 ℃), pressure (5 ~ 6MPa), the use of cobalt and other metal binding agent to a number of polycrystalline diamond crystal powder polycrystalline material, although slightly lower than the hardness of a single crystal diamond, but it is randomly oriented diamond grains polymerization, is isotropic, as can be arbitrarily oriented cutting tool sharpening, no natural diamond that must be selected as the best cleavage plane as a rake. In cutting, the cutting edge is very sensitive for accidental damage, wear resistance is also strong, long stay sharp cutting edge, can be used when machining high cutting speed and larger cutting depth (to eat deep) , life is generally higher than the WC-based cemented carbide cutting tools 10 to 500 times, and because the metal binding agent PCD has conductivity, making PCD easy to cut to shape, and is a rich source of raw materials, the grinding cup wheels price is only a few tenth of natural diamond a fraction of the ten have become traditions WC-based cemented carbide cutting tools, high-performance alternatives.PCD inserts to improve the toughness and weldability in the cemented carbide substrate, sintered or pressed on the surface of 0.5 ~ 1mm thick layer of the composition of PCD diamond composite blade (PCD / CC). PCD / CC welding or machine folder available way of making knives. Due to its good weldability, regrinding easy, low cost, and therefore widely used. Hereupon, PCD and PCD / CC sharp cutting edge of the tool and are not as good surface quality single crystal diamond, while its workability is poor, the grinding ratio is small, it is difficult according to the geometry of any shape head, still not easy to manufacture with chipbreakers indexable end mills and other geometric shapes and complex products.
2013年9月28日星期六
[ Alloy saw brand ] diamond saw cutting knowledge
1 , idle : in particular, the first use of a new base , the need to idle for about 30 minutes , the summer hot season needs to bring water idling , which aims to further eliminate welding head when matrix effects and enhanced blade rotating at high speed state to maintain the intrinsic quality of memory.
2 , blocks of not less than 0.5m3, and carbide tipped saw blade placed securely , the bottom should be well- wood pad , plug SUCOOT prison , blocks should be located in symmetrical positions workbench , workbench cars and blocks to ensure the stability , without shaking , shaking phenomenon .
3 , according to the blocks of length, width, height adjusting limit switch, the blade lift and skip the trip in a reliable and effective range. Saw blade should leave before sawing blocks up to 10 ~ 20mm. After sawing , saw cut should be left away from the blocks at the bottom of 20-40mm, knife blade to go about running , you should exit all blocks Jukou the blade from not less than 150-200mm, to prevent the blade hit Shortage material .
4 , the blade idling stable only after a trial cut turbo diamond blade blocks are not allowed contact with the blade starts cutting edge blade , cutting blade rotation are not allowed to stop , to withdraw Jukou before stalling .
5 , cutting blocks are shaking if found should immediately stop cutting the blocks to be firmly fixed before it can continue working , cutting , are not allowed to move in any blocks.
6 , the cutting blade and hole saw blades found a significant slowdown or even clip knife phenomenon , it may be belt slippage , compression nut loose or too large depth of cut , the cutting speed is too fast and other reasons, should be timely adjusted .
7 , the line speed should be processed stone hardness and wear resistance to adapt, line speed table are recommended cutting different types of stone .
2 , blocks of not less than 0.5m3, and carbide tipped saw blade placed securely , the bottom should be well- wood pad , plug SUCOOT prison , blocks should be located in symmetrical positions workbench , workbench cars and blocks to ensure the stability , without shaking , shaking phenomenon .
3 , according to the blocks of length, width, height adjusting limit switch, the blade lift and skip the trip in a reliable and effective range. Saw blade should leave before sawing blocks up to 10 ~ 20mm. After sawing , saw cut should be left away from the blocks at the bottom of 20-40mm, knife blade to go about running , you should exit all blocks Jukou the blade from not less than 150-200mm, to prevent the blade hit Shortage material .
4 , the blade idling stable only after a trial cut turbo diamond blade blocks are not allowed contact with the blade starts cutting edge blade , cutting blade rotation are not allowed to stop , to withdraw Jukou before stalling .
5 , cutting blocks are shaking if found should immediately stop cutting the blocks to be firmly fixed before it can continue working , cutting , are not allowed to move in any blocks.
6 , the cutting blade and hole saw blades found a significant slowdown or even clip knife phenomenon , it may be belt slippage , compression nut loose or too large depth of cut , the cutting speed is too fast and other reasons, should be timely adjusted .
7 , the line speed should be processed stone hardness and wear resistance to adapt, line speed table are recommended cutting different types of stone .
[ Alloy saw brand ] alloy saw blade grinding knowledge
1 , coolant grinding teeth grinding fluid that is good or bad decision . Partridge produce large amounts of tungsten grinding , diamond grinding wheel powder, not timely flushing and cleaning carbide
tipped saw blade of grinding wheel tool surface pores , causing the surface of the grinding tool can not grind finish, there is not enough cooling will burn alloys.
2 , grinding teeth grinding effect on the structure . Alloy saw blade grinding teeth model structure is good or bad
And assembly , currently on the market about two types of models: one is floating in Germany Seoul ink types. The type with vertical grinding off , all the advantages of hydraulic stepless movement , all of the feed system using V-shaped guide rail and ball screw work , grinding or big arm with slow feed forward, rewind retraction , Clips cylinder regulator heart, flexible and reliable support piece , pulling teeth accurate positioning, strong self-centering blade positioning heart , arbitrary angle adjustment , cooling flush reasonable , man-machine interface , high precision grinding off , pure grinder rational design ; Type II , which is currently horizontal such as Taiwan and Japan models, the presence of mechanical transmission gears and mechanical clearance dovetail slide accuracy, stable performance low clip , branched bandsaw blades tablet core adjustment difficult, pulling teeth institution or poor reliability , flat two sides , left and right rear corner is not a heart- mill cut , resulting in large deviation angle difficult to control, mechanical wear disaster ensure accuracy.
3 , welding factor. Welding alloys deviation and impact grinding precision , resulting in a large pressure while grinding , while pressure is small, the posterior horn of the same generation of the above factors , welding angle difference , human unavoidable factors , all of the grinding wheel and other factors generates unavoidable impact .
4 , wheel width affect the quality and size . Optional wheel running gold films , note wheel size , granularity is too diamond tool manufacturer coarse grinding wheel produced traces wheel easy to plug the optional fine granularity grinding less easy to burn knife . Grinding wheel diameter and length width thickness is based alloy and alloy tooth width or different each face the situation, not a corner after corner or front wheel specifications are the same as any different from tooth grinding , must be targeted to choose a suitable Specifications wheel .
5 , grinding feed speed. Alloy saw blade grinding entirely good or bad decision grinding feed rate , generally alloy saw blade feed rate at from 0.5 to 6 mm / s can not exceed this value should be 20 per minute teeth , the ultra in every minute 20 tooth feed rate is too large, it will have serious knife tumors or burning alloy wheel impact generated convex and concave surface precision grinding wheel wasted .
2 , grinding teeth grinding effect on the structure . Alloy saw blade grinding teeth model structure is good or bad
And assembly , currently on the market about two types of models: one is floating in Germany Seoul ink types. The type with vertical grinding off , all the advantages of hydraulic stepless movement , all of the feed system using V-shaped guide rail and ball screw work , grinding or big arm with slow feed forward, rewind retraction , Clips cylinder regulator heart, flexible and reliable support piece , pulling teeth accurate positioning, strong self-centering blade positioning heart , arbitrary angle adjustment , cooling flush reasonable , man-machine interface , high precision grinding off , pure grinder rational design ; Type II , which is currently horizontal such as Taiwan and Japan models, the presence of mechanical transmission gears and mechanical clearance dovetail slide accuracy, stable performance low clip , branched bandsaw blades tablet core adjustment difficult, pulling teeth institution or poor reliability , flat two sides , left and right rear corner is not a heart- mill cut , resulting in large deviation angle difficult to control, mechanical wear disaster ensure accuracy.
3 , welding factor. Welding alloys deviation and impact grinding precision , resulting in a large pressure while grinding , while pressure is small, the posterior horn of the same generation of the above factors , welding angle difference , human unavoidable factors , all of the grinding wheel and other factors generates unavoidable impact .
4 , wheel width affect the quality and size . Optional wheel running gold films , note wheel size , granularity is too diamond tool manufacturer coarse grinding wheel produced traces wheel easy to plug the optional fine granularity grinding less easy to burn knife . Grinding wheel diameter and length width thickness is based alloy and alloy tooth width or different each face the situation, not a corner after corner or front wheel specifications are the same as any different from tooth grinding , must be targeted to choose a suitable Specifications wheel .
5 , grinding feed speed. Alloy saw blade grinding entirely good or bad decision grinding feed rate , generally alloy saw blade feed rate at from 0.5 to 6 mm / s can not exceed this value should be 20 per minute teeth , the ultra in every minute 20 tooth feed rate is too large, it will have serious knife tumors or burning alloy wheel impact generated convex and concave surface precision grinding wheel wasted .
2013年9月27日星期五
Diamond with adamantine luster and high hardness
The composition of the diamond element C, the crystal was transparent in nature, often with octahedral, tetrahedral, and rhombic dodecahedron has occurred, the color often colorless, yellow, brown, naturally occurring in red, blue, green and so extremely rare. Adamantine luster; refractive diamond cbn wheel index of 2.417. Hardness of 10, the highest hardness in gems. Density of 3.52g/cm3. Dispersion of 0.044, it is the diamond has a high dispersion, so that the diamond produces colorful color of fire. Diamond Identification
Diamond with adamantine luster and high hardness, the diamond has been processed gives the first feeling is that its surface with strong luster, ridge angle is extremely sharp. Turn the diamond, the pavilion in its bottom surface visible orange and blue flash. Diamond has lipophilic, the diamond surface drip a drop of oil, you can see the oil on the surface spread into almost a plane. Is the thermal conductivity of diamond gem is the best, even more than the thermal conductivity of the metal are good, so using thermal conductivity meter it can be distinguished from other gemstones, but should be noted that currently there is a gem just artificially produced ---- synthetic silicon carbide, and its thermal conductivity is also high, which can make sds drill bits use of a magnifying glass, synthetic silicon carbide with diamond with ghosting distinguish. The quality of a diamond is to evaluate four aspects, namely weight (CARAT), color (COLOR), Clarity (CLARITY), cut (CUT), because they are beginning with C, therefore referred to 4C. Weight
Evaluation of the weight of the primary factor in the diamond, because the price of the diamond is almost the square of the weight of a relationship expressed by the formula: price = weight of 2 × K (factor). Diamond weight commonly "carat" and "minute", said one gram (g) = 5 克拉 (ct), 1 克拉 = 100 points. Carat diamond weighing scales can be used, you can also use high-precision electronic balance, such as the millionth electronic balance. As a unit of weight in carats, the digit after the decimal point, every 9 into a turbo diamond blade third place. Diamonds can not be weighed against the empirical estimation method can be:
Standard round diamond = Waist average diameter 2 × depth × 0.0061 (conversion factor, thick waist increased to 0.0064)
2, the color
Diamond color can be divided into two series, a series is a colorless to light yellow (brown, gray) series, another series of color series. Color series can be divided into yellow, brown, red, blue, green, pink and so on. 4C, color grading is the first series that is colorless to light yellow (brown, gray) series. Colorless diamonds used in the classification "white" means.
Diamond with adamantine luster and high hardness, the diamond has been processed gives the first feeling is that its surface with strong luster, ridge angle is extremely sharp. Turn the diamond, the pavilion in its bottom surface visible orange and blue flash. Diamond has lipophilic, the diamond surface drip a drop of oil, you can see the oil on the surface spread into almost a plane. Is the thermal conductivity of diamond gem is the best, even more than the thermal conductivity of the metal are good, so using thermal conductivity meter it can be distinguished from other gemstones, but should be noted that currently there is a gem just artificially produced ---- synthetic silicon carbide, and its thermal conductivity is also high, which can make sds drill bits use of a magnifying glass, synthetic silicon carbide with diamond with ghosting distinguish. The quality of a diamond is to evaluate four aspects, namely weight (CARAT), color (COLOR), Clarity (CLARITY), cut (CUT), because they are beginning with C, therefore referred to 4C. Weight
Evaluation of the weight of the primary factor in the diamond, because the price of the diamond is almost the square of the weight of a relationship expressed by the formula: price = weight of 2 × K (factor). Diamond weight commonly "carat" and "minute", said one gram (g) = 5 克拉 (ct), 1 克拉 = 100 points. Carat diamond weighing scales can be used, you can also use high-precision electronic balance, such as the millionth electronic balance. As a unit of weight in carats, the digit after the decimal point, every 9 into a turbo diamond blade third place. Diamonds can not be weighed against the empirical estimation method can be:
Standard round diamond = Waist average diameter 2 × depth × 0.0061 (conversion factor, thick waist increased to 0.0064)
2, the color
Diamond color can be divided into two series, a series is a colorless to light yellow (brown, gray) series, another series of color series. Color series can be divided into yellow, brown, red, blue, green, pink and so on. 4C, color grading is the first series that is colorless to light yellow (brown, gray) series. Colorless diamonds used in the classification "white" means.
diamonds expensive reason
At present, the reason why diamonds are expensive, and their characteristics are inseparable.First, the diamond hardness, high density. Diamond is the hardest natural substance known, Mohs hardness of 10. The density of 3.52 over its most natural stones, and very stable. The tile saw blade nature of gravity separation and identification are very important.In addition, the diamond will not only have a high refractive index, but also has a higher dispersion. These two factors, making the diamond cutting and grinding after the show dazzling bright light.
There is a high thermal conductivity of diamond, and its thermal conductivity of copper five times. Designed for the application of this tct saw blades principle can be used to identify the thermal conductivity meter diamond imitation. Some natural blueDiamond, boron element because, further comprising electrically conductive properties.Diamonds are very stable, temperature changes with minimal impact on its size, it does not react with the acid and alkali.Diamond has the lipophilicity of this nature commonly used in diamond sorting; surface of the water droplets in the diamond shape cutting tools and will not spread, this property can be used for the identification of diamonds and imitation.High hardness and stable chemical properties make the beauty of the diamond and the environment will not change over time, which is able to increase the value of the diamond foundation. Diamond formed under harsh conditions so scarce reserves, and is non-renewable resources. Into the global market each year are affected by De beers diamond company strictly controlled. The so-called rare
There is a high thermal conductivity of diamond, and its thermal conductivity of copper five times. Designed for the application of this tct saw blades principle can be used to identify the thermal conductivity meter diamond imitation. Some natural blueDiamond, boron element because, further comprising electrically conductive properties.Diamonds are very stable, temperature changes with minimal impact on its size, it does not react with the acid and alkali.Diamond has the lipophilicity of this nature commonly used in diamond sorting; surface of the water droplets in the diamond shape cutting tools and will not spread, this property can be used for the identification of diamonds and imitation.High hardness and stable chemical properties make the beauty of the diamond and the environment will not change over time, which is able to increase the value of the diamond foundation. Diamond formed under harsh conditions so scarce reserves, and is non-renewable resources. Into the global market each year are affected by De beers diamond company strictly controlled. The so-called rare
2013年9月26日星期四
Single crystal diamond cutting tool must be used for large particles
(mass greater than 0.1g, the best path length not less than 3mm), mainly used in surface roughness, geometry, high precision and dimensional accuracy requirements of precision and ultra precision machining applications fields.Natural diamond single crystal diamond is the most wear-resistant material. Fine texture of its own, after fine grinding, cutting edge edge edge colde saw blade radius as small as 0.008 ~ 0.005μm. But more brittle natural single crystal diamond, the crystal anisotropy, different surfaces or in the same plane of the crystal in different directions were different hardness, during grinding and use must choose the right direction. The use of harsh conditions, coupled with natural single crystal diamond resources are limited, the price is very expensive, so they use a production PCD, PCD / CC and CVD diamond tools. Natural single crystal diamond diamond saw blade is mainly used for some of the ultra-precision machining non-ferrous metals or gold jewelry production.Synthetic single crystal diamond the size, shape and performance are in good agreement, present due to high pressure technology matures, a certain size can be prepared by synthetic single crystal diamond, especially in the processing of high wear-resistant laminated wood, it performance than PCD diamond cutting edge will metal grinding wheel not cause premature passivated.Synthetic polycrystalline diamond (PCD) and synthetic polycrystalline diamond and carbide composite blade (PCD / CC)PCD is at high temperature (about 1800 ℃), pressure (5 ~ 6MPa), the use of cobalt and other metal binding agent to a number of polycrystalline diamond crystal powder polycrystalline material, although slightly lower than the hardness of a single crystal diamond, but it is randomly oriented diamond grains polymerization, is isotropic, as can be arbitrarily oriented cutting tool sharpening, no natural diamond that must be selected as the best cleavage plane as a rake. Diamond saw blade during cutting, the cutting edge is very sensitive for accidental damage, wear resistance is also strong, long stay sharp cutting edge, can be used when machining high speeds and larger cutting depth ( eat deep), life in general is higher than WC-based cemented carbide cutting tools 10 to 500 times, and because of PCD in a conductive metal binding agent, making PCD easy cut to shape, and abundant sources of raw materials, and Diamond tool its price is only dozens of natural diamond a fraction of one to ten, one has become a traditional WC-based cemented carbide cutting tools, high-performance alternatives.PCD inserts to improve the toughness and weldability in the cemented carbide substrate, sintered or pressed on the surface of 0.5 ~ 1mm thick layer of the composition of PCD diamond composite blade (PCD / CC). PCD / CC welding or machine folder available way of making knives. Due to its good weldability, regrinding easy, low cost, and therefore widely used. Diamond saw blade should be noted that, PCD and PCD / CC tool edge sharpness and better surface quality are monocrystalline diamond, while its workability is poor, the grinding ratio is small, it is difficult according to the geometry of any head shape, still can not be easily manufactured with chipbreakers indexable end mills and other geometric shapes and complex products.
Alloy saw blade when grinding many factors
1, the matrix deformation, inconsistent thickness, bore tolerances big. Congenital defects of the base there is a problem, no matter the kind of graphics device, there is grinding errors. Matrix deformation on the two side angle bias; matrix inconsistent thickness right rear corner and edge front corner of bias, such as the existence of cumulative tolerance is too large, the quality and accuracy of the blade severely affected.
2, grinding teeth grinding effect on the structure. Alloy saw blade grinding machine structure and assembly is good or bad, about two types of models currently on the market: one is floating in Germany Seoul ink types. The type with vertical grinding off, all the advantages of hydraulic stepless movement, all of the feed system using V-shaped guide rail and ball screw work, grinding or big arm with slow feed forward, rewind retraction, Clips cylinder regulator center support piece flexible and reliable, accurate positioning pulling teeth, blade positioning center firmly self-centering, arbitrary angle adjustment, cooling flush reasonable, man-machine interface, high precision grinding off, pure grinder rational design; diamond saw two categories namely At present horizontal, such as Taiwan and Japan models, mechanical transmission gears and mechanical clearance exists dovetail slide accuracy, stable performance low clip, branched piece center adjustment difficult, pulling teeth institution or poor reliability, flat two sides, left and right rear corner is not a center grinding, producing large deviation angle difficult to control, mechanical wear disaster ensure accuracy.
3, welding factor. Welding Alloys for moderate deviations and impact grinding precision, resulting in a large pressure while grinding, while pressure is small, the posterior horn of the same generation of the above factors, welding angle difference, human factors will inevitably have on the grinding wheel, etc. factors produce unavoidable impact.
4, wheel width affect the quality and size. Optional wheel running gold films, note wheel size, granularity is too coarse grinding wheel produced traces wheel easy to plug the optional fine granularity grinding less easy to burn knife. Diamond Saw wheel diameter and wheel width stone drill bits length width thickness is based alloy or a different tooth surfaces and alloys of each case may be, not a corner after corner or front wheel specifications are the same as any different from tooth grinding, must be targeted to choose a suitable size wheel.
5, grinding feed speed. Alloy saw blade grinding entirely good or bad decision grinding feed rate, generally alloy saw blade feed rate at from 0.5 to 6 mm / s can not exceed this value should be 20 per minute teeth, the ultra in every minute 20 tooth feed rate is too large, it will have serious knife tumors or burning alloy wheel impact generated convex and concave surface precision grinding wheel wasted.
6, grinding feed rate, the choice of wheel size on the amount of feed has an extremely important significance. General grinding wheel recommendation to use 180 # 240 # 240 # to use at most an opt 280 # 280 # to 320 #, or to adjust the feed rate.
7, grinding center. All grinding the blade and the substrate as the center, rather than with the blade as the center, get it out flat grinding center, rear angle, rake angle with a processing center can not be sharpened a saw blade, saw blade grinding three processes the center can not be ignored. Grinding diamond saw blade side angle is still careful observation alloy thickness, the thickness change with different grinding center, regardless of how the alloy thickness, the grinding surface grinding wheel center line and the welding position to be maintained in a straight line, or have carbide tipped saw blade a poor impact angle cutting.
8, pulling teeth institutions can not be ignored. Regardless of how the structure of any grinding, pulling teeth designed to coordinate accuracy sharpening design quality, machine adjustment pulling teeth acupressure reasonable position in the tooth surface, and not with the move is extremely critical, back teeth when pulling teeth claw should flexible and reliable.
9, Clips institutions: institutions firmly clip stable and reliable quality is the main part of the Brothers, the Brothers when any clip institutions can not have the slightest loosening, or grinding teeth deviation seriously out of control.
10, grinding itinerary. Regardless of any part of the blade grinding, grinding grinding stroke is very important, generally require grinding wheel or exit out of the workpiece 1 mm 1 mm is appropriate, or cutting discs tooth blade produces two faces.
11, the program options: Sharpening generally provided with a rough and fine grinding three different programs options, depending on the degree of demand for product selection, and finally recommended when grinding rake angle grinding process.
12, coolant grinding teeth grinding fluid that is good or bad decision. Diamond saw blade grinding produce large amounts of tungsten partridge, diamond wheel powder, not timely flushing and cleaning of grinding wheel tool surface pores, causing the surface of the grinding tool can not grind finish, there is not enough cooling will burn alloys.
2, grinding teeth grinding effect on the structure. Alloy saw blade grinding machine structure and assembly is good or bad, about two types of models currently on the market: one is floating in Germany Seoul ink types. The type with vertical grinding off, all the advantages of hydraulic stepless movement, all of the feed system using V-shaped guide rail and ball screw work, grinding or big arm with slow feed forward, rewind retraction, Clips cylinder regulator center support piece flexible and reliable, accurate positioning pulling teeth, blade positioning center firmly self-centering, arbitrary angle adjustment, cooling flush reasonable, man-machine interface, high precision grinding off, pure grinder rational design; diamond saw two categories namely At present horizontal, such as Taiwan and Japan models, mechanical transmission gears and mechanical clearance exists dovetail slide accuracy, stable performance low clip, branched piece center adjustment difficult, pulling teeth institution or poor reliability, flat two sides, left and right rear corner is not a center grinding, producing large deviation angle difficult to control, mechanical wear disaster ensure accuracy.
3, welding factor. Welding Alloys for moderate deviations and impact grinding precision, resulting in a large pressure while grinding, while pressure is small, the posterior horn of the same generation of the above factors, welding angle difference, human factors will inevitably have on the grinding wheel, etc. factors produce unavoidable impact.
4, wheel width affect the quality and size. Optional wheel running gold films, note wheel size, granularity is too coarse grinding wheel produced traces wheel easy to plug the optional fine granularity grinding less easy to burn knife. Diamond Saw wheel diameter and wheel width stone drill bits length width thickness is based alloy or a different tooth surfaces and alloys of each case may be, not a corner after corner or front wheel specifications are the same as any different from tooth grinding, must be targeted to choose a suitable size wheel.
5, grinding feed speed. Alloy saw blade grinding entirely good or bad decision grinding feed rate, generally alloy saw blade feed rate at from 0.5 to 6 mm / s can not exceed this value should be 20 per minute teeth, the ultra in every minute 20 tooth feed rate is too large, it will have serious knife tumors or burning alloy wheel impact generated convex and concave surface precision grinding wheel wasted.
6, grinding feed rate, the choice of wheel size on the amount of feed has an extremely important significance. General grinding wheel recommendation to use 180 # 240 # 240 # to use at most an opt 280 # 280 # to 320 #, or to adjust the feed rate.
7, grinding center. All grinding the blade and the substrate as the center, rather than with the blade as the center, get it out flat grinding center, rear angle, rake angle with a processing center can not be sharpened a saw blade, saw blade grinding three processes the center can not be ignored. Grinding diamond saw blade side angle is still careful observation alloy thickness, the thickness change with different grinding center, regardless of how the alloy thickness, the grinding surface grinding wheel center line and the welding position to be maintained in a straight line, or have carbide tipped saw blade a poor impact angle cutting.
8, pulling teeth institutions can not be ignored. Regardless of how the structure of any grinding, pulling teeth designed to coordinate accuracy sharpening design quality, machine adjustment pulling teeth acupressure reasonable position in the tooth surface, and not with the move is extremely critical, back teeth when pulling teeth claw should flexible and reliable.
9, Clips institutions: institutions firmly clip stable and reliable quality is the main part of the Brothers, the Brothers when any clip institutions can not have the slightest loosening, or grinding teeth deviation seriously out of control.
10, grinding itinerary. Regardless of any part of the blade grinding, grinding grinding stroke is very important, generally require grinding wheel or exit out of the workpiece 1 mm 1 mm is appropriate, or cutting discs tooth blade produces two faces.
11, the program options: Sharpening generally provided with a rough and fine grinding three different programs options, depending on the degree of demand for product selection, and finally recommended when grinding rake angle grinding process.
12, coolant grinding teeth grinding fluid that is good or bad decision. Diamond saw blade grinding produce large amounts of tungsten partridge, diamond wheel powder, not timely flushing and cleaning of grinding wheel tool surface pores, causing the surface of the grinding tool can not grind finish, there is not enough cooling will burn alloys.
2013年9月25日星期三
diamond cutting depth is related to wear
saw cutting force conditions and the nature of the important parameters of stone. Generally speaking, when the line speed diamond saw blade is high, should be selected for cutting of small depth, from the stone polishing pads current technology, the cutting depth of the diamond can choose between 1mm ~ 10mm. Usually with a large diameter saw blade cutting granite blocks, the cutting depth can be controlled within 1mm 2mm between the feed rate should be reduced at the same time. When the line speed diamond saw blade is large, a large cutting depth should be selected. But in performance and tool strength saw the extent permitted, should try to take a greater depth of cut for cutting to improve cutting efficiency. When the machined surface flap discs when requested, should be used small depth of cut.
Feed speed: Cutting feedrate incurs stone feed rate. Its size sawing rate impact, the force and the cutting blade heat dissipation area. Its value should be based on the nature of the selected cutting stone. Generally speaking, sawing softer stone, such as marble, may be Diamond tool appropriate to increase the feed speed, if the feed rate is too low, more conducive to high cutting rates. Sawing fine structure, relatively homogeneous granite, may be appropriate to increase the feed speed, feed rate is too low if the diamond blade easily be polished. But sawing UNEVEN coarse granite structure, should reduce feed speed, otherwise it will cause the blade vibration and reduce fragmentation leading diamond cutting rates. Granite cutting feed rate is generally 9m ~ 12m/min within the selected range.
Feed speed: Cutting feedrate incurs stone feed rate. Its size sawing rate impact, the force and the cutting blade heat dissipation area. Its value should be based on the nature of the selected cutting stone. Generally speaking, sawing softer stone, such as marble, may be Diamond tool appropriate to increase the feed speed, if the feed rate is too low, more conducive to high cutting rates. Sawing fine structure, relatively homogeneous granite, may be appropriate to increase the feed speed, feed rate is too low if the diamond blade easily be polished. But sawing UNEVEN coarse granite structure, should reduce feed speed, otherwise it will cause the blade vibration and reduce fragmentation leading diamond cutting rates. Granite cutting feed rate is generally 9m ~ 12m/min within the selected range.
alloy circular saw blades to improve the life of a number of factors
the matrix requires the selection of materials is good enough base heat-resistant material, high toughness, strength, stress, deformation and side jump smaller base, the base of each one grinding wheels tooth angle seat depth matrix consistent hole tolerances and high precision, material density, thickness, uniform hardness. 2, try to use low-temperature welding process tooth silver electrode and flux selection and good mobility, to prevent the room temperature quenching dips, welding gear temperature in principle allowed to exceed 750 °, to ensure that every weld tooth tooth tooth welding temperature uniformity and repeat, Try to use bilateral high-frequency generator heating the alloy and the substrate temperature remained the same, to sds hammer drill bits ensure welded into the oven to eliminate welding stress and the alloy crystal refinement, and keep the weld strength. 3, precision grinding tool life and process using the key in the blade, the blade is not grinding in place various surface resistance, obviously chosen too coarse grinding wheel grinding wheel marks, traces of grinding wheel misalignment, angular asymmetry, any faces two flank , wheel impact blade retraction pressure belt, jump to maintain the minimum diameter runout side rake angle requirements of small, back rake should not use too large, the correct selection of grinding direction of carbide grinding wheels rotation, and the radial cutting force from low to high, grinding two side angle grinding process first, and then after grinding angle and back rake, rake angle and blade rake angle is the last part of tool manufacture, process violation in front of the tool will bring to the quality of results. 4, to strengthen pre-shipment inspection tool each process must develop a reasonable process, according to the strict and meticulous inspection process, affecting the quality of the reason is very complex tool, bad checks before the process after the process no end of trouble, as long as careful analysis of all factors that can be solved .
2013年9月24日星期二
As abrasive grinding process is constantly broken or lost
if not timely supplement, will result in leaving because of insufficient density of diamond abrasive disk directly in contact with the iron will not only affect the quality of tool grinding, but Plate Compactor also because the diamond scratch squeeze role of the disk damage or blockage the pores, thus reducing the life of the grinding disc. Thus, during the grinding process requires frequent to add a new disk grinding paste.In addition, prior to powder coating pretreatment disk grinding disc is also vital, generally required Whetstone SiC abrasive powder or coarse grind performed on the disk to remove the turning grooves to improve the disk flatness. By using a variety of stone and SiC powder grinding disk comparative tests and found that the ring saw blades disk with TL280ZY1 Whetstone millstone W1 1 hour and then painted with fine diamond powder, get the best grinding disk, then the shortest time to reach a stable disk, grinding After smallest serrated blade. The use of free SiC abrasive powder is easily clogged pores on the disk, so that a large number of diamond powder hard and firmly embedded in the ground plate.Sharpening angle on the quality of groundPolishing sharpening angle q is the linear velocity of the angle between the direction of the blade. When q> 0 ° when the rubbing direction of the blade from the blade point, called the smooth grinding; when q <0 ° when the rubbing direction from the blade point to the cutter body, known as reverse mill. Figure 2 shows the degree of the sharpening serrated blade angle. High tensile strength of the diamond, grinding along, the blade tensile stress, so after grinding teeth smaller degree; inverse mill, the blade to withstand compressive stress, so after grinding teeth greater degree. As can be concrete cutting blade seen from Figure 2, when q is greater than 0 °, and is close to the minimum serrated blade degree obtained, when the stress edge substantially parallel to the direction of the blade, and the blade in this direction has the highest tensile stress intensity . Parallel to the edge grinding is another advantage of the flank wear scar is parallel with the blade in the cutting process does not copy the machined surface maps to help improve the quality of cutting.
Diamond grinding disc for grinding of cast iron
Single-crystal diamond tool manufacturing processes generally include material selection, orientation, sawing, cogging, installed cards, rough grinding, fine grinding and inspection. Will be selected by the directional diamond original stone after sawing along the carbide drill bits biggest open plane, get two tool blanks, so that both improve the utilization of diamond material, but also reduce the total amount of polishing. Blooming through the tool can shape up chucking (mosaic or brazing) requirements. Cogging and coarse, fine grinding polishing methods are used.Diamond grinding disc for grinding of cast iron. Grinding disc diameter of about 300mm, organized by the material pore shape, size and proportions of the diamond abrasive are optimized special high phosphorus cast iron. Grinding disc surface inlaid metal grinding wheel with diamond abrasive powder, the particle size can be from less than 1μm until 40μm. Rough diamond powder particles having a high polishing rate, but poor quality grinding, generally used so coarse meal, and is used when grinding the powder size of less than 1μm. Before grinding, first diamond powder with olive oil or other similar substances mixed into a grinding paste, and then coated on the surface of the grinding plate, place some time for the grinding disc grinding paste to fully penetrate the pores of the cast, and ring saw blades then a large diamond in pre-grinding disc surface grinding back and forth in order to further strengthen the diamond powder in the cast iron pores mosaic effect. Grinding, polishing the diamond will generally be embedded in a tin bucket, revealing only a surface to be polished. Abrasive grinding disc speed is about 2500r/min, grinding pressure of about 1kg/mm2.
2013年9月23日星期一
Diamond saw blade diamond segment is the work of the subject
1 diamond size selection
When coarse diamond size and granularity of a single, sharp saw blade, cutting efficiency is high, but the flexural strength of agglomerated diamond drop; when fine or coarse grained diamond size when mixed with saw blade durability, but efficiency is low. Considering these factors, choose diamond size 50/60 mesh is more appropriate.
(2) the selection of diamond concentration tamping rammer distribution
Within a certain range, when the diamond concentration changes from low to high, the blade sharpness and cutting efficiency decreased, while life is gradually extended; but the concentration is too high, the blade becomes blunt. The use of low concentration, coarse, efficiency will be increased. The use of various parts of the cutting head when the different roles of different concentrations (i.e. three or more layer structure in the intermediate layer can be used in low concentrations), the saw blade during the work head to form an intermediate groove, with helps prevent blade deflection, thereby improving the quality of stone processing.
3 diamond strength selection
Is to ensure the strength of the diamond cutting important indicator of performance. High intensity causes the crystal is broken, the polishing abrasive grains are in use, the sharpness decreased, resulting in performance degradation tool; diamond enough strength when subjected to shock easily broken, difficult to bear heavy cutting. It should choose a strength of 130 ~ 140N.
4 choice of binder phase
Depends not only on the performance of the blade diamond, but on the diamond and the binder with the appropriate head of this composite material composed of the overall performance. For marble and other soft stone, head of the cutting blades mechanical properties required is relatively low, the choice of copper-based binder. The sintering temperature is low but the copper-based binder, strength, low hardness, high toughness, low bonding strength with the diamond. When adding tungsten carbide (WC), the WC or W2C to as a skeleton metal, with the amount of cobalt in order to improve the strength, hardness and binding properties, and add a small amount of low melting point and low hardness Cu, Sn, Zn and other metal for bonding phase. Main plus ingredients turbo blades should be finer than 200 mesh size, add ingredients finer than 300 mesh size should be.
5 Select the sintering process
As the temperature increases, the carcass densification improved flexural strength also will increase, and with the holding time, the blank matrix and diamond caked flexural strength increased firstly and then decreased, you can choose 120s at 800 ℃ sintering processes to meet performance requirements.
When coarse diamond size and granularity of a single, sharp saw blade, cutting efficiency is high, but the flexural strength of agglomerated diamond drop; when fine or coarse grained diamond size when mixed with saw blade durability, but efficiency is low. Considering these factors, choose diamond size 50/60 mesh is more appropriate.
(2) the selection of diamond concentration tamping rammer distribution
Within a certain range, when the diamond concentration changes from low to high, the blade sharpness and cutting efficiency decreased, while life is gradually extended; but the concentration is too high, the blade becomes blunt. The use of low concentration, coarse, efficiency will be increased. The use of various parts of the cutting head when the different roles of different concentrations (i.e. three or more layer structure in the intermediate layer can be used in low concentrations), the saw blade during the work head to form an intermediate groove, with helps prevent blade deflection, thereby improving the quality of stone processing.
3 diamond strength selection
Is to ensure the strength of the diamond cutting important indicator of performance. High intensity causes the crystal is broken, the polishing abrasive grains are in use, the sharpness decreased, resulting in performance degradation tool; diamond enough strength when subjected to shock easily broken, difficult to bear heavy cutting. It should choose a strength of 130 ~ 140N.
4 choice of binder phase
Depends not only on the performance of the blade diamond, but on the diamond and the binder with the appropriate head of this composite material composed of the overall performance. For marble and other soft stone, head of the cutting blades mechanical properties required is relatively low, the choice of copper-based binder. The sintering temperature is low but the copper-based binder, strength, low hardness, high toughness, low bonding strength with the diamond. When adding tungsten carbide (WC), the WC or W2C to as a skeleton metal, with the amount of cobalt in order to improve the strength, hardness and binding properties, and add a small amount of low melting point and low hardness Cu, Sn, Zn and other metal for bonding phase. Main plus ingredients turbo blades should be finer than 200 mesh size, add ingredients finer than 300 mesh size should be.
5 Select the sintering process
As the temperature increases, the carcass densification improved flexural strength also will increase, and with the holding time, the blank matrix and diamond caked flexural strength increased firstly and then decreased, you can choose 120s at 800 ℃ sintering processes to meet performance requirements.
Users in the selection and use of diamond coated tool
(1) CVD diamond coated with amorphous diamond coating difference
Amorphous diamond (also called diamond-like carbon - Annotation) coatings are deposited using a PVD process carbon. It has a key part of the diamond SP3, SP2 also has some carbon bond; their film hardness is high, but lower than the hardness of diamond film; thickness than we stone drill bits usually deposited diamond film to be thinner. Machining graphite, amorphous diamond coated tool life is uncoated carbide tools 2-3 times. In contrast, CVD diamond is deposited using CVD process pure diamond coating, machining graphite carbide cutting tool life is 12-20 times, thereby reducing the number of tool changes to improve the reliability and accuracy of processing consistency.
(2) can not be hardened steel with diamond tooling
Diamond from carbon atoms. Certain materials when heated, sucked from the carbon atoms in diamond and carbide is formed in the workpiece. Iron is one such material. Cutting tools with diamond iron group material, the friction generated heat causes diffusion of carbon atoms in carbide grinding wheels the diamond into the iron, the resulting diamond coating due to chemical wear and premature failure.
(3) restriction diamond tool
Regrinding and (or) heavy coating of diamond coated tools is difficult to guarantee the quality of the coating formed on the surface as the tool for the pure diamond, so the tool with a diamond wheel for re-grinding takes a very long time. In addition, the growth of the diamond tool used. Preparation of the tool will change the chemical properties of the surface, since the coating of this chemical properties requires very precise control, so the effect of the tool recoating difficult to be guaranteed.
(4) diamond coated tool life varies
Like any other tool, diamond coated tool life varies, depending on the material to be cut, the choice of feed rate and cutting speed, and the turbo blades geometry of the workpiece and so on. Generally, diamond-coated graphite machining tool life is uncoated carbide tools 10-20 times, in some cases, may even be longer. This way, you can use a tool to complete almost any processing tasks without tool change due to tool wear and to avoid disruption and recalibration process, making it possible to achieve unattended machining. The processing of the composite material, is entirely possible to obtain a longer tool life.
According to reports, in the processing of high-density glass fiber, carbon fiber and Gl0-FR4 other difficult machining composite materials, diamond-coated tool life up to uncoated carbide tool 70 times.
Amorphous diamond (also called diamond-like carbon - Annotation) coatings are deposited using a PVD process carbon. It has a key part of the diamond SP3, SP2 also has some carbon bond; their film hardness is high, but lower than the hardness of diamond film; thickness than we stone drill bits usually deposited diamond film to be thinner. Machining graphite, amorphous diamond coated tool life is uncoated carbide tools 2-3 times. In contrast, CVD diamond is deposited using CVD process pure diamond coating, machining graphite carbide cutting tool life is 12-20 times, thereby reducing the number of tool changes to improve the reliability and accuracy of processing consistency.
(2) can not be hardened steel with diamond tooling
Diamond from carbon atoms. Certain materials when heated, sucked from the carbon atoms in diamond and carbide is formed in the workpiece. Iron is one such material. Cutting tools with diamond iron group material, the friction generated heat causes diffusion of carbon atoms in carbide grinding wheels the diamond into the iron, the resulting diamond coating due to chemical wear and premature failure.
(3) restriction diamond tool
Regrinding and (or) heavy coating of diamond coated tools is difficult to guarantee the quality of the coating formed on the surface as the tool for the pure diamond, so the tool with a diamond wheel for re-grinding takes a very long time. In addition, the growth of the diamond tool used. Preparation of the tool will change the chemical properties of the surface, since the coating of this chemical properties requires very precise control, so the effect of the tool recoating difficult to be guaranteed.
(4) diamond coated tool life varies
Like any other tool, diamond coated tool life varies, depending on the material to be cut, the choice of feed rate and cutting speed, and the turbo blades geometry of the workpiece and so on. Generally, diamond-coated graphite machining tool life is uncoated carbide tools 10-20 times, in some cases, may even be longer. This way, you can use a tool to complete almost any processing tasks without tool change due to tool wear and to avoid disruption and recalibration process, making it possible to achieve unattended machining. The processing of the composite material, is entirely possible to obtain a longer tool life.
According to reports, in the processing of high-density glass fiber, carbon fiber and Gl0-FR4 other difficult machining composite materials, diamond-coated tool life up to uncoated carbide tool 70 times.
2013年9月22日星期日
single crystal diamond tool machining mechanism
Area remaining after cutting height h = f / (ctgkr + ctgkr ') is the theory of the machined surface roughness, it varies the feed rate f, the tool main and sub declination angle kr kr' the decrease decreases. As the main angle kr Fy force reduction will increase rapidly and wet granite
pads cause tool vibration, reducing the feed rate f will affect the cutting efficiency, it is generally by reducing the deputy angle kr 'to reduce the surface roughness.
Conventional cutting tool surface is rough, poor edge formation, if the choice of the sub angle is too small, while the secondary cutting edge is not flat will be mapped to complex processing of the surface; also exacerbate the other flank and the sub- processing of the friction, the machined surface. "galling." Therefore, in conventional cutting, deputy angle of approximately 2 °, the minimum value of surface roughness, further reduce the deputy angle will cause the deterioration of the quality of the machined surface.
Monocrystalline diamond tool may be less than the surface roughness Ra0.01μm, edge quality can reach at least under the granite polishing pad microscope at 100 times the defect, combined friction coefficient is extremely small, so the sub-angle limit can be reduced to 0 ~ 2 ' , thereby allowing theoretical surface roughness close to or equal to zero, the actual value of the surface roughness can be achieved ultra-smooth surface or mirror requirements.
Thus, the tool itself, the single crystal diamond tool mirror processing mechanism is through ultra-smooth surface and the tool defect secondary cutting edge (wiper) the role of the theoretical surface roughness values close to zero Mirror processing effect is obtained.
2 single-crystal diamond tool design
Single-crystal diamond tool designed to consider when main factors: ① precision parts to be processed; ② actual processing conditions; ③ diamond material properties.
Design single crystal diamond tool, you diamond core drills should follow the following principles: ① Because single-crystal diamond high hardness, processing difficulties, so the shape of the tool should be as simple as possible; ② According to single-crystal diamond brittle, poor impact resistance characteristics, should be combined with the actual processing conditions, through the tool geometry are optimized to improve the impact resistance head; ③ precision machined parts according to the requirements of the design wiper length, taking into account the ability of the tool to cut thin.
Conventional cutting tool surface is rough, poor edge formation, if the choice of the sub angle is too small, while the secondary cutting edge is not flat will be mapped to complex processing of the surface; also exacerbate the other flank and the sub- processing of the friction, the machined surface. "galling." Therefore, in conventional cutting, deputy angle of approximately 2 °, the minimum value of surface roughness, further reduce the deputy angle will cause the deterioration of the quality of the machined surface.
Monocrystalline diamond tool may be less than the surface roughness Ra0.01μm, edge quality can reach at least under the granite polishing pad microscope at 100 times the defect, combined friction coefficient is extremely small, so the sub-angle limit can be reduced to 0 ~ 2 ' , thereby allowing theoretical surface roughness close to or equal to zero, the actual value of the surface roughness can be achieved ultra-smooth surface or mirror requirements.
Thus, the tool itself, the single crystal diamond tool mirror processing mechanism is through ultra-smooth surface and the tool defect secondary cutting edge (wiper) the role of the theoretical surface roughness values close to zero Mirror processing effect is obtained.
2 single-crystal diamond tool design
Single-crystal diamond tool designed to consider when main factors: ① precision parts to be processed; ② actual processing conditions; ③ diamond material properties.
Design single crystal diamond tool, you diamond core drills should follow the following principles: ① Because single-crystal diamond high hardness, processing difficulties, so the shape of the tool should be as simple as possible; ② According to single-crystal diamond brittle, poor impact resistance characteristics, should be combined with the actual processing conditions, through the tool geometry are optimized to improve the impact resistance head; ③ precision machined parts according to the requirements of the design wiper length, taking into account the ability of the tool to cut thin.
single crystal diamond tool application
a single diamond crystal, the crystal structure of the highest density of metal atom such as axial face-centered cubic crystal. Diamond crystal connected between the carbon atoms bond to sp3 hybridized covalent bond, with a strong binding force, stability and direction. The wet
polishing pad unique crystal structure of diamond in nature it has the highest hardness, stiffness, refractive index and thermal conductivity, and high wear resistance, corrosion resistance and chemical stability.
Excellent characteristics of single crystal diamond meet the precision and ultra-precision cutting tool material for most of the requirements and is ideal for precision cutting tool materials. Diamond without internal grain boundaries uniform crystal structure so that the tool cutting edge can theoretically reach the atomic level flatness and sharpness, cut thin cutting ability, high precision, cutting force is small; their diamond tool manufacturer high hardness and good wear resistance resistance, corrosion resistance and chemical stability can ensure that the tool has a long life, so that it can continue for a long time of cutting, the tool wear can be reduced because of the precision of the parts; its high thermal conductivity can be reduced and the cutting temperature parts thermal deformation.
Single crystal diamond tool in the machining field has an important position, is widely used as a mirror, missiles and rockets navigation gyro, computer hard disk substrate accelerator electron gun, such as ultra hole saw blades precision mirror of parts. Can also be used in the manufacture of single crystal diamond eye, brain surgeon's scalpel, thin slicing knives and other bio-medical tools. In addition, single-crystal diamond tool in civilian products processing applications are becoming increasingly widespread, from watch parts, aluminum pistons, jewelry and other processing to pens, high-gloss mirror decorative signs and non-ferrous metal parts processing, its application has entered the machining a variety of areas.
This article focuses on the design principles of the single crystal diamond tool and the use of technology.
Excellent characteristics of single crystal diamond meet the precision and ultra-precision cutting tool material for most of the requirements and is ideal for precision cutting tool materials. Diamond without internal grain boundaries uniform crystal structure so that the tool cutting edge can theoretically reach the atomic level flatness and sharpness, cut thin cutting ability, high precision, cutting force is small; their diamond tool manufacturer high hardness and good wear resistance resistance, corrosion resistance and chemical stability can ensure that the tool has a long life, so that it can continue for a long time of cutting, the tool wear can be reduced because of the precision of the parts; its high thermal conductivity can be reduced and the cutting temperature parts thermal deformation.
Single crystal diamond tool in the machining field has an important position, is widely used as a mirror, missiles and rockets navigation gyro, computer hard disk substrate accelerator electron gun, such as ultra hole saw blades precision mirror of parts. Can also be used in the manufacture of single crystal diamond eye, brain surgeon's scalpel, thin slicing knives and other bio-medical tools. In addition, single-crystal diamond tool in civilian products processing applications are becoming increasingly widespread, from watch parts, aluminum pistons, jewelry and other processing to pens, high-gloss mirror decorative signs and non-ferrous metal parts processing, its application has entered the machining a variety of areas.
This article focuses on the design principles of the single crystal diamond tool and the use of technology.
2013年9月21日星期六
Stone polishing abrasives what role
Stone with its elegant posture , loved by the people , with economic development , more and more extensive use of stone , especially a variety of public places, but the use of stone , as time changes, there sanding paper will be pollution and other issues of aging , which can be By way of preliminary cleaning solution , but sometimes must be refurbished by grinding way to achieve the following through abrasive materials , abrasive materials introduced , so that we have a preliminary understanding of this .
Abrasive polishing materials are used , are generally classified ordinary abrasives, superhard abrasive types ; ordinary abrasive including corundum ( corundum, corundum , etc. ) , and concrete ring saw its main chemical composition Al2O3 ( aluminum oxide ) , silicon carbide ( black silicon carbide, green silicon carbide ) , and its main chemical components of SiC (silicon carbide ) .
Diamond grinding tools are metal, resin , ceramic, etc. , which are classified according to type of binding agent , metal abrasive materials include iron, copper , cobalt-based these categories , will determine the different types of materials, processing costs, which is characterized by long life, but the cost will be higher . resinous abrasive materials, due to the production costs are relatively low, the application should be cutting discs relatively more, it is now also used for rough grinding to polishing, polishing fine-grained aspects of its greatest advantage ; ceramic diamond in recent years, the fastest growing abrasive tool , its processing performance , the length of metal processing , to avoid resin processing short, is technically a very good advantage, but because of cost reasons , have not seen the stone used in the refurbishment .
Abrasive polishing materials are used , are generally classified ordinary abrasives, superhard abrasive types ; ordinary abrasive including corundum ( corundum, corundum , etc. ) , and concrete ring saw its main chemical composition Al2O3 ( aluminum oxide ) , silicon carbide ( black silicon carbide, green silicon carbide ) , and its main chemical components of SiC (silicon carbide ) .
Diamond grinding tools are metal, resin , ceramic, etc. , which are classified according to type of binding agent , metal abrasive materials include iron, copper , cobalt-based these categories , will determine the different types of materials, processing costs, which is characterized by long life, but the cost will be higher . resinous abrasive materials, due to the production costs are relatively low, the application should be cutting discs relatively more, it is now also used for rough grinding to polishing, polishing fine-grained aspects of its greatest advantage ; ceramic diamond in recent years, the fastest growing abrasive tool , its processing performance , the length of metal processing , to avoid resin processing short, is technically a very good advantage, but because of cost reasons , have not seen the stone used in the refurbishment .
How emery cloth sandpaper belt reel made
Industrial most sandpaper belt sandpaper belt abrasive cloth roll , abrasive belt is a high hardness and mechanical strength of a particulate material, which is directly used for the manufacture of abrasive or grinding and polishing as a sandpaper sand with emery cloth roll cutting discs must have the basic features , in general, should meet the following five requirements :
Sandpaper belt abrasive cloth roll hardness must be higher than the hardness of the object to be processed , otherwise , can not be achieved grinding requirements. Modest crush resistance and self -sharpening sandpaper belt abrasive cloth roll have appropriate crush resistance and self-sharpening sex , during grinding , abrasive order love with a compressive, flexural , impact and other stresses , such as its crush resistance is too low, grinding abrasive quickly broken , it is difficult for effective grinding : on the contrary , after blunt abrasive nor broken, not a new blade , so that the grinding unable to proceed, therefore , requires grit blunt after grinding under stress , self- broken, exposing new sharp blade , the grinding process continues . 3 . Sandpaper belt abrasive cloth roll should have good thermal stability
Grinding work, often produce large amounts of heat , high temperatures can be achieved locally as a sandpaper belt abrasive cloth roll at high temperature should be able to maintain a certain hardness and strength , for example, the highest temperature hardness of diamond , but more than 800 ℃ will be carbonized into graphite, the sharp decline in hardness and tile cutting blades strength , which to a certain extent, limit the application of diamond .
4 . Sandpaper belt abrasive cloth roll should have a certain chemical stability c9T Huizhou HTC grinding plant material
Sandpaper belt abrasive cloth roll with the object to be processed is not easy to produce a chemical reaction . Term practice has shown that the grinding is not a simple mechanical process in which the presence of certain chemical reactions , such as silicon carbide sandpaper belt abrasive cloth roll steel processing occurs when following reaction : SiC ( solid ) +4 Fe ( liquid ) → FeSi ( solid ) + Fe3C ( solid) as sandpaper belt abrasive cloth roll and being the processing target a chemical reaction, the abrasive sandpaper belt inherent mechanical properties of the volume change, which affecting the grinding effect .
5 . Ease of processing into particles of different sizes is the use of the abrasive grinding surface composed of many particles to carry out the cutting edge , so the process should sandpaper belt abrasive cloth roll to the desired particle size . Some substances , such as tamping rammer cemented carbide Although high hardness, but because of its toughness is large, compared with sandpaper belt abrasive cloth roll is difficult processed into granules, therefore , not suitable for manufacturing emery cloth sandpaper belt reel .
Sandpaper belt abrasive cloth roll hardness must be higher than the hardness of the object to be processed , otherwise , can not be achieved grinding requirements. Modest crush resistance and self -sharpening sandpaper belt abrasive cloth roll have appropriate crush resistance and self-sharpening sex , during grinding , abrasive order love with a compressive, flexural , impact and other stresses , such as its crush resistance is too low, grinding abrasive quickly broken , it is difficult for effective grinding : on the contrary , after blunt abrasive nor broken, not a new blade , so that the grinding unable to proceed, therefore , requires grit blunt after grinding under stress , self- broken, exposing new sharp blade , the grinding process continues . 3 . Sandpaper belt abrasive cloth roll should have good thermal stability
Grinding work, often produce large amounts of heat , high temperatures can be achieved locally as a sandpaper belt abrasive cloth roll at high temperature should be able to maintain a certain hardness and strength , for example, the highest temperature hardness of diamond , but more than 800 ℃ will be carbonized into graphite, the sharp decline in hardness and tile cutting blades strength , which to a certain extent, limit the application of diamond .
4 . Sandpaper belt abrasive cloth roll should have a certain chemical stability c9T Huizhou HTC grinding plant material
Sandpaper belt abrasive cloth roll with the object to be processed is not easy to produce a chemical reaction . Term practice has shown that the grinding is not a simple mechanical process in which the presence of certain chemical reactions , such as silicon carbide sandpaper belt abrasive cloth roll steel processing occurs when following reaction : SiC ( solid ) +4 Fe ( liquid ) → FeSi ( solid ) + Fe3C ( solid) as sandpaper belt abrasive cloth roll and being the processing target a chemical reaction, the abrasive sandpaper belt inherent mechanical properties of the volume change, which affecting the grinding effect .
5 . Ease of processing into particles of different sizes is the use of the abrasive grinding surface composed of many particles to carry out the cutting edge , so the process should sandpaper belt abrasive cloth roll to the desired particle size . Some substances , such as tamping rammer cemented carbide Although high hardness, but because of its toughness is large, compared with sandpaper belt abrasive cloth roll is difficult processed into granules, therefore , not suitable for manufacturing emery cloth sandpaper belt reel .
2013年9月17日星期二
synthetic alternative to natural diamond
Currently, single crystal diamond, PCD (or PCD / CC), and were successfully used for CVD diamond turning, boring tools, drills, reamers, milling cutters, molding knives and other cutting tools Cutting part of the production materials.Varieties of diamond material must be based on the sand paper nature of the material being processed and processing requirements to select, in addition to meet the technical requirements, but also to meet the economic and environmental performance requirements.PCD and PCD / CC materialPCD and PCD / CC is the most commonly used in the production of diamond material, it applies not only usually machining fields, but also widely used in automobiles, motorcycles, high-speed trains, petroleum, chemical, construction, wood processing, and aerospace and other industrial sectors. In the field of cars and motorcycles, PCD and PCD / CC suitable for machining aluminum engine piston skirt, pin hole, cylinder blocks, transmission, carburetor and other wear parts. Most of these components are relatively high silicon content (Si> 12%) of aluminum composite material of high hardness hard particles (such as high hardness of SiC-3000 ~ 3500HV) distributed in the alloy matrix, and if the wheel be the cbn grinding wheel same as the abrasive grains from the cutting edge of the tool abrasion and impact action, leaving the cutting edge wear quickly. The higher the hardness of the hard particles, the larger the particle size, the greater the number of particles, the tool wear faster. Therefore, it is difficult using conventional machining of carbide cutting tools, tool life is very low or impossible to use. Diamond is the world's hardest substance known, the actual use of proven, it is the processing of aluminum matrix composites best tool material.With PCD diamond machining aluminum matrix composites, its cutting speed of tamping rammer up to 800 ~ 1000m/min, tool life is several times higher than the carbide or even several times the surface roughness value of up Ra0.025 ~ 0.012μm. Figure 2 shows the drilling process with PCD tools 20% SiCυ of aluminum matrix composite spiral pump casing application examples.With PCD (or PCD / CC) tooling carbon fiber and glass fiber reinforced plastic (FRP), the chip into a powder, cutting temperature is low, and the length of class K carbide cutting tool 10 times, and not to hard wear carbide tool 1/3PCD (or PCD / CC) also applies to the processing tool after a burn-resistant carbide and non-metallic materials, such as ceramic, rubber, graphite, glass and various wear-resistant timberPCD tool performance depends primarily on its application and the process involved, but the choice of the appropriate grade and particle size can also affect it. Different varieties of PCD inserts, due to its composition of different cutting is very different, and selection must be noted.
sawing machine before installation
commissioning some of the work prepared
One, Saw hydraulic oil should be added on the foot, sliding and rotating parts with a layer of oil.
Second, band sawing machine fitted construction tools with saws, adjustable tension device (rotating saw frame on the left handle) the saw band tension reached a suitable level, while adjusting ran into a good trip switch contact block of iron, in the open state.Third, the cooling water tank Riga enough coolant.Fourth, do more preparatory work, plug in the power, ground must be standard, reliable, turn on the power switch (in the electrical control box), start sawing test, as stated on the wood drill bits label in accordance with rotation correction wiring, while listening to its sound is normal . During operation so that saw bow down automatically with the saw table to drop below 0.5 ~ 1mm, limit switch head hit hit the block automatically rise, when it reaches the limit position height is automatically shut down, three successive experiments. Tension adjustment during operation device in a relaxed state, so leave the hit limit switch contact blocks power off, continuous experiment three times.Fifth, check up, down cylinder device, check the saw bow lift and fall, is reliable and flexible.Six, check the cutting discs clamp, loosen cylinder device, check whether reliable clamping clamping, relaxation is flexible.Seven, adjust the speed control knob, transferred a file (low speed) operation, then governor to two files (high-speed) operation, repeated the experiment three times.Eight, the main motor power switch is turned on, the pump accordingly and start the cooling system to normal operation. Commissioning valves, check the coolant is smooth.Nine, do more preparatory work, the load clamp lock, sawing trial.
One, Saw hydraulic oil should be added on the foot, sliding and rotating parts with a layer of oil.
Second, band sawing machine fitted construction tools with saws, adjustable tension device (rotating saw frame on the left handle) the saw band tension reached a suitable level, while adjusting ran into a good trip switch contact block of iron, in the open state.Third, the cooling water tank Riga enough coolant.Fourth, do more preparatory work, plug in the power, ground must be standard, reliable, turn on the power switch (in the electrical control box), start sawing test, as stated on the wood drill bits label in accordance with rotation correction wiring, while listening to its sound is normal . During operation so that saw bow down automatically with the saw table to drop below 0.5 ~ 1mm, limit switch head hit hit the block automatically rise, when it reaches the limit position height is automatically shut down, three successive experiments. Tension adjustment during operation device in a relaxed state, so leave the hit limit switch contact blocks power off, continuous experiment three times.Fifth, check up, down cylinder device, check the saw bow lift and fall, is reliable and flexible.Six, check the cutting discs clamp, loosen cylinder device, check whether reliable clamping clamping, relaxation is flexible.Seven, adjust the speed control knob, transferred a file (low speed) operation, then governor to two files (high-speed) operation, repeated the experiment three times.Eight, the main motor power switch is turned on, the pump accordingly and start the cooling system to normal operation. Commissioning valves, check the coolant is smooth.Nine, do more preparatory work, the load clamp lock, sawing trial.
2013年9月16日星期一
With an innovative way of producing blade
New era, woodworking equipment are no longer simple tasks such as drilling, open cutting operations such simple processes a single device , the traditional diamond saw only some of the standard process sds plus drill bits stages , reaching effort, time effect , " If you look at appliances, electronics, communications equipment manufacturing plant category , you will find their manufacturing equipment, automation and intelligence to be much more advanced than the furniture , especially in the field of automobile manufacturing , machinery automation can be said to represent the top level, it is also affected by these industries , we have stepped up the development of new processing equipment, woodworking efforts, through numerical control , industrial as well as a more advanced network automation and control , making carving, drilling, cutting and other processes more precise , to achieve a more much shaped timber processing, manufacturing companies to better meet the individual needs of production . "
Although there are still some manufacturers tend to choose the import of foreign equipment, domestic equipment is also true in the machining accuracy slightly inferior to foreign countries, and 4 inch circular saw blade some high-end machinery automation technology abroad China strictly technical monopolies still exist , but the current woodworking machinery and equipment undoubtedly constantly upgraded. Compared to the imported equipment , HE Pei Liu said that the domestic than foreign equipment has several advantages : first, in terms of price , Chinese equipment in the freight and manufacturing costs, etc. is better than abroad , more likely to be a wider range of manufacturing enterprises to accept ; Secondly, in the repair and maintenance areas , post- basic domestic repairs are free , and can respond quickly to the factory to save valuable production time ; addition , more and more need to rely on post- automation equipment and other technical support to upgrade the overall , single in this regard , foreign upgrade cost is quite high . "Because of geography, and other different manufacturing environments , resulting in the use of foreign equipment in the factory various inconveniences , does not tamping rammer necessarily apply to all domestic manufacturers, domestic equipment suppliers closer to the market , a better understanding of plant usage and real needs better able to provide equipment and related services . "
We believe that it is diamond saw blade production level with the world 's advanced level there are still gaps, to promote the healthy development of the industry , companies must be honest self-discipline, strengthen brand building.
Although there are still some manufacturers tend to choose the import of foreign equipment, domestic equipment is also true in the machining accuracy slightly inferior to foreign countries, and 4 inch circular saw blade some high-end machinery automation technology abroad China strictly technical monopolies still exist , but the current woodworking machinery and equipment undoubtedly constantly upgraded. Compared to the imported equipment , HE Pei Liu said that the domestic than foreign equipment has several advantages : first, in terms of price , Chinese equipment in the freight and manufacturing costs, etc. is better than abroad , more likely to be a wider range of manufacturing enterprises to accept ; Secondly, in the repair and maintenance areas , post- basic domestic repairs are free , and can respond quickly to the factory to save valuable production time ; addition , more and more need to rely on post- automation equipment and other technical support to upgrade the overall , single in this regard , foreign upgrade cost is quite high . "Because of geography, and other different manufacturing environments , resulting in the use of foreign equipment in the factory various inconveniences , does not tamping rammer necessarily apply to all domestic manufacturers, domestic equipment suppliers closer to the market , a better understanding of plant usage and real needs better able to provide equipment and related services . "
We believe that it is diamond saw blade production level with the world 's advanced level there are still gaps, to promote the healthy development of the industry , companies must be honest self-discipline, strengthen brand building.
Some of the major diamond wheel applications
By a diamond or cubic boron nitride (CBN) abrasive grinding wheel production , because of its excellent grinding performance , has been widely used for grinding various aspects of the field .
Diamond grinding wheel grinding carbide , glass, ceramics , precious stones high brittle materials effects tools . In recent years , with high-speed ultra-precision grinding technology rapidly grinding
Development , put forward higher diamond bandsaw blades requirements for grinding wheel , ceramic resin bonded grinding wheel has been unable to meet production needs , because of its combination of metal bonded grinding wheel , high strength, good formability ,
Long life and other significant characteristics of the production has been widely used.
Metal bond diamond wheel manufacturers in different ways according to the main there are two types of sintered plating . In order to give full play to the role of super abrasive abroad from the 20th century, 90 years
On behalf of the beginning of the high-temperature brazing process to develop a new wheel, ie high temperature brazing monolayer superabrasive grinding wheels, this wheel is still in the current domestic research and development stage .
2 , sintered diamond wheel
Sintered metal-bonded grinding wheels mostly bronze and other metals as a binder , with the manufacture of high-temperature sintering method , which combines high strength, good formability , high temperature , thermal conductivity
Good wear resistance, long life, can withstand greater loads. Wheel sintering process because inevitably kept the dry cut blades contraction and deformation , so use a facelift before the grinding wheel
But Dresser difficult. Current production methods commonly used plastic roller wheel right when dressing not only time consuming, but the process of finishing off the diamond particles are more trimming
Wheel itself consumes large plastic lower accuracy . France composite dressing method. Electrolytic dressing method is fast , but shaping accuracy is not high ; EDM shaping precision trimming method can be either plastic dressing , but the plastic slowly ; composite dressing method has spark composite electrolytic dressing , mechanical chemical compound trimming method, etc., dressing better, but the system is more complex, so sintered diamond wheel dressing the problem still has not been solved.
Further , since the grinding wheel manufacturing process determines the random surface morphology , each grain geometry, distribution and high degree of inconsistency which the cutting edge , so concrete cutting blade that only a small number of high grinding the cutting edges cut into the workpiece , the grinding quality of the grinding limit further improve the efficiency .
Diamond grinding wheel grinding carbide , glass, ceramics , precious stones high brittle materials effects tools . In recent years , with high-speed ultra-precision grinding technology rapidly grinding
Development , put forward higher diamond bandsaw blades requirements for grinding wheel , ceramic resin bonded grinding wheel has been unable to meet production needs , because of its combination of metal bonded grinding wheel , high strength, good formability ,
Long life and other significant characteristics of the production has been widely used.
Metal bond diamond wheel manufacturers in different ways according to the main there are two types of sintered plating . In order to give full play to the role of super abrasive abroad from the 20th century, 90 years
On behalf of the beginning of the high-temperature brazing process to develop a new wheel, ie high temperature brazing monolayer superabrasive grinding wheels, this wheel is still in the current domestic research and development stage .
2 , sintered diamond wheel
Sintered metal-bonded grinding wheels mostly bronze and other metals as a binder , with the manufacture of high-temperature sintering method , which combines high strength, good formability , high temperature , thermal conductivity
Good wear resistance, long life, can withstand greater loads. Wheel sintering process because inevitably kept the dry cut blades contraction and deformation , so use a facelift before the grinding wheel
But Dresser difficult. Current production methods commonly used plastic roller wheel right when dressing not only time consuming, but the process of finishing off the diamond particles are more trimming
Wheel itself consumes large plastic lower accuracy . France composite dressing method. Electrolytic dressing method is fast , but shaping accuracy is not high ; EDM shaping precision trimming method can be either plastic dressing , but the plastic slowly ; composite dressing method has spark composite electrolytic dressing , mechanical chemical compound trimming method, etc., dressing better, but the system is more complex, so sintered diamond wheel dressing the problem still has not been solved.
Further , since the grinding wheel manufacturing process determines the random surface morphology , each grain geometry, distribution and high degree of inconsistency which the cutting edge , so concrete cutting blade that only a small number of high grinding the cutting edges cut into the workpiece , the grinding quality of the grinding limit further improve the efficiency .
2013年9月15日星期日
saw - some of the factors affecting other
The grit size used in the 30/35 ~ 60/80 range. The more hard rock, should be selected with a finer granularity. Because at the same pressure conditions, the more detailed the more sharp diamond, cut hard rock in favor. In addition, the general requirements of a large-diameter blade cutting efficiency is high, with the coarser particle size should be selected, for example, 30/40, 40/50; small-diameter blade cutting crack chaser efficiency is low, requires smooth rock cutting section, preferably to a smaller particle size, such as 50/60, 60/80.
Segment concentration
The so-called diamond concentration, the diamond in the working layer is the carcass in the density distribution (i.e. contained within the unit area weight of the diamond). "Norms" provides work per cubic centimeter of the matrix containing 4.4 kt diamond, the concentration of 100%, including 3.3 kt diamond, the concentration was 75%. Volume concentration of said agglomerates in the volume occupied by the number of diamond and provides that when the volume of the total volume of the diamond 1/4 concentration of 100%. Increasing the concentration of diamond is expected to extend the life of the blade, because of the increased concentration of each piece of diamond is reduced, the average cutting force suffered. However, increasing the depth of the blade will increase the cost, so there is a concentration of the most economical, and the concentration with VS shear rate increases.
Head hardness binding agents
Generally, the higher the hardness green concrete blades binding agents, the stronger its wear resistance. Thus, when a large rock abrasive cutting, the bonding agent should be high hardness; when the cutting of soft rock material, the hardness of the binding agent should be low; when large and abrasive cutting hard rock, the binding agent should be moderate hardness .
Force effects, temperature effects and grinding damage
Diamond saw blades in the process of cutting stone, will be centrifugal force, cutting power, cutting hot alternating load effect.Because force and temperature effects caused by diamond saw blade worn to donate damage.Force effects: In the cutting process, the blade subject to axial force and tangential force. Because there is in the circumferential direction and the radial force, in the axial direction so that the blade wavy dish in radial direction. Both can cause deformation of the rock section is not flat, stone wasted, sawing noise, vibration intensified, resulting in diamond caking early damage, reduced blade life.Temperature effect: the traditional theory: the influence of temperature on the blade process is mainly manifested in two aspects: First, cause agglomeration of diamond graphitization; two diamond and matrix is caused by the thermal Wilson force caused premature loss of diamond particles . New research showed that: the heat generated during cutting the main incoming agglomeration. Arc temperature is not high, generally between 40 ~ 120 ℃. The abrasive grinding point temperature was high, generally between 250 ~ 700 ℃. The coolant only reduce the average temperature of the arc zone, the temperature has little effect on the grain. This does not result in graphite carbonization temperature, but will make the friction between the abrasive particles and the workpiece change in properties, and to occur between the diamond and the additive thermal stress, which led to a fundamental failure mechanisms curved diamond technology. Studies have shown that the temperature effect is to make the biggest factors blade breakage.Grinding damage: the force effects and temperature than the response, after a period of use of the blade tend to produce wear damage. Grinding damage in the form of mainly the following: abrasive wear, local Edge Pad crushing, a large area of broken off, binders direction along the cutting speed of the mechanical abrasions. Abrasive: Diamond particles and constant friction formula pieces, into a flat edge passivation, loss cutting, increasing friction. Heat causes the cutting surface of the diamond particles graphite sheet, the hardness greatly reduced, increased wear: the surface of the diamond particles exposed to alternating thermal stresses, and also the cutting under alternating stress, fatigue cracks will be partially broken, revealing a sharp new edge, is an ideal wear pattern; large area broken: diamond particles in the Leads to withstand shock loads, the more prominent grain and grain prematurely consumed; shedding: the diamond cutting force alternating binding agent particles are constantly being generated shaking loose. Meanwhile, the cutting process of the binding agent itself wear and cutting heat to soften the binding agent. This makes the gripping force decreased binding agent, when the particle is greater than the cutting force on the gripping force, the diamond particles will fall off. No matter what kind of wear and tear with the diamond particles to withstand load and temperature are closely related. Both of which are determined by Cheng cutting process and cooling lubrication conditions.
Segment concentration
The so-called diamond concentration, the diamond in the working layer is the carcass in the density distribution (i.e. contained within the unit area weight of the diamond). "Norms" provides work per cubic centimeter of the matrix containing 4.4 kt diamond, the concentration of 100%, including 3.3 kt diamond, the concentration was 75%. Volume concentration of said agglomerates in the volume occupied by the number of diamond and provides that when the volume of the total volume of the diamond 1/4 concentration of 100%. Increasing the concentration of diamond is expected to extend the life of the blade, because of the increased concentration of each piece of diamond is reduced, the average cutting force suffered. However, increasing the depth of the blade will increase the cost, so there is a concentration of the most economical, and the concentration with VS shear rate increases.
Head hardness binding agents
Generally, the higher the hardness green concrete blades binding agents, the stronger its wear resistance. Thus, when a large rock abrasive cutting, the bonding agent should be high hardness; when the cutting of soft rock material, the hardness of the binding agent should be low; when large and abrasive cutting hard rock, the binding agent should be moderate hardness .
Force effects, temperature effects and grinding damage
Diamond saw blades in the process of cutting stone, will be centrifugal force, cutting power, cutting hot alternating load effect.Because force and temperature effects caused by diamond saw blade worn to donate damage.Force effects: In the cutting process, the blade subject to axial force and tangential force. Because there is in the circumferential direction and the radial force, in the axial direction so that the blade wavy dish in radial direction. Both can cause deformation of the rock section is not flat, stone wasted, sawing noise, vibration intensified, resulting in diamond caking early damage, reduced blade life.Temperature effect: the traditional theory: the influence of temperature on the blade process is mainly manifested in two aspects: First, cause agglomeration of diamond graphitization; two diamond and matrix is caused by the thermal Wilson force caused premature loss of diamond particles . New research showed that: the heat generated during cutting the main incoming agglomeration. Arc temperature is not high, generally between 40 ~ 120 ℃. The abrasive grinding point temperature was high, generally between 250 ~ 700 ℃. The coolant only reduce the average temperature of the arc zone, the temperature has little effect on the grain. This does not result in graphite carbonization temperature, but will make the friction between the abrasive particles and the workpiece change in properties, and to occur between the diamond and the additive thermal stress, which led to a fundamental failure mechanisms curved diamond technology. Studies have shown that the temperature effect is to make the biggest factors blade breakage.Grinding damage: the force effects and temperature than the response, after a period of use of the blade tend to produce wear damage. Grinding damage in the form of mainly the following: abrasive wear, local Edge Pad crushing, a large area of broken off, binders direction along the cutting speed of the mechanical abrasions. Abrasive: Diamond particles and constant friction formula pieces, into a flat edge passivation, loss cutting, increasing friction. Heat causes the cutting surface of the diamond particles graphite sheet, the hardness greatly reduced, increased wear: the surface of the diamond particles exposed to alternating thermal stresses, and also the cutting under alternating stress, fatigue cracks will be partially broken, revealing a sharp new edge, is an ideal wear pattern; large area broken: diamond particles in the Leads to withstand shock loads, the more prominent grain and grain prematurely consumed; shedding: the diamond cutting force alternating binding agent particles are constantly being generated shaking loose. Meanwhile, the cutting process of the binding agent itself wear and cutting heat to soften the binding agent. This makes the gripping force decreased binding agent, when the particle is greater than the cutting force on the gripping force, the diamond particles will fall off. No matter what kind of wear and tear with the diamond particles to withstand load and temperature are closely related. Both of which are determined by Cheng cutting process and cooling lubrication conditions.
consumption of some of the blade tips
Blade differences,To determine the first fact is used by the blade has a big difference. In our sample, a total of 638 kinds of different blades to maintain the six sets of CNC lathe operation. Good side is that each blade are champions of each category. But the 638 kinds of blades used pack of 10 packaging, means inventory 6,380 blades. And turbo diamond blade all of these are just to maintain six lathe operation. The fact that the number of cutting edges of each blade is relatively small. In many workshops, car blade is still a triangle or diamond. Best combination of number of cutting edges (triangular inserts) and cutting edge strength (diamond blades) are provided on the convex triangular inserts possibility is clearly not sufficient in diamond bandsaw blades many cognitive workshop.
the best advice is to use a large size, strong blade. Carbide used in that era, although hard, but the toughness is not good enough. The strength of the blade through its sizes (= thickness of the blade blade blade = strength) to be guaranteed. A blade of the cutting edge length required at least three times greater than the depth of cut. At the same time two things have changed. On the one hand, the average depth of cut for turning has been significantly reduced. Seco conducted by the study showed that the average today turning cutting depth of about 2.5 ~ 3mm. On the masonry saw blades other hand, today's fourth generation carbide (in TP2500 example) has good toughness, and while its hardness (wear resistance) higher. This means that today's blades, and the cutting depth of the cutting edge length between a complete change to occur. The latest generation (in MF5 example) blade geometry can obviously suited to this new situation.Damage / unused cutting edgeWhen you according to their in-use way to look worn blades, the situation really become clear. The correct form of the cutting edge is worn flank safe, predictable and controllable wear. Cutting edge should not be broken. Cutting edge broken up because of incorrect use or improper use is cutting edge. Being thrown into a box mounted before the cutting edge wear, the cutting edge must be "worn" in. Yet it was discarded for the processing of the "new" cutting edge is always striking.
the best advice is to use a large size, strong blade. Carbide used in that era, although hard, but the toughness is not good enough. The strength of the blade through its sizes (= thickness of the blade blade blade = strength) to be guaranteed. A blade of the cutting edge length required at least three times greater than the depth of cut. At the same time two things have changed. On the one hand, the average depth of cut for turning has been significantly reduced. Seco conducted by the study showed that the average today turning cutting depth of about 2.5 ~ 3mm. On the masonry saw blades other hand, today's fourth generation carbide (in TP2500 example) has good toughness, and while its hardness (wear resistance) higher. This means that today's blades, and the cutting depth of the cutting edge length between a complete change to occur. The latest generation (in MF5 example) blade geometry can obviously suited to this new situation.Damage / unused cutting edgeWhen you according to their in-use way to look worn blades, the situation really become clear. The correct form of the cutting edge is worn flank safe, predictable and controllable wear. Cutting edge should not be broken. Cutting edge broken up because of incorrect use or improper use is cutting edge. Being thrown into a box mounted before the cutting edge wear, the cutting edge must be "worn" in. Yet it was discarded for the processing of the "new" cutting edge is always striking.
2013年9月13日星期五
monocrystalline tool design and application
Carbon atoms, a single diamond crystal, the crystal structure of the highest density of metal atom such as axial face-centered cubic crystal. Diamond crystal connected between the carbon atoms bond to sp3 hybridized covalent bond, with a strong binding force, stability and sds plus drill bits direction. The unique crystal structure of diamond in nature it has the highest hardness, stiffness, refractive index and thermal conductivity, and high wear resistance, corrosion resistance and chemical stability.
Excellent characteristics of single crystal diamond meet the precision and ultra-precision cutting tool material for most of the requirements and is ideal for precision cutting tool materials. Diamond without internal grain boundaries uniform crystal structure so that the tool cutting edge can theoretically reach the atomic level flatness and sharpness, cut thin cutting ability, high precision, cutting force is small; their high hardness and good wear resistance resistance, corrosion resistance and chemical stability can ensure that the tool has a long life, so that it can continue for a long time of cutting, the tool wear can be reduced because of the diamond discs precision of the parts; its high thermal conductivity can be reduced and the cutting temperature parts thermal deformation.
Single crystal diamond tool in the machining field has an important position, is widely used as a mirror, missiles and rockets navigation gyro, computer hard disk substrate accelerator electron gun, such as ultra precision mirror of parts. Can also be used in the manufacture of single crystal diamond eye, brain surgeon's scalpel, thin slicing knives and other bio-medical tools. In addition, single-crystal diamond tool in civilian products processing applications are becoming increasingly widespread, from watch parts, aluminum wet saw blades pistons, jewelry and other processing to pens, high-gloss mirror decorative signs and non-ferrous metal parts processing, its application has entered the machining a variety of areas.
Excellent characteristics of single crystal diamond meet the precision and ultra-precision cutting tool material for most of the requirements and is ideal for precision cutting tool materials. Diamond without internal grain boundaries uniform crystal structure so that the tool cutting edge can theoretically reach the atomic level flatness and sharpness, cut thin cutting ability, high precision, cutting force is small; their high hardness and good wear resistance resistance, corrosion resistance and chemical stability can ensure that the tool has a long life, so that it can continue for a long time of cutting, the tool wear can be reduced because of the diamond discs precision of the parts; its high thermal conductivity can be reduced and the cutting temperature parts thermal deformation.
Single crystal diamond tool in the machining field has an important position, is widely used as a mirror, missiles and rockets navigation gyro, computer hard disk substrate accelerator electron gun, such as ultra precision mirror of parts. Can also be used in the manufacture of single crystal diamond eye, brain surgeon's scalpel, thin slicing knives and other bio-medical tools. In addition, single-crystal diamond tool in civilian products processing applications are becoming increasingly widespread, from watch parts, aluminum wet saw blades pistons, jewelry and other processing to pens, high-gloss mirror decorative signs and non-ferrous metal parts processing, its application has entered the machining a variety of areas.
synthetic trends and characteristics
With synthetic diamond technology matures and China's rapid economic take-off, our country had more diamond tool manufacturing technology accumulation and progress, with a strong manufacturing capacity. As China's enterprises in the huge labor cost advantage, coupled concrete vibrator with technology research and development on the latecomer catch-up situation, making China's enterprises in the product price has obvious advantages crusher manufacturers. The rapid growth in market demand, local companies have launched diamond tools, and the emergence of a number of internationally competitive enterprises competitive strength. China has become the world's most important producer of diamond tools, application and exporting countries, the annual output value of more than ten billion yuan.
1, synthetic diamond industry in the emerging field of application of sand washing machine is expected to further expand the synthetic diamond grade with the continuous improvement of its excellent performance is expected in the high-tech field of linear vibrating screen to be more widely used, such as for aviation instrument bearings , radar tube, optical devices, high-speed and other precision instruments tobacco processing; can be used for monocrystalline silicon, polycrystalline silicon film thickness of 0.1-0.2mm cutting, grinding, satellite solar panels and other high precision machining; can be used for computer chips LSI such fine precision cutting, slotting, back thinned, nano diamond polishing and other processing; purity single crystal diamond large dynamic compression can also be used to produce high-strength test optical window, very environment some devices apertures and fusion energy research components and so on. Including all the cutting wheels world's developed countries, including synthetic diamond superhard materials and products as a development priority, superhard materials and products research and application level in a way represents a country's level of technological development.
2, China's diamond market, a lower proportion of high-grade diamond, the domestic value-added to enhance the space value of superhard materials and products between about 1:3 to 1:6, with the downstream product market size superhard materials growing, superhard materials market prospect is very broad. The market demand for high-grade diamond proportion of the total market is about 60 to 70, according to the current level of domestic technology production of diamond products, the low proportion of high-grade diamond, only about 25 to 30, with 60 market demand contrast, gap of 30 to 35. As China's overall diamond products technology and quality level behind the developed countries for the electronics, automotive, appliance, CNC machining and other industries with more than 90% dependent on imports of high-end products. So our country in the field of high-end hair superhard material impact crusher price development is very big. In recent years, synthetic diamond application objects and applications continue to expand, demand more vigorous, showing a sustained and rapid growth. Manufactured sand making equipment, impact crusher, crusher manufacturers, mill price, cement equipment and other equipment has passed ISO9001 international quality system certification. Welcome to buy!
3, the future growth in demand for diamond prices rose steadily in the coming years, China's diamond market demand can cutting blades still be maintained at an average annual compound growth of 15 or more. According to statistics, in 2001 -2009, the domestic diamond production and sales growth by the 1.6 billion kt to 5.4 billion kt, an average annual compound growth of about 16.4. Next few years China synthetic diamond market demand can still be maintained at an average annual growth of 10 or more, the domestic market demand in 2012 is expected to reach 7 billion kt. With the domestic diamond industry, technological progress and product quality improvement, of synthetic diamond products have been gradually recognized by international customers, according to industry association statistics, in 2001 - 2008 by a number of synthetic diamond exports rose to 153 million karats 1350000000 kt CAGR 37. With our synthetic diamond industry, production capacity and price advantage, China's exports of synthetic diamond and its products will continue to maintain a rapid growth trend.
1, synthetic diamond industry in the emerging field of application of sand washing machine is expected to further expand the synthetic diamond grade with the continuous improvement of its excellent performance is expected in the high-tech field of linear vibrating screen to be more widely used, such as for aviation instrument bearings , radar tube, optical devices, high-speed and other precision instruments tobacco processing; can be used for monocrystalline silicon, polycrystalline silicon film thickness of 0.1-0.2mm cutting, grinding, satellite solar panels and other high precision machining; can be used for computer chips LSI such fine precision cutting, slotting, back thinned, nano diamond polishing and other processing; purity single crystal diamond large dynamic compression can also be used to produce high-strength test optical window, very environment some devices apertures and fusion energy research components and so on. Including all the cutting wheels world's developed countries, including synthetic diamond superhard materials and products as a development priority, superhard materials and products research and application level in a way represents a country's level of technological development.
2, China's diamond market, a lower proportion of high-grade diamond, the domestic value-added to enhance the space value of superhard materials and products between about 1:3 to 1:6, with the downstream product market size superhard materials growing, superhard materials market prospect is very broad. The market demand for high-grade diamond proportion of the total market is about 60 to 70, according to the current level of domestic technology production of diamond products, the low proportion of high-grade diamond, only about 25 to 30, with 60 market demand contrast, gap of 30 to 35. As China's overall diamond products technology and quality level behind the developed countries for the electronics, automotive, appliance, CNC machining and other industries with more than 90% dependent on imports of high-end products. So our country in the field of high-end hair superhard material impact crusher price development is very big. In recent years, synthetic diamond application objects and applications continue to expand, demand more vigorous, showing a sustained and rapid growth. Manufactured sand making equipment, impact crusher, crusher manufacturers, mill price, cement equipment and other equipment has passed ISO9001 international quality system certification. Welcome to buy!
3, the future growth in demand for diamond prices rose steadily in the coming years, China's diamond market demand can cutting blades still be maintained at an average annual compound growth of 15 or more. According to statistics, in 2001 -2009, the domestic diamond production and sales growth by the 1.6 billion kt to 5.4 billion kt, an average annual compound growth of about 16.4. Next few years China synthetic diamond market demand can still be maintained at an average annual growth of 10 or more, the domestic market demand in 2012 is expected to reach 7 billion kt. With the domestic diamond industry, technological progress and product quality improvement, of synthetic diamond products have been gradually recognized by international customers, according to industry association statistics, in 2001 - 2008 by a number of synthetic diamond exports rose to 153 million karats 1350000000 kt CAGR 37. With our synthetic diamond industry, production capacity and price advantage, China's exports of synthetic diamond and its products will continue to maintain a rapid growth trend.
2013年9月12日星期四
Aluminium and aluminum grinding wheel grinding solutions
An aluminum alloy performance : In the non-ferrous materials used in aluminum is more common materials . It 's grinding , mechanical , physical properties of different types of steel and cast iron and other metal material, it has the following characteristics:
1, the hardness is low intensity : The maximum hardness of aluminum HB110 ~ 120, the maximum tensile sds hammer drill bits strength is generally 20 ~ 30kg/cm2. Low hardness , scratch resistance of a material to plastic deformation or poor , the grinding surface is easily scratched and bumps .
2 , the plastic ductility large , the grinding process produces plastic adhesion , blocking wheel surface ; while a low melting point alloy (660 ~ 780 ℃), the temperature in the grinding zone , the surface of the metal melt , adhesive wheel surface , resulting in the increase of the melt adhesion of the blocking wheel .
3, the linear expansion coefficient: the grinding action of heat , the aluminum alloy is easy to cause deformation of the workpiece , thus affecting the precision grinding of the workpiece surface .
4 , the grinding efficiency is low : in order to overcome the alloy produced in grinding the workpiece thermal deformation , reducing the grinding wheel surface adhesion blocking , to ensure the surface quality , to increase the number of dressing , ordinary steel is about 3 times , thus reducing the grinding productivity.
Second, the choice of grinding wheel aluminum : Aluminum grinding process the biggest problem is the " stick" , " block "
A, aluminum ultra- fine grinding , mirror grinding : Use the "PVA" wheel, equivalent to Japan 's "UB" wheel . Can achieve the effect of the mirror . The grinding wheel is also similar in floor polisher pads structure and ceramics ( see below ) .
B, aluminum and semi- coarse grinding :
1 , abrasives : The brittle and sharp black silicon carbide .
2 , binding agents : Use with high strength ceramic binder , and oil, acid, alkali, corrosion resistance .
3 , particle size : to meet the requirements of the case using the coarse number. Coarse : selection of 36 to 46 # ; grinding : the use of 60-80 ; coarse grit No. relatively small number of participating grinding , grinding, less heat , reducing the deformation of the workpiece and the grinding wheel clogged ;
4 , hardness: should opt for a lower hardness, the grinding wheel to maintain a good self-sharpening . Generally used in H ~ J hardness .
5, the organization : an organization should adopt a more accommodating loose debris , so that the cooling fluid into the grinding zone , enhancing the cooling effect, reducing the grinding zone temperature . Should be used in large pores wheel loose organization , with good grinding effect .
Third, the grinding fluid :
Cleaning performance in a well , good lubrication properties , the cooling performance of the grinding fluid. And grinding fluid supply to the full, to ensure a good cleaning and cooling effect. Manufacturers recommend the use of aluminum alloy special grinding mill grinding fluids, such as Castrol 's ALUSOL series. If conditions do not allow the use of diesel as a grinding fluid can , practice effect is still relatively satisfactory. However, the process of using diesel oil mist prone and volatile . In view of this : You can add a small amount of diesel oil or carbon tetrachloride.
Four , grinding techniques:
1 , the grinding process feed rate should be uniform , especially infeed .
2 , the grinding process aluminum wheel is easy to plug , passivation, so the wheel machined surface is prone to scratches and burns , it needs to be lubricated wheel surface machining : coated with lubricating fluid can be increased , oil, cream. You can use paint wheel diesel , but dirty. You can attach the candle , industrial wax , lubricants, lubricating ointment . Can reduce the congestion caused by burns , scratches and so on.
3 , wheel above the sticky aluminum scrap , you can use stone or the use of a favorable blade. Scratch the sticky crumbs.
4, the wheel must be timely cutting discs trimming , trimming some of the rough , but it must be sharp to prevent clogging .
5 , you can use wheel cutter wheel corners down angle . To facilitate the timely discharge of aluminum scrap .
1, the hardness is low intensity : The maximum hardness of aluminum HB110 ~ 120, the maximum tensile sds hammer drill bits strength is generally 20 ~ 30kg/cm2. Low hardness , scratch resistance of a material to plastic deformation or poor , the grinding surface is easily scratched and bumps .
2 , the plastic ductility large , the grinding process produces plastic adhesion , blocking wheel surface ; while a low melting point alloy (660 ~ 780 ℃), the temperature in the grinding zone , the surface of the metal melt , adhesive wheel surface , resulting in the increase of the melt adhesion of the blocking wheel .
3, the linear expansion coefficient: the grinding action of heat , the aluminum alloy is easy to cause deformation of the workpiece , thus affecting the precision grinding of the workpiece surface .
4 , the grinding efficiency is low : in order to overcome the alloy produced in grinding the workpiece thermal deformation , reducing the grinding wheel surface adhesion blocking , to ensure the surface quality , to increase the number of dressing , ordinary steel is about 3 times , thus reducing the grinding productivity.
Second, the choice of grinding wheel aluminum : Aluminum grinding process the biggest problem is the " stick" , " block "
A, aluminum ultra- fine grinding , mirror grinding : Use the "PVA" wheel, equivalent to Japan 's "UB" wheel . Can achieve the effect of the mirror . The grinding wheel is also similar in floor polisher pads structure and ceramics ( see below ) .
B, aluminum and semi- coarse grinding :
1 , abrasives : The brittle and sharp black silicon carbide .
2 , binding agents : Use with high strength ceramic binder , and oil, acid, alkali, corrosion resistance .
3 , particle size : to meet the requirements of the case using the coarse number. Coarse : selection of 36 to 46 # ; grinding : the use of 60-80 ; coarse grit No. relatively small number of participating grinding , grinding, less heat , reducing the deformation of the workpiece and the grinding wheel clogged ;
4 , hardness: should opt for a lower hardness, the grinding wheel to maintain a good self-sharpening . Generally used in H ~ J hardness .
5, the organization : an organization should adopt a more accommodating loose debris , so that the cooling fluid into the grinding zone , enhancing the cooling effect, reducing the grinding zone temperature . Should be used in large pores wheel loose organization , with good grinding effect .
Third, the grinding fluid :
Cleaning performance in a well , good lubrication properties , the cooling performance of the grinding fluid. And grinding fluid supply to the full, to ensure a good cleaning and cooling effect. Manufacturers recommend the use of aluminum alloy special grinding mill grinding fluids, such as Castrol 's ALUSOL series. If conditions do not allow the use of diesel as a grinding fluid can , practice effect is still relatively satisfactory. However, the process of using diesel oil mist prone and volatile . In view of this : You can add a small amount of diesel oil or carbon tetrachloride.
Four , grinding techniques:
1 , the grinding process feed rate should be uniform , especially infeed .
2 , the grinding process aluminum wheel is easy to plug , passivation, so the wheel machined surface is prone to scratches and burns , it needs to be lubricated wheel surface machining : coated with lubricating fluid can be increased , oil, cream. You can use paint wheel diesel , but dirty. You can attach the candle , industrial wax , lubricants, lubricating ointment . Can reduce the congestion caused by burns , scratches and so on.
3 , wheel above the sticky aluminum scrap , you can use stone or the use of a favorable blade. Scratch the sticky crumbs.
4, the wheel must be timely cutting discs trimming , trimming some of the rough , but it must be sharp to prevent clogging .
5 , you can use wheel cutter wheel corners down angle . To facilitate the timely discharge of aluminum scrap .
Diamond wheel types and points to note
Currently, various varieties of diamond grinding wheel . And in hardness is among the most hard substances. There are artificial and natural . Natural is better than artificial . If the diamond blade hardness is now on the market are divided into grade one to ten , then the diamond belongs to ten . It has many advantages. For example, it can be processed into crafts for people to enjoy , can be processed into the table for people to eat , and so on.
Diamond formation principle is kind of how ? Experts to tell you that when the rock contains a substance called carbon element , which in the rock reaches a certain concentration , a strong high pressure, high temperature conditions , after a long run , and finally it will form a diamond . In modern society , the scientists used these principles diamond , artificial diamond can be successful , such as the development of the diamond industry provides a wide range of applications , and now almost all industrial manufacturers use artificial diamond .
There are many varieties of diamond consumption in accordance with a process can be divided into resin diamond wheel diamond grinding wheel joint , metal joint diamond grinding wheel , sintered diamond grinding wheel, electroplated diamond grinding wheel .
Diamond in the use of the time to pay diamomd core drill bits attention to the following aspects:
First, we put the diamond in place when the clamp , pay attention to avoid hitting diamond wheel appearance.
Second, when the correction of the diamond can not be a single point diamond wheel rest vertically aligned intermediate portion , usually skewed to 10-15 °.
Third , you can not conduct heat things suddenly get cold during the dry correction when correction when necessary to adhere to the spacing of the two moments .
Fourth, in the beginning when the rest to find out the location of the highest point of the grinding wheel to be repaired rectification.
Fifth, pay attention to the rest of the process can not stay in one place for too long, will stay long wheel looks polished diamond heat damage occurs rest of things. To change at least once a day to concrete grinding wheel break things.
Sixth, have been damaged , worn something , you can not use a long time , found it to be promptly repaired or replaced.
Seventh, the rest things , you can not pick too big or too small for the amount of the repair in addition to repairs. If you can have a choice , I suggest selecting the same horizontal speed to repair .
Diamond formation principle is kind of how ? Experts to tell you that when the rock contains a substance called carbon element , which in the rock reaches a certain concentration , a strong high pressure, high temperature conditions , after a long run , and finally it will form a diamond . In modern society , the scientists used these principles diamond , artificial diamond can be successful , such as the development of the diamond industry provides a wide range of applications , and now almost all industrial manufacturers use artificial diamond .
There are many varieties of diamond consumption in accordance with a process can be divided into resin diamond wheel diamond grinding wheel joint , metal joint diamond grinding wheel , sintered diamond grinding wheel, electroplated diamond grinding wheel .
Diamond in the use of the time to pay diamomd core drill bits attention to the following aspects:
First, we put the diamond in place when the clamp , pay attention to avoid hitting diamond wheel appearance.
Second, when the correction of the diamond can not be a single point diamond wheel rest vertically aligned intermediate portion , usually skewed to 10-15 °.
Third , you can not conduct heat things suddenly get cold during the dry correction when correction when necessary to adhere to the spacing of the two moments .
Fourth, in the beginning when the rest to find out the location of the highest point of the grinding wheel to be repaired rectification.
Fifth, pay attention to the rest of the process can not stay in one place for too long, will stay long wheel looks polished diamond heat damage occurs rest of things. To change at least once a day to concrete grinding wheel break things.
Sixth, have been damaged , worn something , you can not use a long time , found it to be promptly repaired or replaced.
Seventh, the rest things , you can not pick too big or too small for the amount of the repair in addition to repairs. If you can have a choice , I suggest selecting the same horizontal speed to repair .
2013年9月11日星期三
alloy circular saw blades worn mainly
1, the mechanical wear such wear is cutting edge with the workpiece or the tool surface grooves carved shades caused by wear and tear. The workpiece or tool and the cutting edge with high concrete cutting blade hardness of the workpiece, the tool is smaller than the more easy to wear, so the tool must have a high hardness, in order to improve its wear resistance. 2, adhesive wear in the cutting of plastic material, the cutting and the rake face after the cutting work viscosity, the tool surface or partially lower strength adhesive particles or the workpiece to be cut so that the tool with grinding brush wear. 3, diffusion wear diffusion wear is at a high cutting tool and the workpiece between the mutual diffusion of alloying elements, the tool material physical and mechanical properties of reduced lead increased tool wear. Diffusion is the wear of a chemical nature, such as cemented carbide or titanium carbide added to tantalum carbide and other additives can be 12 inch saw blade added to improve the matrix alloy and the temperature of diffusion and thus improve tool wear resistance and heat resistance. 4, the phase change alloy blades wear use different materials, heat treatment technology or matrix poor too thin, at a certain speed cutting friction process, substrate or material at temperatures above the phase transition temperature, makes the alloy saw blade with accelerated wear, thus losing the cutting ability. Such as ordinary steel 100 °, 65Mn200 °, alloy steel 300-350 °, high-speed steel temperature at 500-600 ° within the matrix phase change will cause. 5, the oxidation is a chemical oxidation wear wear wear, it is 800 degrees or more friction temperature, oxygen in the air and alloys of cobalt, tungsten carbide, titanium, tool wear due to oxidation occurs. 6, the tool wear buildup accuracy is not high or too fast feed rate, wheel selection, and many other factors or unground good blade with the cutting tool material during shock loading or poor toughness, tool face angle for each band will have a shedding blade factors together. 7, soldering temperature is too high or other factors undermine alloy microstructure, high-density ultra-fine particles in the welding alloy cold and hot temperatures, or high temperature, resulting alloy cracking, alloy crystal thicker, lower alloy matrix strength and deformation durability. 8, angle design and cutting material discrepancies caused by tool wear, and all kinds of plastic materials with different hardness not targeted under the correct selection of a suitable cutting blades alloy, nor according to the hardness of the cutting material dry cutting angle of impact of each plane thereby reducing tool life. 9, sharpening precision and process affect wear, alloy circular saw blades are precision cutting tools, any main and sub-edge blade with tape, face cutting straight face, or radial cutting rather than a cutting line, each one formed alloy cutting point or depth, and many other factors that reduce their effectiveness. 10, improper operation or maintenance of the wear and tear caused by improper, each cutting equipment, cutting feed rate is not the same, while the alloy saw blade is designed according to different cutting material various angles, with inappropriate will reduce its effectiveness.
affect the diamond tool wear several reasons
Determine the tool cutting tool material is a fundamental factor for the processing efficiency, processing quality,
Processing costs as well as a great influence on tool life. The more rigid tool material, the better the bandsaw blades wear resistance, the higher the hardness, the lower the impact toughness, the material is hard. Hardness and toughness is a contradiction, but also the tool material that should overcome a key. For graphite tools, ordinary coating can be the appropriate choice in the selection of the relative toughness a little better, which is slightly higher cobalt content, for the diamond-coated graphite tool, you can choose in the selection hardness is relatively better, that is, slightly lower solids content.
2, the tool geometry graphite select the appropriate tool geometry, helps to reduce tool vibration, in turn, is not easy to collapse graphite piece missing; (a) rake angle, with a negative rake angle machining graphite, the tool edge mouth better strength, resistance to concrete cutting blade impact and friction performance, along with the decrease of the absolute value of the negative rake angle, flank wear area changed little, but the overall decreasing trend, with positive rake angle machining, with the former angle increases, the tool edge strength is weakened, but led to increased flank wear. Negative rake angle machining, cutting resistance, increasing the cutting vibration, using a large positive rake angle machining, tool wear serious, cutting vibration as well. (2) After the corner, if after the angle increases, the tool edge strength is reduced, the flank wear area increases. After the tool angle is too large, the cutting vibration strengthened. (3) helix angle, helix angle is small, while the same cut on the cutting edge of the blade length the longest piece of graphite, the maximum cutting resistance, the cutting tool to withstand the maximum impact force, and thus tool wear, cutting force and cutting vibration are the largest . When the helix angle to the larger, the direction of the milling force large degree of deviation from the workpiece surface, chipping graphite material due to the impact caused by the cutting intensified, and thus tool wear, cutting force and cutting vibration it has also increased. Therefore, the tool angle change on the tool wear, cutting force and cutting vibration is rake angle, clearance angle and helix angle integrated generated, so the choice we must pay more attention. Through the processing characteristics of the graphite material lot of scientific tests, PARA optimize the tools that the tool geometry, so that the overall cutting tool is greatly increased. Three, coated diamond coated tool cutter high hardness, good wear resistance and low coefficient of friction, at this stage diamond-coated graphite machining tool is the best choice, but also the tool that best reflects the superior performance of graphite; diamond-coated carbide tools advantage is the combination of natural diamond carbide hardness and strength and fracture toughness; But in the domestic diamond coating technology is still in its infancy, as well as the cost of inputs are big, diamond coating so there is not much development in the near future, but we can on the basis of the common tool to optimize the angle of the tool, and the material so as to improve the structure of the conventional coatings in a way which can be processed in graphite Applications. Diamond-coated tools and the general geometry of coated tools are essentially different, so the design of diamond coated tools, due to the particularity of graphite machining, its geometry can be properly amplified volume becomes large cut groove, it will not reduce the wear resistance of the tool edge port; for ordinary TiAlN coating, although the ratio of its uncoated tool wear significantly improved, but compared to diamond coating, in the processing of its geometry graphite should be appropriate to put a small, in order to increase its wear resistance. The diamond coating, the coating of the world many companies invest a lot of manpower and material resources to research and development related to coating technology, but so far, foreign companies mature and economical coating confined to Europe; PARA as a subsection excellent graphite machining tool, also using the circular blades world's most advanced coating technology for surface treatment of the tool, in order to ensure that the processing life while ensuring the economic and practical tool. 4, the tool edge enhancement tool edge passivation technology is one not to be widespread attention, but is a very important issue. After the diamond wheel grinding carbide tool edge, there is a different degree of micro-gap (ie micro chipping and saw cut). Graphite speed cutting machining tool performance and stability of the proposed higher requirements, especially in the coating of diamond coated tools must elapse before the knife edge passivation treatment in order to ensure the robustness and service life of the coating. Passivation purpose is to solve the above tool, the tool cutting edge grinding gap microscopic defects, to reduce or eliminate the peak value, to smooth smooth, strong and durable both sharp object.
Processing costs as well as a great influence on tool life. The more rigid tool material, the better the bandsaw blades wear resistance, the higher the hardness, the lower the impact toughness, the material is hard. Hardness and toughness is a contradiction, but also the tool material that should overcome a key. For graphite tools, ordinary coating can be the appropriate choice in the selection of the relative toughness a little better, which is slightly higher cobalt content, for the diamond-coated graphite tool, you can choose in the selection hardness is relatively better, that is, slightly lower solids content.
2, the tool geometry graphite select the appropriate tool geometry, helps to reduce tool vibration, in turn, is not easy to collapse graphite piece missing; (a) rake angle, with a negative rake angle machining graphite, the tool edge mouth better strength, resistance to concrete cutting blade impact and friction performance, along with the decrease of the absolute value of the negative rake angle, flank wear area changed little, but the overall decreasing trend, with positive rake angle machining, with the former angle increases, the tool edge strength is weakened, but led to increased flank wear. Negative rake angle machining, cutting resistance, increasing the cutting vibration, using a large positive rake angle machining, tool wear serious, cutting vibration as well. (2) After the corner, if after the angle increases, the tool edge strength is reduced, the flank wear area increases. After the tool angle is too large, the cutting vibration strengthened. (3) helix angle, helix angle is small, while the same cut on the cutting edge of the blade length the longest piece of graphite, the maximum cutting resistance, the cutting tool to withstand the maximum impact force, and thus tool wear, cutting force and cutting vibration are the largest . When the helix angle to the larger, the direction of the milling force large degree of deviation from the workpiece surface, chipping graphite material due to the impact caused by the cutting intensified, and thus tool wear, cutting force and cutting vibration it has also increased. Therefore, the tool angle change on the tool wear, cutting force and cutting vibration is rake angle, clearance angle and helix angle integrated generated, so the choice we must pay more attention. Through the processing characteristics of the graphite material lot of scientific tests, PARA optimize the tools that the tool geometry, so that the overall cutting tool is greatly increased. Three, coated diamond coated tool cutter high hardness, good wear resistance and low coefficient of friction, at this stage diamond-coated graphite machining tool is the best choice, but also the tool that best reflects the superior performance of graphite; diamond-coated carbide tools advantage is the combination of natural diamond carbide hardness and strength and fracture toughness; But in the domestic diamond coating technology is still in its infancy, as well as the cost of inputs are big, diamond coating so there is not much development in the near future, but we can on the basis of the common tool to optimize the angle of the tool, and the material so as to improve the structure of the conventional coatings in a way which can be processed in graphite Applications. Diamond-coated tools and the general geometry of coated tools are essentially different, so the design of diamond coated tools, due to the particularity of graphite machining, its geometry can be properly amplified volume becomes large cut groove, it will not reduce the wear resistance of the tool edge port; for ordinary TiAlN coating, although the ratio of its uncoated tool wear significantly improved, but compared to diamond coating, in the processing of its geometry graphite should be appropriate to put a small, in order to increase its wear resistance. The diamond coating, the coating of the world many companies invest a lot of manpower and material resources to research and development related to coating technology, but so far, foreign companies mature and economical coating confined to Europe; PARA as a subsection excellent graphite machining tool, also using the circular blades world's most advanced coating technology for surface treatment of the tool, in order to ensure that the processing life while ensuring the economic and practical tool. 4, the tool edge enhancement tool edge passivation technology is one not to be widespread attention, but is a very important issue. After the diamond wheel grinding carbide tool edge, there is a different degree of micro-gap (ie micro chipping and saw cut). Graphite speed cutting machining tool performance and stability of the proposed higher requirements, especially in the coating of diamond coated tools must elapse before the knife edge passivation treatment in order to ensure the robustness and service life of the coating. Passivation purpose is to solve the above tool, the tool cutting edge grinding gap microscopic defects, to reduce or eliminate the peak value, to smooth smooth, strong and durable both sharp object.
2013年9月10日星期二
diamond tool chucking three ways
We all know that a diamond tool chucking quality directly affects the performance of diamond tools , diamond tools described below under three chucking method:
1 bonding method
Epoxy adhesive used is an organic binder such as gum or 502 will be bonded diamond blade arbor wet diamond polishing pads with diamond segments to match the size of the groove. This method is simple , does not require special equipment and fixtures, get a certain bond strength . When the tool requires grinding , you need to first bond with a solvent such as acetone gel open , right diamond blade for grinding and re- bonded to the arbor . In addition, diamond blade bonding process is more difficult to ensure positional accuracy .
(2) Setting
Mosaic Law is the first diamond blade with sintered metal powder together , then head through the diamond plate mechanically fixed to the arbor .
3 Brazing Method
By brazing method directly welded diamond cutting tool has been a popular concern. Since diamond has a high chemical stability , it is difficult chemical reaction with other metals, and the welding , therefore , to reliably achieve the diamond is firmly connected with the metal , a diamond tool manufacturing technology solved difficulties and 4 inch saw blades research.
diamond wheel safekeepingDiamond grinding wheel has a unique performance characteristics, we should also be stored in the custody properly , let's take a look at the diamond grinding wheel should be stored at :
Do not contact with corrosive gases and liquids , especially resin bond diamond grinding wheel, resin contact with corrosive chemicals cause the performance change.
Diamond grinding wheel in the handling storage, be careful not to collide , resin bonded grinding wheel and ceramic bonded grinding wheel after a collision prone gap, rupture.
Do not use the diamond wheel into , they should immediately wash the coolant to keep the wheel surface clean to prevent further oil coolant inside wheel , causing the wheel again when the imbalance .
Try stored at room concrete diamond blades temperature, diamond grinding wheel , avoid contact with high temperature or low temperature .
Due to the effects of aging resin , resin diamond wheels generally do not exceed one year shelf life , otherwise , it will affect the normal use. If you must use , must then be related to safety testing .
1 bonding method
Epoxy adhesive used is an organic binder such as gum or 502 will be bonded diamond blade arbor wet diamond polishing pads with diamond segments to match the size of the groove. This method is simple , does not require special equipment and fixtures, get a certain bond strength . When the tool requires grinding , you need to first bond with a solvent such as acetone gel open , right diamond blade for grinding and re- bonded to the arbor . In addition, diamond blade bonding process is more difficult to ensure positional accuracy .
(2) Setting
Mosaic Law is the first diamond blade with sintered metal powder together , then head through the diamond plate mechanically fixed to the arbor .
3 Brazing Method
By brazing method directly welded diamond cutting tool has been a popular concern. Since diamond has a high chemical stability , it is difficult chemical reaction with other metals, and the welding , therefore , to reliably achieve the diamond is firmly connected with the metal , a diamond tool manufacturing technology solved difficulties and 4 inch saw blades research.
diamond wheel safekeepingDiamond grinding wheel has a unique performance characteristics, we should also be stored in the custody properly , let's take a look at the diamond grinding wheel should be stored at :
Do not contact with corrosive gases and liquids , especially resin bond diamond grinding wheel, resin contact with corrosive chemicals cause the performance change.
Diamond grinding wheel in the handling storage, be careful not to collide , resin bonded grinding wheel and ceramic bonded grinding wheel after a collision prone gap, rupture.
Do not use the diamond wheel into , they should immediately wash the coolant to keep the wheel surface clean to prevent further oil coolant inside wheel , causing the wheel again when the imbalance .
Try stored at room concrete diamond blades temperature, diamond grinding wheel , avoid contact with high temperature or low temperature .
Due to the effects of aging resin , resin diamond wheels generally do not exceed one year shelf life , otherwise , it will affect the normal use. If you must use , must then be related to safety testing .
has the characteristics of diamond abrasive
Diamond grinding wheel is one of the products , high quality products and thoughtful service to win the majority of customers , let's introduce the use of diamond grinding wheel :
As with the characteristics of diamond abrasive ( high hardness , high compressive wet polishing pad strength , good wear resistance ) , the diamond abrasive in grinding become hard and brittle materials and carbide grinding ideal tool not only high efficiency, precision high, and good roughness , abrasive consumption, long life, but can also improve working conditions . It is widely used for general abrasive difficult to process low iron content of the metal and non-metallic brittle materials , such as cemented carbide , alumina ceramic , optical glass , agate gemstone , semiconductor concrete cutting blade materials , stone and so on.
Abrasive diamond wheels are widely used in general difficult to process the low iron content of the metal and non-metallic brittle materials , such as tungsten carbide ( carbide ) , alumina ceramic , optical glass , agate gemstone , semiconductor wet saw blades materials, stone, ceramic , iron oxygen , brittle materials such as semiconductor materials and metallic materials, grinding , carbide materials, shape processing , electrolytic grinding, and grinding center drill with diamond grinding other heavy-duty cutting , grinding wear with good , high efficiency, long life characteristics .
As with the characteristics of diamond abrasive ( high hardness , high compressive wet polishing pad strength , good wear resistance ) , the diamond abrasive in grinding become hard and brittle materials and carbide grinding ideal tool not only high efficiency, precision high, and good roughness , abrasive consumption, long life, but can also improve working conditions . It is widely used for general abrasive difficult to process low iron content of the metal and non-metallic brittle materials , such as cemented carbide , alumina ceramic , optical glass , agate gemstone , semiconductor concrete cutting blade materials , stone and so on.
Abrasive diamond wheels are widely used in general difficult to process the low iron content of the metal and non-metallic brittle materials , such as tungsten carbide ( carbide ) , alumina ceramic , optical glass , agate gemstone , semiconductor wet saw blades materials, stone, ceramic , iron oxygen , brittle materials such as semiconductor materials and metallic materials, grinding , carbide materials, shape processing , electrolytic grinding, and grinding center drill with diamond grinding other heavy-duty cutting , grinding wear with good , high efficiency, long life characteristics .
2013年9月9日星期一
Some of the advantages of diamond tools
Diamond tools are widely used in the manufacturing industry , then how about diamond tools trends ? Following is a brief introduction, I hope for your help:
A , variety , product series : Domestic Diamond Products showing species diversity, product refinement , the diamond blade application of the trend of specialization . General scale enterprises have dozens of product specifications , a slight scale enterprises have hundreds of product specifications, larger enterprises with thousands of product specifications and the products can be customized according to user requirements .
2, the product according to user requirements are divided into two classes: the use of diamond tools, habits and glass blades cost factors, have been artificially divided into two distinct series : First, a larger amount of relatively low price DIY products , such products have a greater market ; two major international markets for high-end professional products. As in recent years, China 's rapid diamond production and quality improvement to be diamond products production technology continues to improve , China's high-end products, diamond tools manufacturing level has made significant progress, and the price advantage is obvious , professional products in the international market competitiveness has enhanced .
3 In recent years, various formulations of pre-alloy powder , adding rare earth metal carcass powder material stone polishing pads applications and single ( multi ) brazing technology , diamond in the carcass ordered , innovation and other new matrix structure technology development, production of many new high-performance products , has greatly improved the industry's product structure, improve efficiency and expand the international market.
A , variety , product series : Domestic Diamond Products showing species diversity, product refinement , the diamond blade application of the trend of specialization . General scale enterprises have dozens of product specifications , a slight scale enterprises have hundreds of product specifications, larger enterprises with thousands of product specifications and the products can be customized according to user requirements .
2, the product according to user requirements are divided into two classes: the use of diamond tools, habits and glass blades cost factors, have been artificially divided into two distinct series : First, a larger amount of relatively low price DIY products , such products have a greater market ; two major international markets for high-end professional products. As in recent years, China 's rapid diamond production and quality improvement to be diamond products production technology continues to improve , China's high-end products, diamond tools manufacturing level has made significant progress, and the price advantage is obvious , professional products in the international market competitiveness has enhanced .
3 In recent years, various formulations of pre-alloy powder , adding rare earth metal carcass powder material stone polishing pads applications and single ( multi ) brazing technology , diamond in the carcass ordered , innovation and other new matrix structure technology development, production of many new high-performance products , has greatly improved the industry's product structure, improve efficiency and expand the international market.
vitrified diamond wheel diamond and ceramic binder with common characteristics
Diamond grinding wheel is grinding carbide , glass, ceramics , precious stones high brittle materials effects tools . In recent years , with high-speed grinding ultra -precision grinding technology developed rapidly , put a higher demand on the grinding wheel , ceramic diamond cbn wheel resin bonded grinding wheel has been unable to meet production needs , because of its combination of metal bonded grinding wheel , high strength, good formability , long life and other significant characteristics of the production has been widely used. Metal bond diamond wheel manufacturers in different ways according to a major sintering , plating two types. In order to give full play to the role of super abrasive abroad from the 20th century, the early 90s with a high temperature brazing process to develop a new wheel, ie high temperature brazing monolayer superabrasive grinding wheels, this wheel is still in the current domestic research and development stage . Ceramic diamond wheel vitrified diamond grinding wheel with diamond and vitrified common characteristics , and general corundum , silicon carbide grinding wheel compared to its grinding force , grinding temperature is relatively low, the wheel wear is relatively small ; can be adapted to each species coolant effect; grinding wheel is good shape retention , high precision grind the diamond blade circular saw workpiece ; wheel has more pores , grinding and heat conducive chip , clogging , easy to burn the workpiece ; wheel good self-sharpening , finishing a long time interval , trimming easier . Therefore, vitrified diamond grinding wheel used in some foreign countries is increasing. Sintered diamond wheel
Sintered metal-bonded grinding wheels mostly bronze and other metals as a binder , with the manufacture of high-temperature sintering method , which combines high strength, good formability , high temperature , thermal conductivity, good wear resistance, long life, can withstand greater loads. Electroplated diamond grinding wheel : ① plating process is simple, less investment, ease of manufacture ; ② without dressing , easy to use ; ③ monolayer structure determines that it can achieve a high work rate, currently abroad has reached 250 ~ 300m / s; ④ Although only a single layer of diamond , but there is still enough life ; ⑤ for high accuracy, roller wheels, electroplated 4 inch saw blades unique manufacturing method. Precisely because of these advantages , plating wheel speed, ultra- high speed grinding occupy undisputed dominance.
Sintered metal-bonded grinding wheels mostly bronze and other metals as a binder , with the manufacture of high-temperature sintering method , which combines high strength, good formability , high temperature , thermal conductivity, good wear resistance, long life, can withstand greater loads. Electroplated diamond grinding wheel : ① plating process is simple, less investment, ease of manufacture ; ② without dressing , easy to use ; ③ monolayer structure determines that it can achieve a high work rate, currently abroad has reached 250 ~ 300m / s; ④ Although only a single layer of diamond , but there is still enough life ; ⑤ for high accuracy, roller wheels, electroplated 4 inch saw blades unique manufacturing method. Precisely because of these advantages , plating wheel speed, ultra- high speed grinding occupy undisputed dominance.
订阅:
博文 (Atom)