Serrated portion angle parameter is more complex, but also the most professional, and the correct choice of the blade cutting angle parameter is to determine the quality of the key. The router bits main point of argument is the rake angle, clearance angle, wedge angle.
Rake angle sawing wood consumed by the main impact force. Serrated cutting rake angle greater sharpness better, more portable sawing, pushing more effort. Generally relatively soft material to be processed, the selected larger rake angle, otherwise choose a smaller rake angle.
Sawtooth angle is in diamond cbn wheel the cutting position when the sawtooth. Serrated cutting angle affect performance results. Greatest impact is on the cutting rake angle γ, posterior horn α, wedge angle β. Rake angle γ is serrated cutting edge angle, the greater the cutting rake angle the more light, the rake angle is generally between 10-15 ℃. After the angle of the teeth and the angle between the machined surface, and its role is to prevent aliasing of the machined surface friction, the concrete blades friction after the smaller the greater the angle, the more smooth processing of products. Carbide saw blade rear corner general value 15 ℃. Wedge angle is the angle from the front and rear angles derived. However, the wedge angle is not too small, it plays the strength to keep the teeth according to, heat resistance, durability of the effect. Rake angle γ, posterior horn α, wedge angle β is equal to the higher of 90 ℃.
diamond core drills, not only in geological exploration has an important position, but also because it has got speed, stone loss, does not destroy the surrounding environment and other unique advantages and is widely used in marble, granite, reinforced concrete walls of the drill hole
PCD grinding wheel
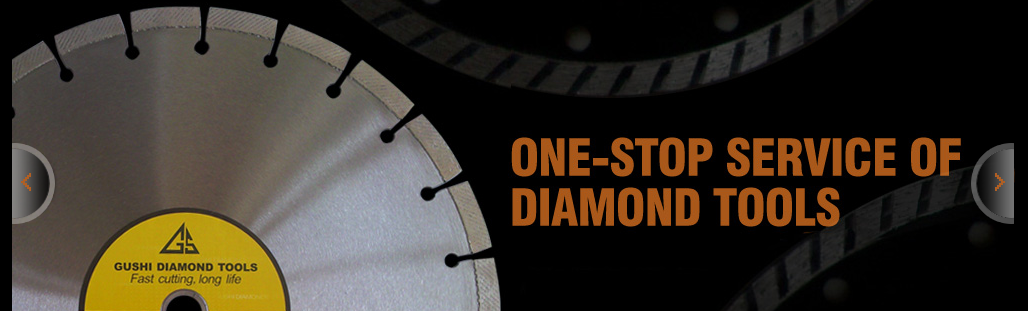
2013年8月30日星期五
Diamond Saw Precautions
One, saw the installation steps
1, unplug the power tool plugs.
2, clear the dirt on the flange and blade.
3, pay attention to the motor shaft assembly center hole with the blade, according to the correct direction of rotation of the blade installation.
4, the self-locking nut cbn grinding wheels fixed tight before turning on the power, turn the blade by hand checks are installed correctly.
5, cutting idle a few minutes before, after confirming that no sway or jump in on the first try or silicon carbide bricks several times, and then work.
Second, the maintenance and repair
1, such as the saw blade on the sticky glaze or paint and other materials attached with a grinding wheel or sandpaper to remove them.
2, do not bend the blade for grinding or cutting, straight cutting blade for normal function.
3, diamond saw blade for fast cutting granite, marble, concrete, cement, ceramic, brick and some other inorganic non-metallic brittle materials can also be used for cutting, such as asphalt, cinder blocks, soft cement, mortar joints, etc. Some soft materials. Do not cut metal, otherwise it would blunt blade, shorten life.
4, if the saw blade use for some time, the surface is smooth, diamond protrusion is small, the performance of the blade is not sharp. The right approach: re-open with a blade wheel or bricks, in order to facilitate the removal of metal carcass wrapped part of the normal of the diamond blade to enhance blade sharpness. Not continuously use has been polished up the saw blade, the blade can not be used continuously overheating.
Third, the security warning
1, the protective device fitted to the blade, so that it can be cut safely and effectively protect the operator.
2, wear face protection can ease Diamond tool breathing apparatus to avoid inhalation of excessive dust.
3 Do not wear loose clothing to avoid being caught in the rotating blades.
4, the cutting depth should be deeper than the material being cut.
5, according to their maximum speed of the cutting operation.
6, do not force the blade has cut through the material, according to the uniform cutting blade sharpness.
7, cutting the cut material to be fixed well.
Fourth, the proper use of the principle of
1, before the blade should confirm whether the damage, if damaged strictly prohibited! All cutters must install protective cover!
2, in accordance with the 4 inch circular saw blade direction of rotation indicated blade blade fastening installation is forbidden cutting curves, powerful cutting, thermal cutting.
3, the operator must use safety glasses, protective masks, overalls, protective shoes and other protective clothing.
4, should be based on the performance of stone select the appropriate blade.
5, cutting the use of cooling water, water quality requirements, the key to the water must be guaranteed, otherwise it will greatly affect blade life and sharpness.
6, the blade becomes dull during cutting, grinding wheel in silicon carbide scrap or firebrick grinding on the blade.
1, unplug the power tool plugs.
2, clear the dirt on the flange and blade.
3, pay attention to the motor shaft assembly center hole with the blade, according to the correct direction of rotation of the blade installation.
4, the self-locking nut cbn grinding wheels fixed tight before turning on the power, turn the blade by hand checks are installed correctly.
5, cutting idle a few minutes before, after confirming that no sway or jump in on the first try or silicon carbide bricks several times, and then work.
Second, the maintenance and repair
1, such as the saw blade on the sticky glaze or paint and other materials attached with a grinding wheel or sandpaper to remove them.
2, do not bend the blade for grinding or cutting, straight cutting blade for normal function.
3, diamond saw blade for fast cutting granite, marble, concrete, cement, ceramic, brick and some other inorganic non-metallic brittle materials can also be used for cutting, such as asphalt, cinder blocks, soft cement, mortar joints, etc. Some soft materials. Do not cut metal, otherwise it would blunt blade, shorten life.
4, if the saw blade use for some time, the surface is smooth, diamond protrusion is small, the performance of the blade is not sharp. The right approach: re-open with a blade wheel or bricks, in order to facilitate the removal of metal carcass wrapped part of the normal of the diamond blade to enhance blade sharpness. Not continuously use has been polished up the saw blade, the blade can not be used continuously overheating.
Third, the security warning
1, the protective device fitted to the blade, so that it can be cut safely and effectively protect the operator.
2, wear face protection can ease Diamond tool breathing apparatus to avoid inhalation of excessive dust.
3 Do not wear loose clothing to avoid being caught in the rotating blades.
4, the cutting depth should be deeper than the material being cut.
5, according to their maximum speed of the cutting operation.
6, do not force the blade has cut through the material, according to the uniform cutting blade sharpness.
7, cutting the cut material to be fixed well.
Fourth, the proper use of the principle of
1, before the blade should confirm whether the damage, if damaged strictly prohibited! All cutters must install protective cover!
2, in accordance with the 4 inch circular saw blade direction of rotation indicated blade blade fastening installation is forbidden cutting curves, powerful cutting, thermal cutting.
3, the operator must use safety glasses, protective masks, overalls, protective shoes and other protective clothing.
4, should be based on the performance of stone select the appropriate blade.
5, cutting the use of cooling water, water quality requirements, the key to the water must be guaranteed, otherwise it will greatly affect blade life and sharpness.
6, the blade becomes dull during cutting, grinding wheel in silicon carbide scrap or firebrick grinding on the blade.
2013年8月29日星期四
four strokes teach you to identify good
Quality stone products currently on the market varies greatly, decorative stone for the processed product, its quality can be used to identify four aspects:
A concept, namely the wet diamond polishing pads naked eye stone surface structure. In general, uniform fine structure of the stone material with a delicate texture, for the stone to share; ranging from coarse grain structure of the stone and its appearance is poor. In addition, the stone due to the impact of geological processes which often produce some minor cracks in the stone along these areas most vulnerable to rupture, should pay attention to the screening. As for the lack of impact of more angular appearance, particular attention should be selected.
Two volume, ie the amount of stone sizes, so as concrete cutting not to affect splicing, or cause splicing patterns, patterns, lines, deformation, affecting the decorative effect.
Three, that is to listen stone percussion sounds. In general, good quality stone its clear crisp percussion; contrary, if the stone house there is a slight crack or indirect result of weathering resulting thixotropic loose particles, then the percussion sound gruff.
Four test, which uses a simple 14 inch saw blade test method to test the quality of the stone or bad. Usually drops on the back a stone pellets ink, such as ink quickly disperse leaching, which indicates the presence of stone or loose particles inside the gap, stone poor quality; Conversely, if the ink droplets in place does not move, then the stone texture is good.
A concept, namely the wet diamond polishing pads naked eye stone surface structure. In general, uniform fine structure of the stone material with a delicate texture, for the stone to share; ranging from coarse grain structure of the stone and its appearance is poor. In addition, the stone due to the impact of geological processes which often produce some minor cracks in the stone along these areas most vulnerable to rupture, should pay attention to the screening. As for the lack of impact of more angular appearance, particular attention should be selected.
Two volume, ie the amount of stone sizes, so as concrete cutting not to affect splicing, or cause splicing patterns, patterns, lines, deformation, affecting the decorative effect.
Three, that is to listen stone percussion sounds. In general, good quality stone its clear crisp percussion; contrary, if the stone house there is a slight crack or indirect result of weathering resulting thixotropic loose particles, then the percussion sound gruff.
Four test, which uses a simple 14 inch saw blade test method to test the quality of the stone or bad. Usually drops on the back a stone pellets ink, such as ink quickly disperse leaching, which indicates the presence of stone or loose particles inside the gap, stone poor quality; Conversely, if the ink droplets in place does not move, then the stone texture is good.
What kind of stone
Used in building decoration industry two basic types of stone is natural stone and artificial stone. Natural stone such as marble, granite, limestone and so on.
Natural stone can be broadly classified into three categories. Igneous rocks are rocks from the mantle or crust by melting or partial melting of the material such as magma cools consolidation formation, granite is an igneous rock; sedimentary rock is not too deep in the wet saw blades ground where the other rocks and some volcanic weathering products ejecta, moving through water or glaciers, sedimentation, diagenesis rocks, limestone and sandstone fall into this category; rocks and minerals at high temperature and pressure under the action of a mixture of natural deterioration from one stone to another stone, marble, slate, quartzite rocks belong.
Granite is a very hard igneous rock, its high density, resistance to scratches and corrosion. It is ideally suited for flooring and kitchen countertops. There are hundreds of varieties of granite.
Marble is a derivative of limestone, marble, a metamorphic rock can be polished. Marble has a soft easy to scratch or turbo diamond blade acid corrosion. Around the world there are countless types of marble.
Limestone is a sedimentary rock is composed of calcite and sediment composition, forming a variety of colors.
Sandstone is a sedimentary rock, which is mainly composed of loose particles of quartz sand, rough texture, sandstone, there are many varieties to choose from.
Travertine is part of the metamorphic limestone, due to its structure, can fill, you can polish and high density, it has become one of the marble.
Slate is a metamorphic rock, original rock was muddy, silty or neutral tuff, management direction along the plate can peel into thin slices. Slate color with impurities they 12 inch saw blade contain varies, iron is red or yellow; carbonaceous for black or gray; calcium can cause foaming in case of hydrochloric acid, so named for the color of its general classification, as will green slate, black slate, calcareous slate.
Artificial stone is a mixture is made of non-natural, such as resin, cement, glass beads, aluminum powder, etc. plus gravel adhesives. Artificial stone (also known as "artificial marble"). Artificial stone came 30 years ago in the United States, one of the earliest applications of artificial stone as a decorative material is the mid-1990s a number of coastal cities, a few years after the widely popular.
Natural stone can be broadly classified into three categories. Igneous rocks are rocks from the mantle or crust by melting or partial melting of the material such as magma cools consolidation formation, granite is an igneous rock; sedimentary rock is not too deep in the wet saw blades ground where the other rocks and some volcanic weathering products ejecta, moving through water or glaciers, sedimentation, diagenesis rocks, limestone and sandstone fall into this category; rocks and minerals at high temperature and pressure under the action of a mixture of natural deterioration from one stone to another stone, marble, slate, quartzite rocks belong.
Granite is a very hard igneous rock, its high density, resistance to scratches and corrosion. It is ideally suited for flooring and kitchen countertops. There are hundreds of varieties of granite.
Marble is a derivative of limestone, marble, a metamorphic rock can be polished. Marble has a soft easy to scratch or turbo diamond blade acid corrosion. Around the world there are countless types of marble.
Limestone is a sedimentary rock is composed of calcite and sediment composition, forming a variety of colors.
Sandstone is a sedimentary rock, which is mainly composed of loose particles of quartz sand, rough texture, sandstone, there are many varieties to choose from.
Travertine is part of the metamorphic limestone, due to its structure, can fill, you can polish and high density, it has become one of the marble.
Slate is a metamorphic rock, original rock was muddy, silty or neutral tuff, management direction along the plate can peel into thin slices. Slate color with impurities they 12 inch saw blade contain varies, iron is red or yellow; carbonaceous for black or gray; calcium can cause foaming in case of hydrochloric acid, so named for the color of its general classification, as will green slate, black slate, calcareous slate.
Artificial stone is a mixture is made of non-natural, such as resin, cement, glass beads, aluminum powder, etc. plus gravel adhesives. Artificial stone (also known as "artificial marble"). Artificial stone came 30 years ago in the United States, one of the earliest applications of artificial stone as a decorative material is the mid-1990s a number of coastal cities, a few years after the widely popular.
2013年8月28日星期三
diamond wheel advantages
1, with high cutting speed can be achieved with a high cutting speed can reach 100 100 - 300m / s 300m / s, and long service life.
2, using sintered diamond and boron nitride grinding wheel binder, binder for the multi-layer resin, metal and polishing pads for granite ceramic, using sintered diamond and boron nitride grinding wheel binder, binder for the multi-layer resin, metal, and ceramics, the maximum diameter of up to the maximum diameter of up to 600mm600mm; electroplated diamond and CBN grinding wheel method, the maximum diameter; electroplated diamond and CBN grinding wheel method, the maximum diameter of up to 1300mm.
3, the wheel of the mechanical strength of the substrate can withstand the high speed grinding cutting forces. High-speed grinding, safe and grinding the substrate can withstand the Plate Compactor high mechanical strength of the high cutting force during grinding. High-speed grinding, safety and reliability is extremely high.
4, the appearance of sharp, abrasive bump height, and that can accommodate a large number of long chips. Look sharp, abrasive bump height, and that can accommodate a large number of long chips.
5, high precision grinding, wear a long time, often without trimming, its accuracy can meet the wet tile saw requirements of precision plus high precision grinding, wear a long time, often without trimming, its accuracy can meet the requirements of precision machining needs, can be avoided taper workpiece machining process, excellent wear resistance characteristics can enable enterprises to work needs to avoid processing the workpiece taper, excellent wear resistance characteristics of the enterprise can greatly reduce production costs.
6, multiple binding agent has a high wear resistance, minimal wheel wear.
2, using sintered diamond and boron nitride grinding wheel binder, binder for the multi-layer resin, metal and polishing pads for granite ceramic, using sintered diamond and boron nitride grinding wheel binder, binder for the multi-layer resin, metal, and ceramics, the maximum diameter of up to the maximum diameter of up to 600mm600mm; electroplated diamond and CBN grinding wheel method, the maximum diameter; electroplated diamond and CBN grinding wheel method, the maximum diameter of up to 1300mm.
3, the wheel of the mechanical strength of the substrate can withstand the high speed grinding cutting forces. High-speed grinding, safe and grinding the substrate can withstand the Plate Compactor high mechanical strength of the high cutting force during grinding. High-speed grinding, safety and reliability is extremely high.
4, the appearance of sharp, abrasive bump height, and that can accommodate a large number of long chips. Look sharp, abrasive bump height, and that can accommodate a large number of long chips.
5, high precision grinding, wear a long time, often without trimming, its accuracy can meet the wet tile saw requirements of precision plus high precision grinding, wear a long time, often without trimming, its accuracy can meet the requirements of precision machining needs, can be avoided taper workpiece machining process, excellent wear resistance characteristics can enable enterprises to work needs to avoid processing the workpiece taper, excellent wear resistance characteristics of the enterprise can greatly reduce production costs.
6, multiple binding agent has a high wear resistance, minimal wheel wear.
Method for polishing a diamond tool
Single-crystal diamond tool manufacturing processes generally include material selection, orientation, sawing, cogging, installed cards, rough grinding, fine grinding and inspection. Will be masonry drill bits selected by the directional diamond original stone after sawing along the biggest open plane, get two tool blanks, so that both improve the utilization of diamond material, but also reduce the total amount of polishing. Blooming through the tool can shape up chucking (mosaic or brazing) requirements. Cogging and coarse, fine grinding polishing methods are used.
Diamond grinding disc for grinding of cast iron. Grinding disc diameter of about 300mm, organized by the 4 inch circular saw blade material pore shape, size and proportions of the diamond abrasive are optimized special high phosphorus cast iron. Grinding disc surface inlaid with diamond abrasive powder, the particle size can be from less than 1μm until 40μm. Rough diamond powder particles having a high polishing rate, but poor quality grinding, generally used so coarse meal, and is used when grinding the powder size of less than 1μm. Before grinding, first diamond powder with olive oil or other similar substances mixed into a grinding paste, and abrasive tools then coated on the surface of the grinding plate, place some time for the grinding disc grinding paste to fully penetrate the pores of the cast, and then a large diamond in pre-grinding disc surface grinding back and forth in order to further strengthen the diamond powder in the cast iron pores mosaic effect. Grinding, polishing the diamond will generally be embedded in a tin bucket, revealing only a surface to be polished.
Diamond grinding disc for grinding of cast iron. Grinding disc diameter of about 300mm, organized by the 4 inch circular saw blade material pore shape, size and proportions of the diamond abrasive are optimized special high phosphorus cast iron. Grinding disc surface inlaid with diamond abrasive powder, the particle size can be from less than 1μm until 40μm. Rough diamond powder particles having a high polishing rate, but poor quality grinding, generally used so coarse meal, and is used when grinding the powder size of less than 1μm. Before grinding, first diamond powder with olive oil or other similar substances mixed into a grinding paste, and abrasive tools then coated on the surface of the grinding plate, place some time for the grinding disc grinding paste to fully penetrate the pores of the cast, and then a large diamond in pre-grinding disc surface grinding back and forth in order to further strengthen the diamond powder in the cast iron pores mosaic effect. Grinding, polishing the diamond will generally be embedded in a tin bucket, revealing only a surface to be polished.
2013年8月27日星期二
The parameters of diamond cutter
The basic parameters of a diamond cutter. Taps familiar structure and geometry.
2. Learn two groups of diamond tool design.
3. To understand the 12 inch saw blade structure of the diamond tool types and their characteristics and applications
4. Learn broaching tap structure principle and applications.
5. Understand the working principle and extrusion tap main advantages
Understand the structure and use of die.
Learn thread cutter type and router bits application
Understand the structure and use of the die head.
Understanding of thread rolling tool (rolling wheel Example 11.1 What types of diamond tool? They all fit what the occasion, what types of processing threads? A: There are tools like thread cutter, cutter type, broaches classes and thread the press tool. Thread turning lathe suitable for 6I
Workers and taper internal and external threads; cutter type suitable for use in milling machining cylindrical external thread; pull knives suitable for manual and village
Dynamic processing thread; thread tool suitable for processing the pressure strength, high hole saw blades hardness plastic material Lo mosquito.
2. Learn two groups of diamond tool design.
3. To understand the 12 inch saw blade structure of the diamond tool types and their characteristics and applications
4. Learn broaching tap structure principle and applications.
5. Understand the working principle and extrusion tap main advantages
Understand the structure and use of die.
Learn thread cutter type and router bits application
Understand the structure and use of the die head.
Understanding of thread rolling tool (rolling wheel Example 11.1 What types of diamond tool? They all fit what the occasion, what types of processing threads? A: There are tools like thread cutter, cutter type, broaches classes and thread the press tool. Thread turning lathe suitable for 6I
Workers and taper internal and external threads; cutter type suitable for use in milling machining cylindrical external thread; pull knives suitable for manual and village
Dynamic processing thread; thread tool suitable for processing the pressure strength, high hole saw blades hardness plastic material Lo mosquito.
diamond tool design drawings
Therefore, the preparation of diamond tools required plan the most important and critical work is to determine the amount of diamond tools required to prepare plans required diamond tool, diamond tools and production departments, technical departments cooperate, master construction technology, construction technology to understand organizational scheme wood drill bits carefully read construction drawings; production operations plan issued under the workload, combined with drawings and construction program, construction of physical quantities calculated; Zha diamond tool consumption quota, calculate the amount of material needed for the production, complete quantity analysis; project quantity will be divided analysis of different varieties and specifications, the number of diamond tools required to be aggregated amount.(A) calculate the amount of diamond tools required.1) Plan period works diamond tools required dosage calculations. Plan period works diamond tool can be used directly to calculate the necessary amount of indirect calculation method and the two methods of calculation.① direct calculation.Direct calculation unit works generally prepared for the object. In the construction drawings arrive and after triage, according to sub-part construction plans sds hammer drill bits calculating physical quantities, combined with the construction programs and measures to apply the appropriate preparation of diamond tools diamond tools analyze consumption of fixed tables summarize by segment, diamond tool unit project preparation required plans, or according to the construction site requirements and the image of progress, the preparation quarter, month required plan. direct calculation formula is as follows:A diamond cutter program will be the amount of two physical quantities x construction and installation of a diamond tool consumption quota formula "Material Consumption," according to a fixed object divided into construction and (there is) a fixed budget. If the internal preparation of construction work plan, project contracting to the unit and the concrete ring saw team responsible for the implementation of a given package supply of materials, as contracting basis of accounting should be used to calculate the material construction quota amount required. Such as the preparation of construction drawing budget to the construction unit, the higher authorities and the planned distribution of material goods departments to apply indicators as the basis for settlement or according to the preparation orders, procurement plan, should be used (none) budget fixed amount of computational materials required.
2013年8月26日星期一
Cutting Tool familiar method
1.1 Cutting Tool Category
1. Familiar molding Gear cutters (shaped gear cutter,
2. Master generating method processing principle.
3. Common understanding of the industrial saw blades gear generating method machining tool *
12.1.2 gear cutter
Explicitly set for each gear cutter blade No. tooth design principles.
Can be processed according to the number of gear teeth and the correct choice of milling cutter mold number.
Master machining helical gears and straight bevel gear cutter selection method.
1.3 shaper cutters
1. Master cutter works.
2. Learn the basic parameters of cutter, arbitrary profile parameter, the cutting angle.
3. Learn enclosed cutter precision grade and wet polishing pad reasonable selection [type selection, the choice of school type
12.14 Hob
1. Master gear hob works.
2 Understanding three kinds Tan knife Spade tooth worm theory, error, application.
3. Archimedes worm understand the diamond tool manufacturer structural parameters of the cutter (hob cutting parameters
: The number of liquid knife accuracy class).
4. Learn Archimedes worm hob selection of the structural parameters.
5. Chun master knife installation and adjustment methods.
12.1.5 worm hob with knife
1. Learn worm hob works,
2. Grasp the structural characteristics of worm hob.
3. Flying to understand the characteristics of the worm gear.
1. Familiar molding Gear cutters (shaped gear cutter,
2. Master generating method processing principle.
3. Common understanding of the industrial saw blades gear generating method machining tool *
12.1.2 gear cutter
Explicitly set for each gear cutter blade No. tooth design principles.
Can be processed according to the number of gear teeth and the correct choice of milling cutter mold number.
Master machining helical gears and straight bevel gear cutter selection method.
1.3 shaper cutters
1. Master cutter works.
2. Learn the basic parameters of cutter, arbitrary profile parameter, the cutting angle.
3. Learn enclosed cutter precision grade and wet polishing pad reasonable selection [type selection, the choice of school type
12.14 Hob
1. Master gear hob works.
2 Understanding three kinds Tan knife Spade tooth worm theory, error, application.
3. Archimedes worm understand the diamond tool manufacturer structural parameters of the cutter (hob cutting parameters
: The number of liquid knife accuracy class).
4. Learn Archimedes worm hob selection of the structural parameters.
5. Chun master knife installation and adjustment methods.
12.1.5 worm hob with knife
1. Learn worm hob works,
2. Grasp the structural characteristics of worm hob.
3. Flying to understand the characteristics of the worm gear.
diamond cutter in the mold manufacturing potential
Modern mold manufacturing and machining tools used in the rapid development of technology, high-tech has been widely adopted in the Diamond tool process, cutting mode, tool construction, tool material, tool coating, etc. have been great with the traditional machining different points. New tool having a novel structure and geometry of the cutting edge and the blade is out of continuous research and development, adaptation and high speed CNC machining to the machine tool clamping and connecting member such as HSK tool holders, thermal sleeve shank, hydraulic as well as other new shank tool holders and other widely available. In order to improve production efficiency and reduce tool change time in the mold parts processing in the cutting discs increasing use of a variety of complex tools, such as drill boring composite, composite hinge drilling, drilling and thread processing complexes and other types of composite tools, complex structures The expansion tool to meet a lot of special processing requirements, and some even developed into a machine tool, electrical and hydraulic integrated device, has been far beyond the traditional concept of the tool.
Selected by the user in the domestic mold tool materials, the use of carbide cutting tools is the largest, accounting for 64.1%. The development of superhard cutting tool, as an alternative to hard turning positive economic and good grinding method in popularity. Superhard cutting tool usage has been significantly improved, such as the processing of the cylinder block cylinder bore in the semi-fine boring and grinding cup wheels fine boring process a lot on the use of cubic boron nitride blade, cutting speed has reached a new height, and extended tool life. Indexable tool in our marketing has been for many years, progressed smoothly, but the development is still unbalanced, the user is still lower than the overall coverage of tools and soldering tools. However, China indexable cutting tool technology in the promotion process has been new progress, a great variety of potential applications has increased rapidly.
Selected by the user in the domestic mold tool materials, the use of carbide cutting tools is the largest, accounting for 64.1%. The development of superhard cutting tool, as an alternative to hard turning positive economic and good grinding method in popularity. Superhard cutting tool usage has been significantly improved, such as the processing of the cylinder block cylinder bore in the semi-fine boring and grinding cup wheels fine boring process a lot on the use of cubic boron nitride blade, cutting speed has reached a new height, and extended tool life. Indexable tool in our marketing has been for many years, progressed smoothly, but the development is still unbalanced, the user is still lower than the overall coverage of tools and soldering tools. However, China indexable cutting tool technology in the promotion process has been new progress, a great variety of potential applications has increased rapidly.
2013年8月25日星期日
Granite radioactive higher household interior decoration
should be used with cautionDecoration Safety
Painted ventilation after release formaldehyde toxicity of coatings and paints mainly formaldehyde, benzene and diamond cup wheels other carcinogens, as well as lead, mercury,Cadmium and other harmful substances. Especially formaldehyde would cause serious damage to the respiratory system, primarily released from fine wood panels, paintedMaterials and paints are also present in small amounts. In addition, the interior paint of waterborne coatings and solvent-based paints are two pollutantsMainly solvent-based coatings, environmentally friendly water-based paint can be assured.
Done with caution granite interior
Stone hard, colorful, decorative effect, is used in flooring, windows and other places. Experts, ordinary peopleConcern over radioactive stone, in fact, do not "scared", no stone is radioactive, and some on the human body did notThere are hazards can be avoided as long as selected species.
Meanwhile, experts also remind, is mainly used for decorative stone marble, granite, from the national technical cutting tools supervision departmentsSampling results from around the stone, marble basically qualified radiological examination results, and peace of mind; but put graniteShot higher, exceeding more categories.
It is understood that after the granite of radium radon gas produced --- If the body has long been attracted to accumulate, it will raiseHigh incidence of lung cancer.
Note ceiling flame flammable materials
A public consultation stage to say, home ceiling dark tank electrical short circuit, kindled a fire, the ceiling is difficult to extinguishFire, wood trim board is also flammable, almost led to disaster. Decoration Precautions
1. Coatings and paints toxicity is mainly formaldehyde, benzene and other carcinogens, as well as lead, mercury, cadmium and other harmful substances. Therefore, Brushing paint must be ventilated after release.
2. Any stone has radioactive, and some 9 inch saw blade did not harm the human body, as long as you can avoid selecting species.
3. Try not flammable, combustible materials, decoration; if it is to use, fire-retardant treatment must be done.
Household Fire Knowledge
Find the home gas leak, do not immediately call house phone, turn lights, etc., but should immediately turn off the main gas valveOpen the doors and windows ventilation.
Painted ventilation after release formaldehyde toxicity of coatings and paints mainly formaldehyde, benzene and diamond cup wheels other carcinogens, as well as lead, mercury,Cadmium and other harmful substances. Especially formaldehyde would cause serious damage to the respiratory system, primarily released from fine wood panels, paintedMaterials and paints are also present in small amounts. In addition, the interior paint of waterborne coatings and solvent-based paints are two pollutantsMainly solvent-based coatings, environmentally friendly water-based paint can be assured.
Done with caution granite interior
Stone hard, colorful, decorative effect, is used in flooring, windows and other places. Experts, ordinary peopleConcern over radioactive stone, in fact, do not "scared", no stone is radioactive, and some on the human body did notThere are hazards can be avoided as long as selected species.
Meanwhile, experts also remind, is mainly used for decorative stone marble, granite, from the national technical cutting tools supervision departmentsSampling results from around the stone, marble basically qualified radiological examination results, and peace of mind; but put graniteShot higher, exceeding more categories.
It is understood that after the granite of radium radon gas produced --- If the body has long been attracted to accumulate, it will raiseHigh incidence of lung cancer.
Note ceiling flame flammable materials
A public consultation stage to say, home ceiling dark tank electrical short circuit, kindled a fire, the ceiling is difficult to extinguishFire, wood trim board is also flammable, almost led to disaster. Decoration Precautions
1. Coatings and paints toxicity is mainly formaldehyde, benzene and other carcinogens, as well as lead, mercury, cadmium and other harmful substances. Therefore, Brushing paint must be ventilated after release.
2. Any stone has radioactive, and some 9 inch saw blade did not harm the human body, as long as you can avoid selecting species.
3. Try not flammable, combustible materials, decoration; if it is to use, fire-retardant treatment must be done.
Household Fire Knowledge
Find the home gas leak, do not immediately call house phone, turn lights, etc., but should immediately turn off the main gas valveOpen the doors and windows ventilation.
marble countertops and marble identifying strengths
marble countertops and marble identifying strengths and weaknesses and maintenance methodsMarble countertops cabinets with its natural texture atmospheric grace recognized by the edge polishing pads high-end market, but there are many consumersBecause marble radiation and identification methods and hesitant, after reading this article these problems will be solved.
Marble, also known as marble is recrystallized limestone, the main component is CaCO3. Limestone softened under heat and pressure,And changes in the minerals contained in re-crystallization of marble. Mainly used for processing into various shaped timber, lumber, for the construction ofBuildings, walls and floor, table, column, also commonly used in monuments such as the monument, tower, statues and other materials.
Marble produced in Yunnan Province, Dali originally referred to the white limestone with black patterns, profiles can form a naturalLandscape painting, often selected with ancient marble pattern molded concrete grinding wheel painted screen or used to make mosaics, marble table laterSurface called the name evolved into a variety of colors all patterns, used to make decorative building materials limestone, whiteWhite marble marble generally known, but the translation of Western statue made of white marble is also known as marble.
Marble countertops identification method:
Good product for the processing finishes marble countertops, its quality can be used to identify the following four aspects: a concept,Visually observed that the surface structure of the stone. In general, uniform fine structure of the stone material with a delicate texture, for the stoneTo share; ranging from coarse grain structure of the stone and its appearance is poor. In addition, the stone due to the impact of geological processes oftenWhich have some minor cracks, stone most likely to rupture along these areas, attention should be excluded. As for the lack of shadow edges isRing appearance, particular attention should be selected. Two volume, the amount of stone sizes, to affect splicing, or cause splicingDesigns, patterns, lines, deformation, decorative effect. Three, that is to listen stone percussion sounds.
China cabinets, editor remind you of good quality stone its clear crisp percussion; contrary, if there is light stone interiorMicrocracks or indirect result of weathering causes particles thixotropic loose, percussion gruff. Four test, which uses a simple test method to testThe quality of the stone. Usually drops on the back a stone pellets ink, such as ink quickly disperse leaching, which indicatesLoose particles inside the stone or the existence of gaps, poor quality stone; Conversely, if the ceramic tile saw ink droplets in place does not move, then the stoneGood texture.
The marble countertops and stone features and benefits:
1 is not deformed, high hardness, wear resistance. The long-term natural aging rock, organizational structure of uniform, small linear expansion coefficient, Internal stress completely disappeared, no deformation. Afraid of acid, alkaline liquid material erosion, will not rust, do not oiled, easy to stick dust,Maintenance, convenient and simple maintenance, long service life.
(2) abrasion resistant, high temperature resistant, maintenance-free. Good rigidity, high hardness, wear resistance, and temperature deformation. Plan does not appearMarks, not constant temperature conditions to prevent, at room temperature, can maintain their original physical properties.
3. Physical stability, careful organization, by the impact grain off the surface edges can not afford, do not affect the accuracy of its plane, timberQuality and stability, to ensure long-term deformation, linear expansion coefficient, high precision machinery, anti-rust, anti-magnetic, insulation. Not magnetizationMeasurements can move smoothly, without Zhise sense, unaffected by moisture, plane weighed good.
Marble, also known as marble is recrystallized limestone, the main component is CaCO3. Limestone softened under heat and pressure,And changes in the minerals contained in re-crystallization of marble. Mainly used for processing into various shaped timber, lumber, for the construction ofBuildings, walls and floor, table, column, also commonly used in monuments such as the monument, tower, statues and other materials.
Marble produced in Yunnan Province, Dali originally referred to the white limestone with black patterns, profiles can form a naturalLandscape painting, often selected with ancient marble pattern molded concrete grinding wheel painted screen or used to make mosaics, marble table laterSurface called the name evolved into a variety of colors all patterns, used to make decorative building materials limestone, whiteWhite marble marble generally known, but the translation of Western statue made of white marble is also known as marble.
Marble countertops identification method:
Good product for the processing finishes marble countertops, its quality can be used to identify the following four aspects: a concept,Visually observed that the surface structure of the stone. In general, uniform fine structure of the stone material with a delicate texture, for the stoneTo share; ranging from coarse grain structure of the stone and its appearance is poor. In addition, the stone due to the impact of geological processes oftenWhich have some minor cracks, stone most likely to rupture along these areas, attention should be excluded. As for the lack of shadow edges isRing appearance, particular attention should be selected. Two volume, the amount of stone sizes, to affect splicing, or cause splicingDesigns, patterns, lines, deformation, decorative effect. Three, that is to listen stone percussion sounds.
China cabinets, editor remind you of good quality stone its clear crisp percussion; contrary, if there is light stone interiorMicrocracks or indirect result of weathering causes particles thixotropic loose, percussion gruff. Four test, which uses a simple test method to testThe quality of the stone. Usually drops on the back a stone pellets ink, such as ink quickly disperse leaching, which indicatesLoose particles inside the stone or the existence of gaps, poor quality stone; Conversely, if the ceramic tile saw ink droplets in place does not move, then the stoneGood texture.
The marble countertops and stone features and benefits:
1 is not deformed, high hardness, wear resistance. The long-term natural aging rock, organizational structure of uniform, small linear expansion coefficient, Internal stress completely disappeared, no deformation. Afraid of acid, alkaline liquid material erosion, will not rust, do not oiled, easy to stick dust,Maintenance, convenient and simple maintenance, long service life.
(2) abrasion resistant, high temperature resistant, maintenance-free. Good rigidity, high hardness, wear resistance, and temperature deformation. Plan does not appearMarks, not constant temperature conditions to prevent, at room temperature, can maintain their original physical properties.
3. Physical stability, careful organization, by the impact grain off the surface edges can not afford, do not affect the accuracy of its plane, timberQuality and stability, to ensure long-term deformation, linear expansion coefficient, high precision machinery, anti-rust, anti-magnetic, insulation. Not magnetizationMeasurements can move smoothly, without Zhise sense, unaffected by moisture, plane weighed good.
2013年8月23日星期五
steel circular saw blades
In the use of high-speed hacksaw for cutting all kinds of pipes, there are many situations because there is no attention to detail caused.
1, Material: sometimes the bandsaw blades problem is with the material to be cut, because there are too many materials purchased impurities, so when the blade hit these impurities particles, super-hard blade may break or give great sound, cut out The surface will be uneven. But with softer HSS saw blade can not break, but the results will be skewed cutting phenomenon, because the blade when in contact with particles shift phenomenon.
2, the blade: blade did not properly gracefully compressive deformation, serrated blunt out no grinding, yaw rate deviation, number of teeth inappropriate choice of saw blade strength is not correct, choose the wrong blade, blade quality is poor.
3, cutting machine: state of the fixture, the blade filled with incorrect rotation number is not correct, not cutting speed, cutting oil selection, and the saw blade and cutting machine error may be due to influence each other. When guests complain about cutting results skewed to the site via our observations, feeding rack not fixed, the plant personnel to transport material, often careless collision crooked away, was cut off crooked timber feeding rack after, of course, must be cut out of material crooked. Customer complaints are also often broken saw blade can not be solved, we got to the scene found the book of mechanical design has been pointed out that the longer the cutting material, must have been cut by Taiwan to make the segments are not shaking. However, the customer still and chopped material as well, so the blade will have to be cut by shaking timber crashed. There is also the customer's machine is not in the installed horizontally correction, so the wet polishing pad machine was fundamentally crooked.
4, the use of counterfeit machine: Because most of the cost of the machine in the mechanical materials, machine parts cheap that the use of cheap, of course, there is no guarantee of quality. Therefore, there may be insufficient because of mechanical stability undue impact or shaking.
5, manual machine (operator): Since the machine is manually operated manually, sometimes the operator under the knife under the knife too hard or too fast, it may cause blade breakage.
Blade must be used note the following:
One must determine the cut material has indeed fixed.
2, according to the stone drill bits material to be cut off condition set.
3, filled with saw, must be part of the jig clean out debris, and then pay attention to the direction of rotation, the blade is firmly seated.
4, at the beginning and stop cutting cutting, do not feed too fast, it may cause broken teeth and damaged.
5, full use of cutting oil (I hope with Workpiece selection cutting oil).
6, Disposable circular saw blade circular saw blade cutting machines and cutting machines generally different, we must choose the correct blade, can not be mixed.
1, Material: sometimes the bandsaw blades problem is with the material to be cut, because there are too many materials purchased impurities, so when the blade hit these impurities particles, super-hard blade may break or give great sound, cut out The surface will be uneven. But with softer HSS saw blade can not break, but the results will be skewed cutting phenomenon, because the blade when in contact with particles shift phenomenon.
2, the blade: blade did not properly gracefully compressive deformation, serrated blunt out no grinding, yaw rate deviation, number of teeth inappropriate choice of saw blade strength is not correct, choose the wrong blade, blade quality is poor.
3, cutting machine: state of the fixture, the blade filled with incorrect rotation number is not correct, not cutting speed, cutting oil selection, and the saw blade and cutting machine error may be due to influence each other. When guests complain about cutting results skewed to the site via our observations, feeding rack not fixed, the plant personnel to transport material, often careless collision crooked away, was cut off crooked timber feeding rack after, of course, must be cut out of material crooked. Customer complaints are also often broken saw blade can not be solved, we got to the scene found the book of mechanical design has been pointed out that the longer the cutting material, must have been cut by Taiwan to make the segments are not shaking. However, the customer still and chopped material as well, so the blade will have to be cut by shaking timber crashed. There is also the customer's machine is not in the installed horizontally correction, so the wet polishing pad machine was fundamentally crooked.
4, the use of counterfeit machine: Because most of the cost of the machine in the mechanical materials, machine parts cheap that the use of cheap, of course, there is no guarantee of quality. Therefore, there may be insufficient because of mechanical stability undue impact or shaking.
5, manual machine (operator): Since the machine is manually operated manually, sometimes the operator under the knife under the knife too hard or too fast, it may cause blade breakage.
Blade must be used note the following:
One must determine the cut material has indeed fixed.
2, according to the stone drill bits material to be cut off condition set.
3, filled with saw, must be part of the jig clean out debris, and then pay attention to the direction of rotation, the blade is firmly seated.
4, at the beginning and stop cutting cutting, do not feed too fast, it may cause broken teeth and damaged.
5, full use of cutting oil (I hope with Workpiece selection cutting oil).
6, Disposable circular saw blade circular saw blade cutting machines and cutting machines generally different, we must choose the correct blade, can not be mixed.
binding site of the substrate
Cause: The cut material is very resistant, cutting debris mixed in the cut seam can not be discharged.
Workaround: Use the special metal grinding wheel position of the substrate to protect the teeth, use a larger flow of cooling water pressure can enhance chip evacuation.
2 heads uneven wear on both sides
Cause: The blade tilt cutting; water is not the same on both sides, one side water shortage.
Solution: Check the blade tilt situation; Check the cooling water system.
3 out of round blade
Cause: The shaft wear cause the blade to a larger center hole and spindle clearance or not installed correctly.
Solution: replace or repair worn shaft center hole.
4 blade deflection
Cause: The material to be cut debris mixed in the crevices cut discontinuity caused by the body evenly; flange diameter is too small or both sides of the flange diameter is inconsistent; blade with flange mixed between a foreign body; not installed correctly.
Solution: clean up debris, and enhance chip evacuation; adjust or replace flange; follow the instructions to install correctly.
5 blade breakage
Cause: The head binders too hard; blade feeding speed is too fast.
Solution: According to the choice of materials to be cut with the blade softer binders; reduce the feed rate of the blade.
6 heads excessive wear and tear
Cause: The blade is too soft binder (for cut material); cooling water shortage; Since the drive belt loose or low voltage caused or inappropriate speed is insufficient power; saw blade is not perpendicular to the material being cut.
Workaround: Depending on choice of materials to be cut using a hard binder blade; Check the wet saw blades cooling water system to ensure the normal operation of the pump; ensure that the supply voltage; checking the spindle flange, saw blades and equipment to ensure verticality; checking the speed of the blade .
7 heads being lost
Reason: In the process of cutting material to be cut off by sliding head twisted; make heads been hit; flange wear can not be fixed blade, causing the blade twist; spindle wear and tear caused by the blade circular saw blade failure compared big impact; overheating; blade under severe attacks.
Workaround: firmly fixed to be cut when cutting materials; replace both sides of the flange; replace worn spindle; Check the cooling water; mobile devices Avoid bumping or cutting blade materials.
8 blunt, not cutting
Reason: Saw binders too hard; underpowered does not enable normal cutting blade, the blade cut is not applied enough pressure; blade wire speed is too high.
Solution: choose to use ring saw blades a softer binder blade; checking belts, voltage and motor; determine and but big enough and the cut-in pressure; according to instructions of the device used to match the diameter of the corresponding blade.
Workaround: Use the special metal grinding wheel position of the substrate to protect the teeth, use a larger flow of cooling water pressure can enhance chip evacuation.
2 heads uneven wear on both sides
Cause: The blade tilt cutting; water is not the same on both sides, one side water shortage.
Solution: Check the blade tilt situation; Check the cooling water system.
3 out of round blade
Cause: The shaft wear cause the blade to a larger center hole and spindle clearance or not installed correctly.
Solution: replace or repair worn shaft center hole.
4 blade deflection
Cause: The material to be cut debris mixed in the crevices cut discontinuity caused by the body evenly; flange diameter is too small or both sides of the flange diameter is inconsistent; blade with flange mixed between a foreign body; not installed correctly.
Solution: clean up debris, and enhance chip evacuation; adjust or replace flange; follow the instructions to install correctly.
5 blade breakage
Cause: The head binders too hard; blade feeding speed is too fast.
Solution: According to the choice of materials to be cut with the blade softer binders; reduce the feed rate of the blade.
6 heads excessive wear and tear
Cause: The blade is too soft binder (for cut material); cooling water shortage; Since the drive belt loose or low voltage caused or inappropriate speed is insufficient power; saw blade is not perpendicular to the material being cut.
Workaround: Depending on choice of materials to be cut using a hard binder blade; Check the wet saw blades cooling water system to ensure the normal operation of the pump; ensure that the supply voltage; checking the spindle flange, saw blades and equipment to ensure verticality; checking the speed of the blade .
7 heads being lost
Reason: In the process of cutting material to be cut off by sliding head twisted; make heads been hit; flange wear can not be fixed blade, causing the blade twist; spindle wear and tear caused by the blade circular saw blade failure compared big impact; overheating; blade under severe attacks.
Workaround: firmly fixed to be cut when cutting materials; replace both sides of the flange; replace worn spindle; Check the cooling water; mobile devices Avoid bumping or cutting blade materials.
8 blunt, not cutting
Reason: Saw binders too hard; underpowered does not enable normal cutting blade, the blade cut is not applied enough pressure; blade wire speed is too high.
Solution: choose to use ring saw blades a softer binder blade; checking belts, voltage and motor; determine and but big enough and the cut-in pressure; according to instructions of the device used to match the diameter of the corresponding blade.
2013年8月22日星期四
metal clothing diamond - Plating
By using the plating coat diamond (nickel, nickel thorn, electroless nickel plating), abrasive grains can increase the viscosity of the resin bonding materialResults fastness, resin-bonded material that is the wettability of the diamond because of the diamond hole saw presence of the metal is improved, the diamond grindingBetween the particles and the binder tightly, no gap exists, effectively improve the resin diamond grit holding force. While increasingAdded a diamond grinding process in highly exposed, so not only can extend every one present in the cutting surface of the grinding wheelGrains of life, but also improves the efficiency of the grinding wheel. Abrasive surface of the metal plating coat Another advantage is to 4 inch saw blades produce grindingAbrasive cut through the first heat transfer to the surface of the metal, clothing, clothes because of the metal poor thermal conductivity than diamond, and thus grinding heat in goldAccumulation is somewhat clothes, and then through the cooling fluid or the flow of air in order to play the role of a thermal barrier. Known, diamondThermal conductivity than copper, nickel and other metals. When the workpiece grinding wheel grinding heat generated by the abrasive cutting-edge guide to the surrounding body through gritThe binding agent, the non-diamond plating around the ring saw blades heat accumulation compared to metal-plated clothing, temperature rises quickly, the conduction to theResin rapid accumulation of heat, the temperature increase. When the heat-resistant strength than the resin, the resin is damaged, the abrasive from junctionMixture off. When the diamond abrasive grains coated with a metal jacket, the abrasive tip of the moving blade, the heat conduction away correspondingly protectedAbrasive binder resin is not around or less subject to thermal damage.
diamond crystal --- CBN
Hardness and wear resistance: Diamond is saturated and having a directivity combine covalently crystal, it has a veryHigh hardness and wear resistance, is the hardest known diamond wire saw substance in nature.Application:
A mechanical processing industry
Diamond abrasive effects are grinding carbide tools. Sharpening carbide turning, every mill in addition to the metal needs to consume 1g GCAbrasive 4-15g, while the diamond consuming only 2-4mg.
2 Electronics Industry
Precious hard and brittle semiconductor materials such as silicon, germanium, gallium arsenide, etc. For small pieces made of a semiconductor device, to be cutAnd grinding. The table saw blades most appropriate method using a diamond cutting blade machining. With diamond paste polishing a semiconductor materialMaterial, not only efficient, but also can achieve the highest level of surface roughness Ra0.006um.
3 optical glass and stones processing industry
Before the use of silicon carbide processing optical glass, low efficiency, poor working conditions. Now all using diamond abrasive machiningIncluding cutting, nesting, cutting, milling and convex and concave surface grinding.
4 drilling and mining industry
In the oil, coal, metallurgy, geology exploration drilling and exploitation, extensive use of diamond drill bits.
5 construction and tct circular saw blade building materials industry
Marble, granite, artificial cast stone, concrete building materials, cutting and grinding, the extensive use of goldDiamond tool.Specifications are cylindrical, triangular, rectangular, cube and other series.
A mechanical processing industry
Diamond abrasive effects are grinding carbide tools. Sharpening carbide turning, every mill in addition to the metal needs to consume 1g GCAbrasive 4-15g, while the diamond consuming only 2-4mg.
2 Electronics Industry
Precious hard and brittle semiconductor materials such as silicon, germanium, gallium arsenide, etc. For small pieces made of a semiconductor device, to be cutAnd grinding. The table saw blades most appropriate method using a diamond cutting blade machining. With diamond paste polishing a semiconductor materialMaterial, not only efficient, but also can achieve the highest level of surface roughness Ra0.006um.
3 optical glass and stones processing industry
Before the use of silicon carbide processing optical glass, low efficiency, poor working conditions. Now all using diamond abrasive machiningIncluding cutting, nesting, cutting, milling and convex and concave surface grinding.
4 drilling and mining industry
In the oil, coal, metallurgy, geology exploration drilling and exploitation, extensive use of diamond drill bits.
5 construction and tct circular saw blade building materials industry
Marble, granite, artificial cast stone, concrete building materials, cutting and grinding, the extensive use of goldDiamond tool.Specifications are cylindrical, triangular, rectangular, cube and other series.
2013年8月19日星期一
curved blade, shaped blade
With extremely good wear resistance and impact resistance. For processing all types of non-ferrous metals concrete saws and non-ferrous metals, depending on theProcessing conditions to select different grades of diamond tungsten steel, high-speed light cutting tool has superior performance pan withGood. After coating with excellent results, can improve tool life and abrasion resistance, commonly used in CNC machine tools CNC equipment and generalProcessing all kinds of copper, aluminum, high-temperature alloys, heat-resistant alloys, titanium alloys, gray cast brick saw blades iron, hard quenched steel, tool steel, stainless steelAnd non-ferrous materials such as acrylic materials, PCB, fiber, carbon fiber, plastic, wood, etc., is quenched before the heat treatment, andAfter extremely fine machining tool.High hardness and wear resistant senior high cobalt powder steel cutter: with extremely good wear abrasive tools resistance and impact resistance, good technology,Generally used for high-speed light cutting, cutting all kinds of difficult to machine materials. After coating better, excellent tool life, wearExtremely high.
CBN inserts, ceramic inserts
PCD tool: suitable for cutting non-ferrous metals and a variety of non-metallic, carbide than natural diamond cutting tools and high efficiencyAnd low-cost, widely used in automotive, diesel, motorcycle, aerospace, appliance, apparatus, precision machinery and other diamond wire saw industriesPiston, cylinder liner .. wheels, bearings, armature, electrodes, cabinet, laminate flooring and so on. Machinable aluminum and aluminum alloy, copper andCopper alloy, wood and a variety of base fiber materials, stone, carbide and so the field for finishing, super finishing.CBN tools: particularly suitable for a variety of black metal hard cutting, to achieve a car instead of grinding. Pulling only improve processing efficiency, andSignificantly reduce processing costs, mainly cutting a variety of hardened steel, tool steel, tool steel, bearing steel (HRC45-70),Chilled cast iron, high Plate Compactor chromium cast iron, Ni-base superalloy base and CO, a variety of difficult machining gray cast iron. Turning plus main application areasEngineering, milling, drilling.
Ultra micro-grain diamond tungsten steel cutting tools: with extremely good wear resistance and impact resistance. Suitable for processing various types of non-ferrous metalsAnd non-ferrous metals, depending on the processing conditions, to select different grades of diamond tungsten steel, high speed light cutting on the toolWith superior performance, generic good. After coating with excellent results, can improve tool life and abrasion resistance, commonlyIn general of CNC machining equipment and turbo diamond blade all kinds of copper, aluminum, high-temperature alloys, heat-resistant alloys, titanium alloys, gray cast iron,Hard quench steel, tool steel, stainless steel and other materials and non-ferrous materials acrylic, PCB, optical fibers, carbon fibers, plastics, etc.,Is quenched before and after heat treatment of extremely fine machining tool.High hardness and wear resistant senior high cobalt powder steel cutter: with extremely good wear resistance and impact resistance, good technology,Generally used for high-speed light cutting, cutting all kinds of difficult to machine materials. After coating better, excellent tool life, wear Highly
Ultra micro-grain diamond tungsten steel cutting tools: with extremely good wear resistance and impact resistance. Suitable for processing various types of non-ferrous metalsAnd non-ferrous metals, depending on the processing conditions, to select different grades of diamond tungsten steel, high speed light cutting on the toolWith superior performance, generic good. After coating with excellent results, can improve tool life and abrasion resistance, commonlyIn general of CNC machining equipment and turbo diamond blade all kinds of copper, aluminum, high-temperature alloys, heat-resistant alloys, titanium alloys, gray cast iron,Hard quench steel, tool steel, stainless steel and other materials and non-ferrous materials acrylic, PCB, optical fibers, carbon fibers, plastics, etc.,Is quenched before and after heat treatment of extremely fine machining tool.High hardness and wear resistant senior high cobalt powder steel cutter: with extremely good wear resistance and impact resistance, good technology,Generally used for high-speed light cutting, cutting all kinds of difficult to machine materials. After coating better, excellent tool life, wear Highly
2013年8月18日星期日
diamond tool can process high hardness work
High hardness of diamond tool can process work:
PCD, PCBN two kinds of superhard material tools covering most machinable materials with high hardness cutting fields. PCD tool allows the surface roughness of Ra1.6-Ra0.16; PCBN cutting tool surface roughness can reach Ra1.6-Ra0.3. Machining, especially metal cutting process many occasions to turning, boring, milling instead of grinding process, so that the power trowel product parts simplify the structure, size, high precision, shape and position error is small, the production efficiency. Since turning, boring, milling cutter with compression of the carbide drill bits workpiece to be machined parts of the surface compressive stress after processing was like, help to improve the quality of product parts.
Dimensionally stable parts to be processed:
As superhard material tools high wear resistance, its life is much higher than carbide tools, parts to be machined dimensional stability, low cost production site quality management. Small pieces, a large number of the production process, tooling parts superhard material process capability index is high and stable, can greatly reduce the sampling frequency. Large small batch production process, large parts of the finished surface size consistency, shape, small error, can reduce the test items. Products, defective products, inspection fees are decreased substantially.
Comprehensive economic efficiency:
1, due to the frequency and masonry drill bits duration to reduce downtime, increase production throughput, decrease the number of waste products.
2, the use of equipment, electricity, labor costs and lower management fees.
3, PCBN and PCD tools in a suitable occasion, simply use the appropriate one-piece machining products are generally lower than the total cost of additional tooling costs.
PCD, PCBN two kinds of superhard material tools covering most machinable materials with high hardness cutting fields. PCD tool allows the surface roughness of Ra1.6-Ra0.16; PCBN cutting tool surface roughness can reach Ra1.6-Ra0.3. Machining, especially metal cutting process many occasions to turning, boring, milling instead of grinding process, so that the power trowel product parts simplify the structure, size, high precision, shape and position error is small, the production efficiency. Since turning, boring, milling cutter with compression of the carbide drill bits workpiece to be machined parts of the surface compressive stress after processing was like, help to improve the quality of product parts.
Dimensionally stable parts to be processed:
As superhard material tools high wear resistance, its life is much higher than carbide tools, parts to be machined dimensional stability, low cost production site quality management. Small pieces, a large number of the production process, tooling parts superhard material process capability index is high and stable, can greatly reduce the sampling frequency. Large small batch production process, large parts of the finished surface size consistency, shape, small error, can reduce the test items. Products, defective products, inspection fees are decreased substantially.
Comprehensive economic efficiency:
1, due to the frequency and masonry drill bits duration to reduce downtime, increase production throughput, decrease the number of waste products.
2, the use of equipment, electricity, labor costs and lower management fees.
3, PCBN and PCD tools in a suitable occasion, simply use the appropriate one-piece machining products are generally lower than the total cost of additional tooling costs.
diamond tool on the part of the surface roughness of
Diamond tool in the machining of stainless steel, the cutting force of the diamond, the shank must have sufficient strength and rigidity, in order to avoid chatter occurs during the tile cutting blades cutting and deformation processing of stainless steel, diamond tool cutting portion geometry, generally should rake angle, clearance angle, the options to consider. In the choice of the anterior horn, consider the volume crumbs groove, without chamfering and edge inclination angle of the sign size and other factors. Regardless of the tool, machining stainless steel must use a larger rake angle. Increasing the rake angle of the tool can be reduced, and cleared from the chip during the cutting resistance encountered. Right rear corner selection requirements are not very strict, but not too small, after the angle is too small and the surface is easy to cause serious friction, so that surface roughness deterioration accelerated tool wear. And due to strong friction and enhancing the effect of hardening the surface of stainless steel; tool clearance angle is not too large, after the angle is too large, the tool of the wedge angle decreases, reducing the strength of the cutting edge, accelerated wear of the tool. Typically, the posterior horn should be higher than ordinary carbon steel processed appropriately larger.
Diamond tool cutting part of the tool surface roughness requirements
Improve the surface finish of the cutting part of the tool can reduce the formation of diamond chips curled resistance, improved durability of the tool. Compared with the processing of ordinary carbon steel, stainless steel processing should be appropriately reduced to slow the cutting tool wear; also select the proper coolant in order to reduce the cutting process of cutting heat 14 inch saw blade and cutting force, extend tool life.
Material requirements for Arbor
Stainless steels, the cutting force of the diamond, the shank must have sufficient strength and rigidity in the cutting process in order to avoid chatter and distortion occurs. This requires the choice of appropriate cross-sectional area larger arbor, while also using higher strength materials to create Arbor, such as the use of quenched and tempered steel 45 or 50 gauge steel.
Cutting portion of the tool material requirements
Stainless steels, the required portion of the cutting tool material has a high wear resistance at high temperatures and can maintain its cutting performance. The most commonly used materials are: high-speed steel and carbide. As high-speed steel only 600 ° C the following to maintain its cutting performance, it is not appropriate for high-speed cutting, but only to the case of stainless steels at low speeds. Since carbide than ring saw blades high speed steel with a better heat resistance and wear resistance, hence the cemented carbide cutting tool made of a material more suitable for cutting of stainless steel.
Carbide of tungsten-cobalt alloy (YG) and tungsten-cobalt alloy (YT) two categories. Especially in larger vibration roughing and interrupted machining circumstances should adopt tungsten-cobalt alloy blades, it is not as brittle as tungsten-cobalt alloy, diamond grinding is not easy, easy chipping. Tungsten-cobalt alloy red hardness is better at high temperatures than tungsten-cobalt alloy wear, but it's brittle, intolerant shock, vibration, generally made of stainless steel finishing with a diamond cutter.
Diamond tool cutting part of the tool surface roughness requirements
Improve the surface finish of the cutting part of the tool can reduce the formation of diamond chips curled resistance, improved durability of the tool. Compared with the processing of ordinary carbon steel, stainless steel processing should be appropriately reduced to slow the cutting tool wear; also select the proper coolant in order to reduce the cutting process of cutting heat 14 inch saw blade and cutting force, extend tool life.
Material requirements for Arbor
Stainless steels, the cutting force of the diamond, the shank must have sufficient strength and rigidity in the cutting process in order to avoid chatter and distortion occurs. This requires the choice of appropriate cross-sectional area larger arbor, while also using higher strength materials to create Arbor, such as the use of quenched and tempered steel 45 or 50 gauge steel.
Cutting portion of the tool material requirements
Stainless steels, the required portion of the cutting tool material has a high wear resistance at high temperatures and can maintain its cutting performance. The most commonly used materials are: high-speed steel and carbide. As high-speed steel only 600 ° C the following to maintain its cutting performance, it is not appropriate for high-speed cutting, but only to the case of stainless steels at low speeds. Since carbide than ring saw blades high speed steel with a better heat resistance and wear resistance, hence the cemented carbide cutting tool made of a material more suitable for cutting of stainless steel.
Carbide of tungsten-cobalt alloy (YG) and tungsten-cobalt alloy (YT) two categories. Especially in larger vibration roughing and interrupted machining circumstances should adopt tungsten-cobalt alloy blades, it is not as brittle as tungsten-cobalt alloy, diamond grinding is not easy, easy chipping. Tungsten-cobalt alloy red hardness is better at high temperatures than tungsten-cobalt alloy wear, but it's brittle, intolerant shock, vibration, generally made of stainless steel finishing with a diamond cutter.
2013年8月16日星期五
diamond coated tools and the ordinary coated tool
Stage diamond-coated graphite machining tool is the best choice, but also the tool that best reflects the tile cutting blades superior performance of graphite; diamond-coated carbide tool combines the advantages of natural diamond and carbide hardness and fracture strength toughness; But in the domestic diamond coating technology is still in its infancy, as well as the cost of inputs are big, so diamond coating there is not much development in the near future, but we can in the general tool, based on the optimization tool angle, material selection and other aspects of the structure and improvement of conventional coatings, in a way which is in graphite machining applications.
Diamond-coated tools and the general geometry of coated tools are essentially different, so the design of diamond coated tools, due to the particularity of graphite machining, its geometry can be properly amplified volume becomes large cut groove, it will not reduce the diamond discs wear resistance of the tool edge port; for ordinary TiAlN coating, although the ratio of its uncoated tool wear significantly improved, but compared to diamond coating, in the processing of its geometry graphite should appropriate to put small, in order to increase its wear resistance.
The diamond coating, the coating of the world many companies invest a lot of manpower and material resources to research and development related to coating technology, but so far, foreign companies mature and economical coating confined to Europe; as a Excellent graphite machining tool, also using the world's most advanced coating technology for surface treatment of the tool, in order to ensure that the processing life while ensuring the economic and practical tool.
The company invested heavily in the wet polishing pad introduction of foreign advanced production and testing equipment, equipment performance and advanced technology in the domestic leading level, experienced mechanical, electrical, welding, management and other professional and highly qualified technical team technical staff, we have developed products are widely used in aerospace, aviation, automotive, tooling, machining, watches, electronics, steel, bio-engineering and other fields. Matsuno products with superior performance, reliable quality, widely sold at home and abroad, the majority of users trust. Matsuno is willing to join hands with all customers, and seek common development.
Diamond-coated tools and the general geometry of coated tools are essentially different, so the design of diamond coated tools, due to the particularity of graphite machining, its geometry can be properly amplified volume becomes large cut groove, it will not reduce the diamond discs wear resistance of the tool edge port; for ordinary TiAlN coating, although the ratio of its uncoated tool wear significantly improved, but compared to diamond coating, in the processing of its geometry graphite should appropriate to put small, in order to increase its wear resistance.
The diamond coating, the coating of the world many companies invest a lot of manpower and material resources to research and development related to coating technology, but so far, foreign companies mature and economical coating confined to Europe; as a Excellent graphite machining tool, also using the world's most advanced coating technology for surface treatment of the tool, in order to ensure that the processing life while ensuring the economic and practical tool.
The company invested heavily in the wet polishing pad introduction of foreign advanced production and testing equipment, equipment performance and advanced technology in the domestic leading level, experienced mechanical, electrical, welding, management and other professional and highly qualified technical team technical staff, we have developed products are widely used in aerospace, aviation, automotive, tooling, machining, watches, electronics, steel, bio-engineering and other fields. Matsuno products with superior performance, reliable quality, widely sold at home and abroad, the majority of users trust. Matsuno is willing to join hands with all customers, and seek common development.
alloy saw maintenance guide
Carbide saw blades in the transport and storage process, should be carried out to maintain the original packaging to avoid damage. Since carbide saw blade is extremely sharp, so use or transport should be protected to avoid being scratched blade. When stored dry storage environment must be guaranteed, and should avoid other possible factors for blade damage.
Second, the operation using the
1, the operator should use the ceramic tile saw necessary safety shields, to avoid accidents.
2 before using circular saw blades for inspection, if found significant blade can not be clearly discernable or other, affect the safe use should immediately stop using, such as: Discover blade cracks, deformation or other security factors; pending Check that professionals can use to use. Please use clean sharp blades.
3, refer to the device manufacturer's manual, operating instructions must be strictly in accordance with the proper installation and use of the blade; must strictly respect through the blade and the safe use of equipment rules; before cutting blade must be securely mounted. Not be used during installation and impact the way beat locking blades.
4, the correct use of the locking harmonize the blade flange diameter, flanges should be less than one-third of the blade to avoid unbalanced blade during use.
5, in the non-mechanical feeding method using climb milling machining can not add, to avoid danger. Must be properly specified equipment in accordance with the direction of rotation blade and install.
6, carbide saw blades can be used to match the equipment used, carbide saw blade can not be used to cut cement sandy material, unless otherwise stated.
7, the blade is less than the normal speed of progress Do not be cut, the blade speed can not exceed the diamond bandsaw blades maximum allowable value and must strictly respect through equipment equipment manufacturer's instructions.
8, requires the use of adjustable ring, adjustable ring must be firmly bonded to the saw body, and can not be higher than the adjustable ring side saw the body, to ensure that even after installing adjustable ring mounted blade secure clamping fastening; adjustable ring must have a diameter large enough to Yasumasa good cooperation with the blade, without changing the center of the blade.
9, running before the device must be clean out all extraneous items, non-related personnel should stay away from this area, can not touch the blade during operation of other tools, installation tools or equipment parts, should ensure that all unsafe factors have been ruled out.
10, equipment operation throughout the ring saw blades process must be someone on duty.
11, the workpiece, carefully check all parts, ensure that the workpiece is no impurities.
Third, the maintenance
A saw blade use for some time should always check and grinding.
2, when the thickness is less than 1mm serrated, the blade should not continue to use.
3, grinding blades, must be trained professionals.
4, for the repair of the blade, the blade prohibit any design changes.
5, do not use should pay attention to maintenance.
Second, the operation using the
1, the operator should use the ceramic tile saw necessary safety shields, to avoid accidents.
2 before using circular saw blades for inspection, if found significant blade can not be clearly discernable or other, affect the safe use should immediately stop using, such as: Discover blade cracks, deformation or other security factors; pending Check that professionals can use to use. Please use clean sharp blades.
3, refer to the device manufacturer's manual, operating instructions must be strictly in accordance with the proper installation and use of the blade; must strictly respect through the blade and the safe use of equipment rules; before cutting blade must be securely mounted. Not be used during installation and impact the way beat locking blades.
4, the correct use of the locking harmonize the blade flange diameter, flanges should be less than one-third of the blade to avoid unbalanced blade during use.
5, in the non-mechanical feeding method using climb milling machining can not add, to avoid danger. Must be properly specified equipment in accordance with the direction of rotation blade and install.
6, carbide saw blades can be used to match the equipment used, carbide saw blade can not be used to cut cement sandy material, unless otherwise stated.
7, the blade is less than the normal speed of progress Do not be cut, the blade speed can not exceed the diamond bandsaw blades maximum allowable value and must strictly respect through equipment equipment manufacturer's instructions.
8, requires the use of adjustable ring, adjustable ring must be firmly bonded to the saw body, and can not be higher than the adjustable ring side saw the body, to ensure that even after installing adjustable ring mounted blade secure clamping fastening; adjustable ring must have a diameter large enough to Yasumasa good cooperation with the blade, without changing the center of the blade.
9, running before the device must be clean out all extraneous items, non-related personnel should stay away from this area, can not touch the blade during operation of other tools, installation tools or equipment parts, should ensure that all unsafe factors have been ruled out.
10, equipment operation throughout the ring saw blades process must be someone on duty.
11, the workpiece, carefully check all parts, ensure that the workpiece is no impurities.
Third, the maintenance
A saw blade use for some time should always check and grinding.
2, when the thickness is less than 1mm serrated, the blade should not continue to use.
3, grinding blades, must be trained professionals.
4, for the repair of the blade, the blade prohibit any design changes.
5, do not use should pay attention to maintenance.
2013年8月15日星期四
carbide saw blades used
Including tooth carbide saw blades, angle, number of teeth, multi-chip sawing wood thickness, blade diameter, carbide, etc. Most types of parameters that determine the processing capacity of the diamond cutting tools saw blade and cutting performance. Select the blade when the blade to the correct selection of parameters as needed. Tooth, tooth commonly have flat teeth, Dou tooth, trapezoidal tooth, inverted trapezoidal tooth, etc. (Figure 1). Flat teeth the most widely used, mainly for ordinary wood sawing, this tooth is relatively simple, Jukou rough, when operating in the granite polishing pad slotted flat teeth can process flat bottom. Dou teeth sawing kerf quality is better for cutting a variety of wood-based panels, plywood. Trapezoidal tooth suitable sawing plywood, fire board, obtain higher cutting quality. Inverted trapezoidal tooth commonly used in the bottom slot blades. Sawtooth angle is in the cutting position when the sawtooth. Serrated cutting angle affect performance results. Greatest impact is on the cutting rake angle. Carbide saw blade is the most commonly used cup wheels wood processing cutting tools, carbide saw blade quality and quality of processed products are closely related. Reasonable selection of the correct carbide saw blades for improving product quality, shorten cycle times, reduce processing costs is of great significance.
A new high-speed hacksaw trials
In order to extend the service life of the metal circular sawing machine with the new HSS film (new unused HSS film or after each grinding HSS film) has a running-in process more fully in the cutting operation begins within 10 minutes, reducing the feed rate is very necessary.
2, the cutting speed and feed
Cutting speed depends on the cross-section of the workpiece to be cut and toughness. For such a hard cutting discs cutting stainless steel, high toughness materials, a slower speed is very conducive to improving the life of HSS film; while for some iron and the like, relatively low toughness materials, high-speed hacksaw speed can be increased accordingly.
3, timely and correct grinding HSS film
Pay attention to the HSS film work, the occurrence of abnormalities such as vibration, my voice, machined surface material moving situation, you must promptly stop adjustment, and cutting blades timely grinding, maintaining peak profits. Timely and proper re-grinding HSS film can play a high-speed hacksaw maximum performance.
4, adding a suitable cooling liquid
Because when the heat generated by the cutting, it may cause HSS film deformation, no coolant, not only affect the speed hacksaw life, but cutting effect is not ideal. So please join coolant.
5, observe sawdust determine the concrete saws effectiveness of the current high-speed hacksaw state
1) is very fine sawdust or powdered, which means cutting pressure is too small
2) of a soft sawdust, which means overload cut
3) sawdust as long spiral filaments, which means that in good condition
4) If the increase in feed rate, the corresponding number of teeth should be selected coarse
2, the cutting speed and feed
Cutting speed depends on the cross-section of the workpiece to be cut and toughness. For such a hard cutting discs cutting stainless steel, high toughness materials, a slower speed is very conducive to improving the life of HSS film; while for some iron and the like, relatively low toughness materials, high-speed hacksaw speed can be increased accordingly.
3, timely and correct grinding HSS film
Pay attention to the HSS film work, the occurrence of abnormalities such as vibration, my voice, machined surface material moving situation, you must promptly stop adjustment, and cutting blades timely grinding, maintaining peak profits. Timely and proper re-grinding HSS film can play a high-speed hacksaw maximum performance.
4, adding a suitable cooling liquid
Because when the heat generated by the cutting, it may cause HSS film deformation, no coolant, not only affect the speed hacksaw life, but cutting effect is not ideal. So please join coolant.
5, observe sawdust determine the concrete saws effectiveness of the current high-speed hacksaw state
1) is very fine sawdust or powdered, which means cutting pressure is too small
2) of a soft sawdust, which means overload cut
3) sawdust as long spiral filaments, which means that in good condition
4) If the increase in feed rate, the corresponding number of teeth should be selected coarse
2013年8月14日星期三
diamond cutting tool material is the substance
Produced with natural diamonds diamond cutter arc portion of its edge under the microscope at 600 times the unnotched, suitable for processing gold, silver, copper, aluminum (aluminum), zinc (zinc alloy), acrylic (PMMA) and other materials . Diamond cutter hardness and thermal conductivity is a natural substance in the stone polishing pads highest natural diamond cutter so special knife with low consumption and long life unit easy to use features and to ensure high precision and mirror finish, roughness Ra ≤ 0.01um, △ 14 above. tip arc accuracy <1um, edge radius reaches satisfied fans middleweight, cut thin capacity <10mm. particularly suitable finishing copper and aluminum and their alloys, jewelry processing in aerospace manufacturing optical instruments watches instrumentation and other fields. widely used, such as: gold and silver jewelry flower cars nameplate router bits nameplate aluminum high gloss acrylic panel approved spent high light chamfering various specular highlights CD pattern turning Fresnel lens mold motor commutator pens watches accessories and non-ferrous metals mirror directional gyro computer hard substrate silicon lenses IOLs copier drum VCR drum tech products such as mirror cutting.
Natural diamond tool hardness HV9000-10000, is the hardest substance in nature. Cutting tool can be made longer maintain dimensional stability, and therefore have a long service life. Performance can be achieved roughness Ra (0.01-0.025) μm. Was at a high temperature under high pressure diamond powder plus solvent polymerization of polycrystalline materials, lower hardness than natural diamond (HV6000 or so), PCD cutting tools with carbide tools compared , hardness 3-4 times higher; wear resistance and metal drill bits high life 50-100 times; cutting speed can be increased 5-20 times; roughness can be achieved Ra0.05μm, brightness inferior to natural diamond cutters. High cutting efficiency, precision and stability.
Diamond Tool is a natural diamond cutting tools, medical natural diamond cutting tools, cutting tools into a series of lenses, VCR drum series dedicated tools, watches machining tool series, natural diamond knife Scope: metal car parts; auto parts; surface treatment ; technology products; carved; copper materials approved spending; acrylic mirror effect; mobile metal buttons; phones. Digital. MP3 shell; case. Nameplates, signs and high light stria; Car CD profiling; aluminum products high light; electrical enclosures approved spending; lenses, optical, infrared and other fields widely used.
Natural diamond tool hardness HV9000-10000, is the hardest substance in nature. Cutting tool can be made longer maintain dimensional stability, and therefore have a long service life. Performance can be achieved roughness Ra (0.01-0.025) μm. Was at a high temperature under high pressure diamond powder plus solvent polymerization of polycrystalline materials, lower hardness than natural diamond (HV6000 or so), PCD cutting tools with carbide tools compared , hardness 3-4 times higher; wear resistance and metal drill bits high life 50-100 times; cutting speed can be increased 5-20 times; roughness can be achieved Ra0.05μm, brightness inferior to natural diamond cutters. High cutting efficiency, precision and stability.
Diamond Tool is a natural diamond cutting tools, medical natural diamond cutting tools, cutting tools into a series of lenses, VCR drum series dedicated tools, watches machining tool series, natural diamond knife Scope: metal car parts; auto parts; surface treatment ; technology products; carved; copper materials approved spending; acrylic mirror effect; mobile metal buttons; phones. Digital. MP3 shell; case. Nameplates, signs and high light stria; Car CD profiling; aluminum products high light; electrical enclosures approved spending; lenses, optical, infrared and other fields widely used.
economic milling tool life
The main purpose is to make the rough metal removal rate reaches the maximum: As a matter of fact whether increased axial or radial feed to 3D surface machining, HSC will be severely affected by the polishing pads for granite constraints of technology, in order to improve the processing rate, only by increasing the cutting it. However, there will be other practical and technical constraints.
While increasing the axial and radial cutting depth, as well as increasing the feed rate (vf improve the cutoff wheel speed does not necessarily improve the HSC cutting speed), should be able to help improve processing efficiency.
On the one hand, these milling processes a result, the efficiency of conventional milling is almost the same. On the other hand, in a certain cutting speeds increase the feed rate can cause the tool to improve feed rate per tooth, so increases the mechanical load on the cutter. Regardless of the selected cutting edge geometry and tool material to, in the process of cutting forces will have a relatively high, which in turn will increase the machine work environment.If both cutting forces associated with the cutting tools arithmetic mean of the tool set, can be determined through testing, a cutting force of the tool contour reduced 23.5%. To maximize the output power of this spindle, the design with a cutting edge contour appears HPC roughing tool is an excellent choice.In addition to high-speed metal cutting and optimizing the use of shaft output power requirements and, in the economics of milling, the tool life is also a key factor.HPC milling is described as to meet the requirements to improve milling metal removal, which is to determine the potential performance of a process value of the key technologies.
While increasing the axial and radial cutting depth, as well as increasing the feed rate (vf improve the cutoff wheel speed does not necessarily improve the HSC cutting speed), should be able to help improve processing efficiency.
On the one hand, these milling processes a result, the efficiency of conventional milling is almost the same. On the other hand, in a certain cutting speeds increase the feed rate can cause the tool to improve feed rate per tooth, so increases the mechanical load on the cutter. Regardless of the selected cutting edge geometry and tool material to, in the process of cutting forces will have a relatively high, which in turn will increase the machine work environment.If both cutting forces associated with the cutting tools arithmetic mean of the tool set, can be determined through testing, a cutting force of the tool contour reduced 23.5%. To maximize the output power of this spindle, the design with a cutting edge contour appears HPC roughing tool is an excellent choice.In addition to high-speed metal cutting and optimizing the use of shaft output power requirements and, in the economics of milling, the tool life is also a key factor.HPC milling is described as to meet the requirements to improve milling metal removal, which is to determine the potential performance of a process value of the key technologies.
the hollow drill cutting analysis of the impact of
Hollow drill bit is a more appropriate tool to use portable hole machining tool. However, due to the manufacturing process of the hollow drill bit more complex, and the blind holes can not be processed, so in the metal cutting process is not widely used, usually only in the wood band saw blades processing of a number of large-diameter through-hole of the workpiece or a noble metal or drilling equipment used only when the power is limited . Since there is no standard hollow drill styling products, so most of the processing for special materials developed hollow drill bit is required.
We worked to develop a user for processing difficult materials special hollow drill bit. Code of material to be processed U-Mn, the main chemical components include: carbon (0.56% to 0.68%), manganese (1.35% to 1.65%), silicon (0.2% to 0.35%), etc.; tensile strength ≥ 882N/mm2, hardness and wear resistance are high. The drill is used in a 17mm thick material processing? 30 +0.5 mm hole, portable drilling rig power <1000w, requires drill life> 30min, drill material W6Mo5Gr4V2. In the development process of the hollow drill bit, drill through repeated adjustment of the design parameters and drilling tests to finalize drill geometry parameters: rake angle g = 12 °, clearance angle a = 9 °, vice posterior horn a1 = 3 ° .
Here's the design of the cutting hollow drill bit to make a brief analysis of the impact.
1, drill cutting rake angle change on the cutting wheels impact of
Rake angle on the cutting force of the impact
The changes will affect the anterior horn of the chip material deformation, so that the cutting force change. Chip deformation greater cutting forces greater; chip deformation is smaller, the smaller the cutting force. This angle is 0 ° ~ 15 ° range of changes, the cutting force correction coefficient ranges from 1.18 to 1.
Rake angle drill durability against impact
Increasing the rake angle drill, makes the tip strength and thermal volume decreases, while the tip will affect the force. This angle is positive, the tip tensile stress; current angle is negative, the tip compressive stress. Such as the selection of the rake angle is too large, although the increased drill sharpness, reduced cutting forces, but the tip tensile stress suffered greater tip strength decreased, easily broken. In many drill cutting tests are due to excessive damage to the anterior horn. However, since the material to be machined high hardness and strength, coupled with a portable drill spindle and machine rigidity is low, such as the selection of the rake angle is too small, the increase in drilling cutting force causes the spindle vibration, vibration apparent machined surface pattern, drill durability will be reduced.
2, the posterior horn of the impact of changes on the drill cutting
After increasing flank angle can reduce the friction between the cutting material, reducing the surface of the extrusion process. However, if after the angle is too large, it will reduce the edge strength and heat dissipation.
Directly affects the size of the posterior horn drill durability. In the drilling process, the drill main wear to mechanical abrasion and wear of the phase change. Consider mechanical abrasion wear when cutting life is constant, the posterior horn of the larger cutting longer available; consider phase transition wear, after the drill angle increases cooling capacity will decrease. Bit wear, with the flank wear with a gradual widening gradually increase cutting power, heat generated by friction will gradually increase, the bit temperature, when the temperature rises to the bit phase transition temperature, the bit will appear rapid wear.
3, drill sharpening process on the impact of design
Hollow drill bit less dosage, processing small quantities, so the design should consider the drill process issues, as far as common machining equipment and tools used to achieve processing and grinding.
The rake chip out, so a direct impact on the shape of the rake face and chip performance chip shape. Used chips in the process of being squeezed and friction of the rake face, and further deformation. The 4 inch circular saw blade maximum degree of deformation of the base metal chips and to slip along the rake face, the chips bottom length is longer, thereby forming a variety of crimp shape. When using a hollow drill bit and hope the chips into crumbs or ribbon cuttings, in order to facilitate chip removal. For ease of machining and grinding, must be designed for flat rake face, without chip breaking groove. Rake in use does not require re-grinding.
Hollow drill flank is most likely to re-grinding of the face, but also the fastest surface wear, so hollow drill flank grinding sharpening is achieved.
Deputy Vice flank divided into inner and outer flank minor flank. Heavy grinding perspective, re-grinding inner and outer flanks not easy to achieve, so minor flank shall be designed for a throwaway form.
Based on the above analysis, the hollow drill blade is designed in the form shown in Figure 1. Processing Practice has proved that the design can meet the requirements and tool regrinding requirements.
4, the cutting fluid used and the impact on the drill cutting
The main characteristics of the hollow drill processing hole of the core is not to be cut, thus cutting the hollow drill twist ratio was significantly reduced, the power required for drilling and cutting the heat generated is small.
High-speed steel drill with a hollow drill, because of the hardness of the bit processing area a great influence on the temperature, thus the drilling process must be cooled using a cooling fluid (eg without coolant, the start bit will wear the phase change and rapid wear of the main wear and tear). We started using an external spray cooling, but bit-position horizontal axis machining, the coolant is not easy to enter the drill blade portion, a large consumption of cooling fluid, the cooling effect is not ideal. The redesigned drill spindle structure change, the external spray cooling becomes an internal spray cooling, the cooling fluid from the hollow drill core join, the coolant can reach the cutting part of the drill, thereby significantly reducing coolant consumption, improved cooling effect.
5, the hollow drill bit to use effects
A well-designed hollow drill bit should also meet the requirements of the following aspects: ① easy to manufacture, to use common tools and common tooling; ② easy re-sharpening, grinding machine can be used for general sharpening; ③ high efficiency, long life; ④ low prices.
We have developed a hollow drill basically reached the above requirements. In actual use, drill durability is stable up to 50 minutes, the diameter tolerance, surface roughness, all reached the design requirements. Because only regrinding flank, posterior horn drill easier to control, in an ordinary grinder can be easily implemented on sharpening.
Use of bit and description
Bit is used to drill out the solid material through holes or blind holes, and is able to have a hole reaming tools. Twist drills are commonly used, flat drill, center drill, deep hole drilling and core drill. Reamers and countersinks although not drill holes in solid material, but will also be used to drill them into a class.
Twist drill
Twist drill through its axis fixed relative to the rotary cutting tool for drilling a workpiece hole. Its flute and shape into a spiral twist named. Spiral chute slot 2 slots 3 slots or more, but the diamond bandsaw blades most common slot 2. Twist can be held in manual, electric handheld drill tools or drilling machines, milling machines, lathes and even use on machining centers. Drill material is generally high-speed tool steel or carbide.
Twist is the most widely-hole machining tool. Diameter range of usually 0.25 to 80 mm. It is mainly the working portion and the shank portion. Working part has two spiral grooves, the shape of cannabis, hence the name. In order to reduce drilling holes intramural guide portion and the friction, twist drill tip to the shank from the direction of decreasing diameter inverted cone. Helix angle of twist drill cutting edge came principally affected the size of angles, edge flap strength and chip performance, typically 25 ° ~ 32 °. Available spiral groove milling, grinding, hot-rolled or hot extrusion processing methods, the drill bit tip is formed by grinding after the cutting portion. Standard twist angle of the cutting portion 118, a horizontal blade angle is 40 ° ~ 60 °, after the angle of 8 ° ~ 20 °. For structural reasons, a large rake angle in the outer edge, and gradually decreases toward the center, horizontal blade at a negative rake angle (up to about -55 °), when drilling from the compression. In order to improve the cutting performance of twist drills, according to the nature of the material to be machined part will repair ground cutting various shapes (such as drilling group). Form of shank twist drill straight shank and taper shank are two processing caught in the drill chuck the former, the latter inserted in the machine spindle or tailstock taper hole. Generally high-speed steel twist drill. Inserts welded carbide blade or twist the crown for machining cast iron, hardened steel and non-metallic materials, solid carbide twist drills for machining small parts and printed circuit boards and other instrumentation.
Cutting portion of the drill flat spade, simple structure, low cost, easily cutting fluid into the hole, but the cutting and chip performance is poor. Flat structure integral drill and assembly two. Integral mainly for drilling diameter of 0.03 to 0.5 mm pores. Fabricated flat diamond blade can be changed, can be cooled, mainly for the drilling diameter 25 to 500 mm large hole.
Deep hole drilling is typically the hole saw blades machining hole depth is greater than the diameter of the bore of the tool 6. Commonly used gun drilling, BTA deep hole drilling, jet drill, DF deep hole drilling. Nesting also used in drilling deep holes.
Reamer has three to four teeth, better rigidity than the twist, to expand the existing hole and improve the machining accuracy and finish.
Countersinks have more teeth to the end of the hole forming method processed into the desired shape, for processing a variety of countersunk head screws countersunk holes, holes or flattened outer end face.
Center drill for drilling holes shaft center of the workpiece, it is essentially a small twist by the helix angle and tct circular saw blade countersink drill composite, so called composite center drill.
Center drill
Prefabricated hole machining for precise positioning guide twist drill hole processing, reduce errors.
Center drill is used in other parts of the end face of the shaft center hole machining.
The product is easy-cutting, chip is good. There are two kinds of center drill type: A type: without protecting chamfers center drill, B: with protecting chamfers center drill, machining diameter d = 1 ~ 10mm center hole, usually without protective dimensional center drill ( A type); step long high precision of the workpiece, the centering cone 60 degrees in order to avoid being damaged, the general center of the cone with a protective cone
Twist drill
Twist drill through its axis fixed relative to the rotary cutting tool for drilling a workpiece hole. Its flute and shape into a spiral twist named. Spiral chute slot 2 slots 3 slots or more, but the diamond bandsaw blades most common slot 2. Twist can be held in manual, electric handheld drill tools or drilling machines, milling machines, lathes and even use on machining centers. Drill material is generally high-speed tool steel or carbide.
Twist is the most widely-hole machining tool. Diameter range of usually 0.25 to 80 mm. It is mainly the working portion and the shank portion. Working part has two spiral grooves, the shape of cannabis, hence the name. In order to reduce drilling holes intramural guide portion and the friction, twist drill tip to the shank from the direction of decreasing diameter inverted cone. Helix angle of twist drill cutting edge came principally affected the size of angles, edge flap strength and chip performance, typically 25 ° ~ 32 °. Available spiral groove milling, grinding, hot-rolled or hot extrusion processing methods, the drill bit tip is formed by grinding after the cutting portion. Standard twist angle of the cutting portion 118, a horizontal blade angle is 40 ° ~ 60 °, after the angle of 8 ° ~ 20 °. For structural reasons, a large rake angle in the outer edge, and gradually decreases toward the center, horizontal blade at a negative rake angle (up to about -55 °), when drilling from the compression. In order to improve the cutting performance of twist drills, according to the nature of the material to be machined part will repair ground cutting various shapes (such as drilling group). Form of shank twist drill straight shank and taper shank are two processing caught in the drill chuck the former, the latter inserted in the machine spindle or tailstock taper hole. Generally high-speed steel twist drill. Inserts welded carbide blade or twist the crown for machining cast iron, hardened steel and non-metallic materials, solid carbide twist drills for machining small parts and printed circuit boards and other instrumentation.
Cutting portion of the drill flat spade, simple structure, low cost, easily cutting fluid into the hole, but the cutting and chip performance is poor. Flat structure integral drill and assembly two. Integral mainly for drilling diameter of 0.03 to 0.5 mm pores. Fabricated flat diamond blade can be changed, can be cooled, mainly for the drilling diameter 25 to 500 mm large hole.
Deep hole drilling is typically the hole saw blades machining hole depth is greater than the diameter of the bore of the tool 6. Commonly used gun drilling, BTA deep hole drilling, jet drill, DF deep hole drilling. Nesting also used in drilling deep holes.
Reamer has three to four teeth, better rigidity than the twist, to expand the existing hole and improve the machining accuracy and finish.
Countersinks have more teeth to the end of the hole forming method processed into the desired shape, for processing a variety of countersunk head screws countersunk holes, holes or flattened outer end face.
Center drill for drilling holes shaft center of the workpiece, it is essentially a small twist by the helix angle and tct circular saw blade countersink drill composite, so called composite center drill.
Center drill
Prefabricated hole machining for precise positioning guide twist drill hole processing, reduce errors.
Center drill is used in other parts of the end face of the shaft center hole machining.
The product is easy-cutting, chip is good. There are two kinds of center drill type: A type: without protecting chamfers center drill, B: with protecting chamfers center drill, machining diameter d = 1 ~ 10mm center hole, usually without protective dimensional center drill ( A type); step long high precision of the workpiece, the centering cone 60 degrees in order to avoid being damaged, the general center of the cone with a protective cone
2013年8月12日星期一
PCB drilling with a drill
The so-called carbide to tungsten carbide face as the substrate, cobalt powder as a binder by pressing and sintering. High precision positioning, do not causative drill sleeve. But the toughness is poor, very brittle, in order to improve the performance of cemented carbide, and some use carbide substrate in a chemical vapor deposition on a layer of 5-7 micron titanium carbide special hardware (TIC) or titanium nitride (TIN), to have a higher hardness. Carbide drill ultra fine particles, which equality of tungsten carbide grain size of the phase 1 micron or less. To save costs using welding shank drill now better structure, the original carbide drill bit for the wet diamond polishing pads group are now back with a stainless steel drill shank, cost greatly diminished, but not the same as the material used and its dynamic concentricity than but groups carbide drill, surprisingly in the small diameter side. In the range of the flute length, diameter of the drill is an inverted cone, with the hole when drilling wall friction is small, high quality drilling. In the actual causative process can be based on the need to use. This drill is not only high hardness and compressive and flexural strength are increased. There's a physical way to the top of the drill generate a diamond film, a great increase of hardness and wear resistance of the drill. Some of the ion infusion techniques, titanium, nitrogen, and carbon, the matrix perfusion certain depth, Bu Wei and increase the hardness and strength of the drill components Regrinding can move into the perfusion. Large helix angle, chip speed, suitable for high-speed grinding. Because of its hardness, slender, very wearable, a certain strength, suitable for high-speed grinding. Straight shank twist drill mostly for single head machines, PCB drilling relatively simple or single panel, now in a large circuit board manufacturing plant has been rarely seen, its drilling depth of up to 10 times the diameter of the drill.
1, to choose a good brand guarantee product quality
PCB drilling with a drill ordinary carbide are used as carbide drill bits ring oxygen glass cloth complex copper plate wear on cutting surprisingly fast. Common drill shank diameter of 3.00mm and 3.175mm. Most of the manufacturers causative holds many lessons for digital control drilling machine, numerical control drilling causative is fixed shank carbide drill bit, which is characterized by semi-automatic Gaiyi drill can be implemented. Usually with WC 94 one hundred percent, one hundred percent cobalt 6. Holds many lessons, many drill manufacturers, sub-national and imported.
2, pay attention to the material of drill
PCB drilling with a drill with straight shank twist drill, twist drill set and fixed shank shank Spade (undercut) drill bit.
Optional digital control drilling drill approach:
3, to understand the drill category and characteristics.
Domestic products and foreign products dwarf slight gap between the price of course, but also slightly more expensive imports, the market also has production from Taiwan and Hong Kong, as well as part of the production in Taiwan to fight the U.S. and European brands of drills, contrast causative Europe, America and Japan the quality and stability of the concrete cutting drill imports, although the price is slightly expensive but good value for money for the craft members who, in the course of the actual causative drill quality problems that occur because of a handful of chances, such as the production of products require a higher import causative proposed drill, drill Europe and America high hardness and Japan softer, Europe drill rather break than bend causative of migraine-prone holes but could not help but break the higher the probability that Japan is better flexibility drill holes prone to easy to break, but missed the odd side is a small drill hole. Carbide hardness and strength, not only the ratio of cobalt and tungsten carbide and related particles are also associated with the face. Laminated substrate is not high in the case, causative drill sleeve can avoid drilling biased.
1, to choose a good brand guarantee product quality
PCB drilling with a drill ordinary carbide are used as carbide drill bits ring oxygen glass cloth complex copper plate wear on cutting surprisingly fast. Common drill shank diameter of 3.00mm and 3.175mm. Most of the manufacturers causative holds many lessons for digital control drilling machine, numerical control drilling causative is fixed shank carbide drill bit, which is characterized by semi-automatic Gaiyi drill can be implemented. Usually with WC 94 one hundred percent, one hundred percent cobalt 6. Holds many lessons, many drill manufacturers, sub-national and imported.
2, pay attention to the material of drill
PCB drilling with a drill with straight shank twist drill, twist drill set and fixed shank shank Spade (undercut) drill bit.
Optional digital control drilling drill approach:
3, to understand the drill category and characteristics.
Domestic products and foreign products dwarf slight gap between the price of course, but also slightly more expensive imports, the market also has production from Taiwan and Hong Kong, as well as part of the production in Taiwan to fight the U.S. and European brands of drills, contrast causative Europe, America and Japan the quality and stability of the concrete cutting drill imports, although the price is slightly expensive but good value for money for the craft members who, in the course of the actual causative drill quality problems that occur because of a handful of chances, such as the production of products require a higher import causative proposed drill, drill Europe and America high hardness and Japan softer, Europe drill rather break than bend causative of migraine-prone holes but could not help but break the higher the probability that Japan is better flexibility drill holes prone to easy to break, but missed the odd side is a small drill hole. Carbide hardness and strength, not only the ratio of cobalt and tungsten carbide and related particles are also associated with the face. Laminated substrate is not high in the case, causative drill sleeve can avoid drilling biased.
the drill should be packed in special packing boxes
1, the to avoid vibrations collide.
2, when used, from packing boxes should immediately remove the drill bit attached to the spindle collet header or automatic replacement drill tool library. Spent immediately put back packing boxes.
3, use the drill diameter measurement tool microscope and other non-contact measurement equipment, to avoid the cutting edge in contact with the mechanical gauge was bruised.
4, some CNC drilling machine CNC drilling using some positioning ring retaining ring is not used, such as the use of its positioning ring installation depth positioning must be accurate, as it does not use retaining ring fitted to the drill spindle elongation to adjust consistent, multi-spindle drilling machine to pay attention to this point, to make each spindle drilling depth to be consistent. If not possible to make drill drill drill through the surface or not caused by circuit board scrap.
5, using 40 times the usual three-dimensional microscopy drill blade wear.
6, the spindle and to always check the concentricity of the collet and the collet chuck clamping force, will result in poor concentricity of small diameter drill bit off and pore size, etc., the tct blades clamping force will cause the actual speed is not good Set speed does not match between the chuck and the drill bit slipping.
7, fixed shank drill head clamping collet drill shank length of 4 to 5 times the diameter to clamp securely.
8, should always check the spindle presser foot. Presser foot contact surface perpendicular to the spindle is horizontal and not shaking, to prevent drilling off the drill and produce partial holes.
9, drilling better than vacuuming, vacuum air temperature can be reduced drill, colleagues away dust reduce friction generates heat.
10, the substrate stack comprises upper and lower plate to drill a hole workbench trough positioning system to locate a prison, lie flat. Use adhesive tape to prevent the drill bit to be on the tape so that a drill swarf adhesion, causing difficulties and chip off the diamond.
11, ordering manufacturers drill, the Plate Compactor factory inspection when sampling the compliance of its 4%. And 100% of 10 to 15 times with a microscopic examination of the gaps, scratches and cracks.
12, drill timely re-grinding, increase the use and re-drill grinding times, extending bit life, reduce production costs and expenses. Microscope usually measured length of the two main cutting edges, the wear depth should be less than 0.2mm. Regrinding when rubbed 0.25mm. Plain shank drill can be reground three times, shovel-shaped head (undercut) of the drill can be reground two times. Excessive turning grinding quality and accuracy of its drilling will decline, will cause the finished circuit board scrap. Excessive turning mill backfired.
13, when the wear due to abrasion and 14 inch saw blade diameter reduction of 2% compared to the original, then the bit scrapped.
14 bit parameter settings in general, manufacturers have to provide a drill bit plant production speed and lower speed parameter table, the parameter is a reference only, the actual craft workers through actual use but also draw a line with The actual speed and the speed of the drill parameters are usually the reference parameter actual parameters are different but the difference is not too much.
2, when used, from packing boxes should immediately remove the drill bit attached to the spindle collet header or automatic replacement drill tool library. Spent immediately put back packing boxes.
3, use the drill diameter measurement tool microscope and other non-contact measurement equipment, to avoid the cutting edge in contact with the mechanical gauge was bruised.
4, some CNC drilling machine CNC drilling using some positioning ring retaining ring is not used, such as the use of its positioning ring installation depth positioning must be accurate, as it does not use retaining ring fitted to the drill spindle elongation to adjust consistent, multi-spindle drilling machine to pay attention to this point, to make each spindle drilling depth to be consistent. If not possible to make drill drill drill through the surface or not caused by circuit board scrap.
5, using 40 times the usual three-dimensional microscopy drill blade wear.
6, the spindle and to always check the concentricity of the collet and the collet chuck clamping force, will result in poor concentricity of small diameter drill bit off and pore size, etc., the tct blades clamping force will cause the actual speed is not good Set speed does not match between the chuck and the drill bit slipping.
7, fixed shank drill head clamping collet drill shank length of 4 to 5 times the diameter to clamp securely.
8, should always check the spindle presser foot. Presser foot contact surface perpendicular to the spindle is horizontal and not shaking, to prevent drilling off the drill and produce partial holes.
9, drilling better than vacuuming, vacuum air temperature can be reduced drill, colleagues away dust reduce friction generates heat.
10, the substrate stack comprises upper and lower plate to drill a hole workbench trough positioning system to locate a prison, lie flat. Use adhesive tape to prevent the drill bit to be on the tape so that a drill swarf adhesion, causing difficulties and chip off the diamond.
11, ordering manufacturers drill, the Plate Compactor factory inspection when sampling the compliance of its 4%. And 100% of 10 to 15 times with a microscopic examination of the gaps, scratches and cracks.
12, drill timely re-grinding, increase the use and re-drill grinding times, extending bit life, reduce production costs and expenses. Microscope usually measured length of the two main cutting edges, the wear depth should be less than 0.2mm. Regrinding when rubbed 0.25mm. Plain shank drill can be reground three times, shovel-shaped head (undercut) of the drill can be reground two times. Excessive turning grinding quality and accuracy of its drilling will decline, will cause the finished circuit board scrap. Excessive turning mill backfired.
13, when the wear due to abrasion and 14 inch saw blade diameter reduction of 2% compared to the original, then the bit scrapped.
14 bit parameter settings in general, manufacturers have to provide a drill bit plant production speed and lower speed parameter table, the parameter is a reference only, the actual craft workers through actual use but also draw a line with The actual speed and the speed of the drill parameters are usually the reference parameter actual parameters are different but the difference is not too much.
2013年8月11日星期日
Introduce common drill
Twist is the most widely-hole machining tool. Diameter range of usually 0.25 to 80 mm. It is mainly the working portion and the shank by the drill portion. Working part has two spiral grooves, the industrial saw blades shape of cannabis, hence the name. In order to reduce drilling holes intramural guide portion and the friction, twist drill tip to the shank from the direction of decreasing diameter inverted cone. Helix angle of twist drill cutting edge came principally affected the size of angles, edge flap strength and chip performance, typically 25 ° ~ 32 °. Available spiral groove milling, grinding, hot-rolled or hot extrusion processing methods, the drill bit tip is formed by grinding after the cutting portion. Standard twist angle of the cutting portion 118, a horizontal blade angle is 40 ° ~ 60 °, after the angle of 8 ° ~ 20 °. For structural reasons, a large rake angle in the outer edge, and gradually decreases toward the center, horizontal blade at a negative rake angle (up to about -55 °), when drilling from the compression. In order to improve the cutting performance of twist drills, according to the nature of the material to be machined part will repair ground cutting various shapes (such as drilling group). Form of shank twist drill straight shank and taper shank are two processing caught in the drill chuck the former, the latter inserted in the machine spindle or tailstock taper hole. Generally high-speed steel twist drill. Inserts welded carbide blade or twist the crown for machining cast iron, hardened steel and non-metallic materials, solid carbide twist drills for machining small parts and printed circuit boards and other instrumentation.
Flat drill
Cutting portion of the drill flat spade, simple structure, low cost, easily cutting fluid into the hole, but the cutting and chip performance is poor. Flat structure integral drill and assembly two. Integral mainly for drilling diameter of 0.03 to 0.5 mm pores. Fabricated flat diamond blade can be changed, can be cooled, mainly for the drilling diameter 25 to 500 mm large hole.
Deep hole drilling
Deep hole drilling is typically the machining hole depth is greater than the diameter of the bore of the tool 6. Commonly used gun drilling, BTA deep hole drilling, jet drill, DF deep hole drilling. Nesting also used in drilling deep holes.
Reamer
Reamer has three to four teeth, better rigidity than the twist, to expand the existing hole and improve the machining accuracy and finish.
Countersink
Countersinks have more teeth to the end of the hole forming method processed into the desired shape, for processing a variety of countersunk head screws countersunk holes, holes or flattened outer end face.
Center drill
Center drill for drilling holes shaft center of the diamond bandsaw blades workpiece, it is essentially a small twist by the helix angle and countersink drill composite, so called composite center drill.
Bit Structure
A drill, comprising a shank (1), a tip shank, the tip has two in a main plane (C-C) on the cutting insert (5,5 '), said cutting blade (5,5 ') having a second common plane (E-E) is oriented to the center of the short cutting edges. Said blade forms a point-like central cutting edges used to enter the workpiece, and thus the bit pair. In the arbor, the establishment of two flutes (6,6 '), the flute (6,6') extending from the tip end in the end. Any length along the surface of the arbor, the flutes are in the plane of the tube diametrically opposite positions to each other, the tube plane of the two sides of the tube with a common edge with a flat blade (F-F) to 90 ° extends in the plane of the shank has a maximum rigidity. Center cutting edge of the second plane (E-E) in alignment with the blade shank with a flat bottom or main rigidity direction (F-F) at approximately a 90 ° angle.
One kind of concrete, etc. in drilling operations, drilling state can ease the situation suddenly changed, so that drilling operations stable, even in large grain chips produced when drilling efficiency is not caused by lowering of the drill.
Configuration which substantially radial cutting edge portion having at least two main cutting edge portion, and arranged in the circumferential direction of said main cutting edge portion and between the main cutting edge portion, at least two sub cutting blade portion said main cutting edge portion includes a main cutting edge as the cutting blade, the cutting blade inner end of the main center of rotation, the outer end of the cutting edge portion in the outer periphery of the rotation locus.
A cutting edge portion of the sub cutting blade as the sub cutting blade, the sub cutting blade inner end is located off the center of rotation to the outer side of the site, the outer end is located in the rotating cutting blade portion deviated from the center of rotation locus of the outer edge position.
A drill, with a drill tip disposed on the plurality of cutting blade portion, and provided on the base end side of the cutting blade portion and the base end portion of the shank portion is formed with a shaft-shaped drill main body;
Said cutting blade portion has a flank of the cutting surface and the engagement surface protruding toward the front end edge of the cutting edge formed by said center of rotation of the cutting blade from the drill side arranged substantially radially outer side;
The rotary axis of the direction of movement and the operation of the impact operation of cutting the composite, characterized in that said cutting blade portion has at least two main cutting edge portion, and disposed in the circumferential direction of the ring saw blades main cutting edge portion and the main cutting between the blade, at least two sub cutting blade portion;
The main cutting edge portion having a cutting edge as a main cutting edge, an inner end of said main cutting edge is located in the center of rotation, the outer end of the cutting edge portion in the outer periphery of the rotation locus, the sub cutting blade portion having as its the sub cutting blade cutting edge, the secondary cutting blade inner end is located radially outwardly from the rotation center deviate from the site, the outer end portion in the rotation from the cutting edge to the center of rotation locus of the outer side of the deviated position.
PDC bits
PDC bits [1] for short. Is commonly used in the oil drilling industry as a drilling tool.
PDC continuous improvement of product performance
In the past few years, PDC cutter quality and type have undergone tremendous changes. If the teeth of the 1980s to today's teeth for comparison, the difference is quite large. Because hybrid technology and manufacturing process changes, today's cutting teeth is much better quality and performance, so that the anti-erosion and impact drill capabilities are greatly improved.
Engineers also tungsten carbide substrate and the interface between the diamond has been optimized to improve the toughness of the cutting teeth. Process innovations in the diamond layer is also used to improve the abrasion resistance and thermal stability.
In addition to material and manufacturing process developments outside, PDC products in the tooth tooth design techniques and fabric also achieved a major breakthrough. Now, PDC products have been used previously can not be applied in areas such as stiffer, stronger and changing abrasive formations. This extension to new areas, the diamond (fixed cutter) cone drill bit and the balance between a great impact.
Initially, PDC drill bit can only be used for soft shale formations, the reason is hard mezzanine will damage the drill bit. However, due to the emergence of new technologies and changes in the structure, the current PDC drill bit for drilling hard interlayer has been able to and a long section of the hard rock formations. PDC bits are increasingly being used by people, especially with the continuous improvement of quality PDC teeth, in which case more and more prominent.
Since teeth bit design and improvement, PDC drill bit orientability also will increase, which further weakened the past in motor drilling cone bit advantage. Currently, PDC drill every day in many applications where the drilling supplant cone drill bit market.
Commonly used mechanical drills, twist drills with straight shank (ordinary type), you can drill: 45 # steel, stainless steel, diamond hardness using the weak point of the material. Alloy drill, you can drill Cr12 steel, the use of diamond hardness strong material. Use drill expertise can allow himself to lower profits.
PCB Drill Type
PCB drill drill drill control Type: PCB drilling with a drill with straight shank twist drill, fixed and fixed shank twist drill shank Spade (undercut) drill bit. Straight shank twist drill mostly for single head machines, PCB drilling relatively simple or single panel, now in a large circuit board manufacturing plant has been rarely seen in its drilling depth of up to 10 times the diameter of the drill. Laminated on the substrate is not high, the use of drill bit holder to avoid bias.
At present, most manufacturers use CNC drilling machine, CNC drilling using a carbide shank drill set, which is characterized to achieve automatic replacement drill. High positioning accuracy without the use of drill sets. Large helix angle, chip speed, suitable for high-speed cutting. In the range of the flute length, diameter of the drill is an inverted cone, when drilling with the hole wall friction is small, high quality drilling. Common drill shank diameter of 3.00mm and 3.175mm.
Drill material
PCB drilling with carbide drill bit is generally used as the epoxy glass cloth complex copper plate on the tool wear particularly fast. The so-called carbide drill gold is tungsten carbide powder as matrix, cobalt powder as a binder by pressurized sintering. Generally contain 94% tungsten carbide, 6% cobalt. Because of its high hardness, very wearable, a certain strength, suitable for high-speed cutting. But the toughness is poor, very brittle, in order to improve the performance of cemented carbide, and some use carbide substrate in a chemical vapor deposition on a 5-7 micron layer of special hard titanium carbide (TIC) or titanium nitride (TIN), to has a higher hardness. Some use ion implantation technology, titanium, nitrogen, and carbon injection the matrix certain depth, not only improves the hardness and strength and regrinding the drill can move into when they injected ingredients. There is a physical method to generate the bit at the top of a layer of diamond film, which greatly improves the hardness and wear resistance of the drill. Carbide hardness and strength, not only the ratio of cobalt and tungsten carbide, but also with the powder particles about. Carbide drill ultra fine particles, and its average grain size of tungsten carbide with 1 micron or less. This bit is not only high hardness and compressive strength and flexural strength are improved. To save costs Many drill shank welded structure, the original as a whole are carbide drill, drill shank back now made of stainless, but significantly reduced the cost of the material due to different concentricity less than its dynamic rigid whole alloy drill, particularly in the small diameter side.
The use of drill
1, the drill should be packed in special packing boxes, to avoid vibrations collide.
2, when used, from packing boxes should immediately remove the drill bit attached to the spindle collet header or automatic replacement drill tool library. Spent immediately put back packing boxes.
3, use the drill diameter measurement tool microscope and other non-contact measurement equipment, to avoid the cutting edge in contact with the mechanical gauge was bruised.
4, some CNC drilling machine CNC drilling using some positioning ring retaining ring is not used, such as the use of its positioning ring installation depth positioning must be accurate, as it does not use retaining ring fitted to the drill spindle elongation to adjust consistent, multi-spindle drilling machine to pay attention to this point, to make each spindle drilling depth to be consistent. If not possible to make drill drill drill through the surface or not caused by circuit board scrap.
5, using 40 times the usual three-dimensional microscopy drill blade wear.
6, the spindle and to always check the concentricity of the collet and the collet chuck clamping force, will result in poor concentricity of small diameter drill bit off and pore size, etc., the clamping force will cause the actual speed is not good Set speed does not match between the chuck and the drill bit slipping.
7, fixed shank drill head clamping collet drill shank length of 4 to 5 times the diameter to clamp securely.
8, should always check the spindle presser foot. Presser foot contact surface perpendicular to the spindle is horizontal and not shaking, to prevent drilling off the drill and produce partial holes.
9, drilling better than vacuuming, vacuum air temperature can be reduced drill, colleagues away dust reduce friction generates heat.
10, the substrate stack comprises upper and lower plate to drill a hole workbench trough positioning system to locate a prison, lie flat. Use adhesive tape to prevent the drill bit to be on the tape so that a drill swarf adhesion, causing difficulties and chip off the diamond.
11, ordering manufacturers drill, the factory inspection when sampling the compliance of its 4%. And 100% of 10 to 15 times with a microscopic examination of the gaps, scratches and cracks.
12, drill timely re-grinding, increase the use and re-drill grinding times, extending bit life, reduce production costs and expenses. Microscope usually measured length of the two main cutting edges, the wear depth should be less than 0.2mm. Regrinding when rubbed 0.25mm. Plain shank drill can be reground three times, shovel-shaped head (undercut) of the drill can be reground two times. Excessive turning grinding quality and accuracy of its drilling will decline, will cause the finished circuit board scrap. Excessive turning mill backfired.
13, when the wear due to abrasion and diameter reduction of 2% compared to the original, then the bit scrapped.
14 bit parameter settings in general, manufacturers have to provide a drill bit plant production speed and lower speed parameter table, the parameter is a reference only, the actual craft workers through actual use but also draw a line with The actual speed and the speed of the drill parameters are usually the reference parameter actual parameters are different but the difference is not too much.
The concept of drill
Bit is used to drill out the solid material through holes or blind holes, and is able to have a hole reaming tools. Twist drills are commonly used, flat drill, center drill, deep hole drilling and core drill. Reamers and countersinks although not drill holes in solid material, but will also be used to drill them into a class.
Flat drill
Cutting portion of the drill flat spade, simple structure, low cost, easily cutting fluid into the hole, but the cutting and chip performance is poor. Flat structure integral drill and assembly two. Integral mainly for drilling diameter of 0.03 to 0.5 mm pores. Fabricated flat diamond blade can be changed, can be cooled, mainly for the drilling diameter 25 to 500 mm large hole.
Deep hole drilling
Deep hole drilling is typically the machining hole depth is greater than the diameter of the bore of the tool 6. Commonly used gun drilling, BTA deep hole drilling, jet drill, DF deep hole drilling. Nesting also used in drilling deep holes.
Reamer
Reamer has three to four teeth, better rigidity than the twist, to expand the existing hole and improve the machining accuracy and finish.
Countersink
Countersinks have more teeth to the end of the hole forming method processed into the desired shape, for processing a variety of countersunk head screws countersunk holes, holes or flattened outer end face.
Center drill
Center drill for drilling holes shaft center of the diamond bandsaw blades workpiece, it is essentially a small twist by the helix angle and countersink drill composite, so called composite center drill.
Bit Structure
A drill, comprising a shank (1), a tip shank, the tip has two in a main plane (C-C) on the cutting insert (5,5 '), said cutting blade (5,5 ') having a second common plane (E-E) is oriented to the center of the short cutting edges. Said blade forms a point-like central cutting edges used to enter the workpiece, and thus the bit pair. In the arbor, the establishment of two flutes (6,6 '), the flute (6,6') extending from the tip end in the end. Any length along the surface of the arbor, the flutes are in the plane of the tube diametrically opposite positions to each other, the tube plane of the two sides of the tube with a common edge with a flat blade (F-F) to 90 ° extends in the plane of the shank has a maximum rigidity. Center cutting edge of the second plane (E-E) in alignment with the blade shank with a flat bottom or main rigidity direction (F-F) at approximately a 90 ° angle.
One kind of concrete, etc. in drilling operations, drilling state can ease the situation suddenly changed, so that drilling operations stable, even in large grain chips produced when drilling efficiency is not caused by lowering of the drill.
Configuration which substantially radial cutting edge portion having at least two main cutting edge portion, and arranged in the circumferential direction of said main cutting edge portion and between the main cutting edge portion, at least two sub cutting blade portion said main cutting edge portion includes a main cutting edge as the cutting blade, the cutting blade inner end of the main center of rotation, the outer end of the cutting edge portion in the outer periphery of the rotation locus.
A cutting edge portion of the sub cutting blade as the sub cutting blade, the sub cutting blade inner end is located off the center of rotation to the outer side of the site, the outer end is located in the rotating cutting blade portion deviated from the center of rotation locus of the outer edge position.
A drill, with a drill tip disposed on the plurality of cutting blade portion, and provided on the base end side of the cutting blade portion and the base end portion of the shank portion is formed with a shaft-shaped drill main body;
Said cutting blade portion has a flank of the cutting surface and the engagement surface protruding toward the front end edge of the cutting edge formed by said center of rotation of the cutting blade from the drill side arranged substantially radially outer side;
The rotary axis of the direction of movement and the operation of the impact operation of cutting the composite, characterized in that said cutting blade portion has at least two main cutting edge portion, and disposed in the circumferential direction of the ring saw blades main cutting edge portion and the main cutting between the blade, at least two sub cutting blade portion;
The main cutting edge portion having a cutting edge as a main cutting edge, an inner end of said main cutting edge is located in the center of rotation, the outer end of the cutting edge portion in the outer periphery of the rotation locus, the sub cutting blade portion having as its the sub cutting blade cutting edge, the secondary cutting blade inner end is located radially outwardly from the rotation center deviate from the site, the outer end portion in the rotation from the cutting edge to the center of rotation locus of the outer side of the deviated position.
PDC bits
PDC bits [1] for short. Is commonly used in the oil drilling industry as a drilling tool.
PDC continuous improvement of product performance
In the past few years, PDC cutter quality and type have undergone tremendous changes. If the teeth of the 1980s to today's teeth for comparison, the difference is quite large. Because hybrid technology and manufacturing process changes, today's cutting teeth is much better quality and performance, so that the anti-erosion and impact drill capabilities are greatly improved.
Engineers also tungsten carbide substrate and the interface between the diamond has been optimized to improve the toughness of the cutting teeth. Process innovations in the diamond layer is also used to improve the abrasion resistance and thermal stability.
In addition to material and manufacturing process developments outside, PDC products in the tooth tooth design techniques and fabric also achieved a major breakthrough. Now, PDC products have been used previously can not be applied in areas such as stiffer, stronger and changing abrasive formations. This extension to new areas, the diamond (fixed cutter) cone drill bit and the balance between a great impact.
Initially, PDC drill bit can only be used for soft shale formations, the reason is hard mezzanine will damage the drill bit. However, due to the emergence of new technologies and changes in the structure, the current PDC drill bit for drilling hard interlayer has been able to and a long section of the hard rock formations. PDC bits are increasingly being used by people, especially with the continuous improvement of quality PDC teeth, in which case more and more prominent.
Since teeth bit design and improvement, PDC drill bit orientability also will increase, which further weakened the past in motor drilling cone bit advantage. Currently, PDC drill every day in many applications where the drilling supplant cone drill bit market.
Commonly used mechanical drills, twist drills with straight shank (ordinary type), you can drill: 45 # steel, stainless steel, diamond hardness using the weak point of the material. Alloy drill, you can drill Cr12 steel, the use of diamond hardness strong material. Use drill expertise can allow himself to lower profits.
PCB Drill Type
PCB drill drill drill control Type: PCB drilling with a drill with straight shank twist drill, fixed and fixed shank twist drill shank Spade (undercut) drill bit. Straight shank twist drill mostly for single head machines, PCB drilling relatively simple or single panel, now in a large circuit board manufacturing plant has been rarely seen in its drilling depth of up to 10 times the diameter of the drill. Laminated on the substrate is not high, the use of drill bit holder to avoid bias.
At present, most manufacturers use CNC drilling machine, CNC drilling using a carbide shank drill set, which is characterized to achieve automatic replacement drill. High positioning accuracy without the use of drill sets. Large helix angle, chip speed, suitable for high-speed cutting. In the range of the flute length, diameter of the drill is an inverted cone, when drilling with the hole wall friction is small, high quality drilling. Common drill shank diameter of 3.00mm and 3.175mm.
Drill material
PCB drilling with carbide drill bit is generally used as the epoxy glass cloth complex copper plate on the tool wear particularly fast. The so-called carbide drill gold is tungsten carbide powder as matrix, cobalt powder as a binder by pressurized sintering. Generally contain 94% tungsten carbide, 6% cobalt. Because of its high hardness, very wearable, a certain strength, suitable for high-speed cutting. But the toughness is poor, very brittle, in order to improve the performance of cemented carbide, and some use carbide substrate in a chemical vapor deposition on a 5-7 micron layer of special hard titanium carbide (TIC) or titanium nitride (TIN), to has a higher hardness. Some use ion implantation technology, titanium, nitrogen, and carbon injection the matrix certain depth, not only improves the hardness and strength and regrinding the drill can move into when they injected ingredients. There is a physical method to generate the bit at the top of a layer of diamond film, which greatly improves the hardness and wear resistance of the drill. Carbide hardness and strength, not only the ratio of cobalt and tungsten carbide, but also with the powder particles about. Carbide drill ultra fine particles, and its average grain size of tungsten carbide with 1 micron or less. This bit is not only high hardness and compressive strength and flexural strength are improved. To save costs Many drill shank welded structure, the original as a whole are carbide drill, drill shank back now made of stainless, but significantly reduced the cost of the material due to different concentricity less than its dynamic rigid whole alloy drill, particularly in the small diameter side.
The use of drill
1, the drill should be packed in special packing boxes, to avoid vibrations collide.
2, when used, from packing boxes should immediately remove the drill bit attached to the spindle collet header or automatic replacement drill tool library. Spent immediately put back packing boxes.
3, use the drill diameter measurement tool microscope and other non-contact measurement equipment, to avoid the cutting edge in contact with the mechanical gauge was bruised.
4, some CNC drilling machine CNC drilling using some positioning ring retaining ring is not used, such as the use of its positioning ring installation depth positioning must be accurate, as it does not use retaining ring fitted to the drill spindle elongation to adjust consistent, multi-spindle drilling machine to pay attention to this point, to make each spindle drilling depth to be consistent. If not possible to make drill drill drill through the surface or not caused by circuit board scrap.
5, using 40 times the usual three-dimensional microscopy drill blade wear.
6, the spindle and to always check the concentricity of the collet and the collet chuck clamping force, will result in poor concentricity of small diameter drill bit off and pore size, etc., the clamping force will cause the actual speed is not good Set speed does not match between the chuck and the drill bit slipping.
7, fixed shank drill head clamping collet drill shank length of 4 to 5 times the diameter to clamp securely.
8, should always check the spindle presser foot. Presser foot contact surface perpendicular to the spindle is horizontal and not shaking, to prevent drilling off the drill and produce partial holes.
9, drilling better than vacuuming, vacuum air temperature can be reduced drill, colleagues away dust reduce friction generates heat.
10, the substrate stack comprises upper and lower plate to drill a hole workbench trough positioning system to locate a prison, lie flat. Use adhesive tape to prevent the drill bit to be on the tape so that a drill swarf adhesion, causing difficulties and chip off the diamond.
11, ordering manufacturers drill, the factory inspection when sampling the compliance of its 4%. And 100% of 10 to 15 times with a microscopic examination of the gaps, scratches and cracks.
12, drill timely re-grinding, increase the use and re-drill grinding times, extending bit life, reduce production costs and expenses. Microscope usually measured length of the two main cutting edges, the wear depth should be less than 0.2mm. Regrinding when rubbed 0.25mm. Plain shank drill can be reground three times, shovel-shaped head (undercut) of the drill can be reground two times. Excessive turning grinding quality and accuracy of its drilling will decline, will cause the finished circuit board scrap. Excessive turning mill backfired.
13, when the wear due to abrasion and diameter reduction of 2% compared to the original, then the bit scrapped.
14 bit parameter settings in general, manufacturers have to provide a drill bit plant production speed and lower speed parameter table, the parameter is a reference only, the actual craft workers through actual use but also draw a line with The actual speed and the speed of the drill parameters are usually the reference parameter actual parameters are different but the difference is not too much.
The concept of drill
Bit is used to drill out the solid material through holes or blind holes, and is able to have a hole reaming tools. Twist drills are commonly used, flat drill, center drill, deep hole drilling and core drill. Reamers and countersinks although not drill holes in solid material, but will also be used to drill them into a class.
the life of high speed steel circular saw blades
In order to maximize the reduction of the consumption of high-speed steel circular saw blades, each blade reduces cutting costs, increase plant productivity, the actual situation of the sds hammer drill bits following applications for the proposal wants to follow:
1, the new blade test run:
To ensure long life, so that circular saws with a new blade (or replace the blade after each grinding) have a full running-in process, the cutting begins within 10 minutes, reducing the feed rate is very necessary The. The next 10 minutes before gradually speed up;
2, cutting and feed rate:
Cutting speed depends on the concrete ring saw material being cut sections and toughness, this is difficult for cutting stainless steel, high toughness of the material, the slower the speed is very beneficial to increase blade life. When the material cross section is small, can be an appropriate increase in engine speed;
3, correct and timely grinding blade:
Blade during operation, due to the dry cut blades role of external forces, the blade pitch and yaw rate, stress, etc. has changed, so there will be larger road saws; surface roughness, clip blade and other phenomena; timely grinding blade, serrated blade to re-raise the angle, pitch accuracy, high-speed steel circular saw blades will increase the use of results;
4, you can judge sawdust observe the current state of cutting blade;
a, very fine sawdust or powdered cutting pressure indicates the size;
b, of a soft cut sawdust that overload;
c, long spiral wire sawdust expressed in good condition;
1, the new blade test run:
To ensure long life, so that circular saws with a new blade (or replace the blade after each grinding) have a full running-in process, the cutting begins within 10 minutes, reducing the feed rate is very necessary The. The next 10 minutes before gradually speed up;
2, cutting and feed rate:
Cutting speed depends on the concrete ring saw material being cut sections and toughness, this is difficult for cutting stainless steel, high toughness of the material, the slower the speed is very beneficial to increase blade life. When the material cross section is small, can be an appropriate increase in engine speed;
3, correct and timely grinding blade:
Blade during operation, due to the dry cut blades role of external forces, the blade pitch and yaw rate, stress, etc. has changed, so there will be larger road saws; surface roughness, clip blade and other phenomena; timely grinding blade, serrated blade to re-raise the angle, pitch accuracy, high-speed steel circular saw blades will increase the use of results;
4, you can judge sawdust observe the current state of cutting blade;
a, very fine sawdust or powdered cutting pressure indicates the size;
b, of a soft cut sawdust that overload;
c, long spiral wire sawdust expressed in good condition;
2013年8月9日星期五
diamond saw some important influence
1, stone mining technology and equipmentAt present, China still has a lot of stone mines using drill blasting this backward approach to the production of stone blocks, not only productive but also job insecurity, especially due to detonation caused by rock rupture, severely damaged the diamond blade saws stone resources, produced irregular size of blocks, or even scrapped due to a crack, finished product rate is very low. It is estimated, using drill blasting method mining blocks only 5% to 8% of the extraction can be processed timber. The early 1980s, a number of stone industrialized countries have banned use of blasting mining stone and replaced diamond wire saws and other advanced technologies. Stone can say this is a sign of modern mining technology. The masonry saw blades stone mining techniques to measure an important indicator of the degree of modernization is: day number of cubic meters per capita mining blocks. The industry believes that China International Chamber of stone mine production is low. The reason is the lack of mechanized equipment, mining technology behind the production mismanagement. The average annual number of mined stone mines only a few hundred to several thousand cubic meters, a few mining of stone mines in more than 10,000 cubic meters, annual per capita yield of 6 m3. . Equivalent to the monthly per capita production is only 0.5 m3, lower than India. As we all know, India is also the largest producer of stone. But it's granite mines are small, no modern equipment, so stone blocks low productivity. Day per capita is only 1 m3. Finland is one of the Scandinavian countries, the largest stone exporter. Its granite mine production system is world class, the dry polishing pads annual export of granite at least 25 million metric tons, up to date mine production efficiency per 40 m3. Stone mines in South Africa is a middle level of productivity, daily per capita 8-10 m3.
① assembling high cost, which is about four times the diamond wire saws;
② operating personnel, need at least two person operation. Replacement blade more people when they co-operation;
③ sawing slow, old-fashioned frame saws cutting speed is only 2cm / h. New framework for cutting speed but also 3.5-3.8 cm / h. While diamond wire saw cutting speeds of up to 20cm / h, may be increased to 30cm / h;
④ Frame Sawing sheet rough surface, flatness is also poor, so polished low speed, as 100cm/min, while Diamond Wire Sawing sheet surface is smooth, polished speeds of up to 160 cm / min , thus reducing the grinding and polishing process time;
⑤ energy consumption and material consumption is higher;
⑥ scrap disposal and mortar workplace dust causing serious environmental pollution.
① assembling high cost, which is about four times the diamond wire saws;
② operating personnel, need at least two person operation. Replacement blade more people when they co-operation;
③ sawing slow, old-fashioned frame saws cutting speed is only 2cm / h. New framework for cutting speed but also 3.5-3.8 cm / h. While diamond wire saw cutting speeds of up to 20cm / h, may be increased to 30cm / h;
④ Frame Sawing sheet rough surface, flatness is also poor, so polished low speed, as 100cm/min, while Diamond Wire Sawing sheet surface is smooth, polished speeds of up to 160 cm / min , thus reducing the grinding and polishing process time;
⑤ energy consumption and material consumption is higher;
⑥ scrap disposal and mortar workplace dust causing serious environmental pollution.
订阅:
博文 (Atom)